Efficient Integration of Template Matching, Calibration and Triangulation for Automating Peg Hole Insertion Task Using Two Cameras
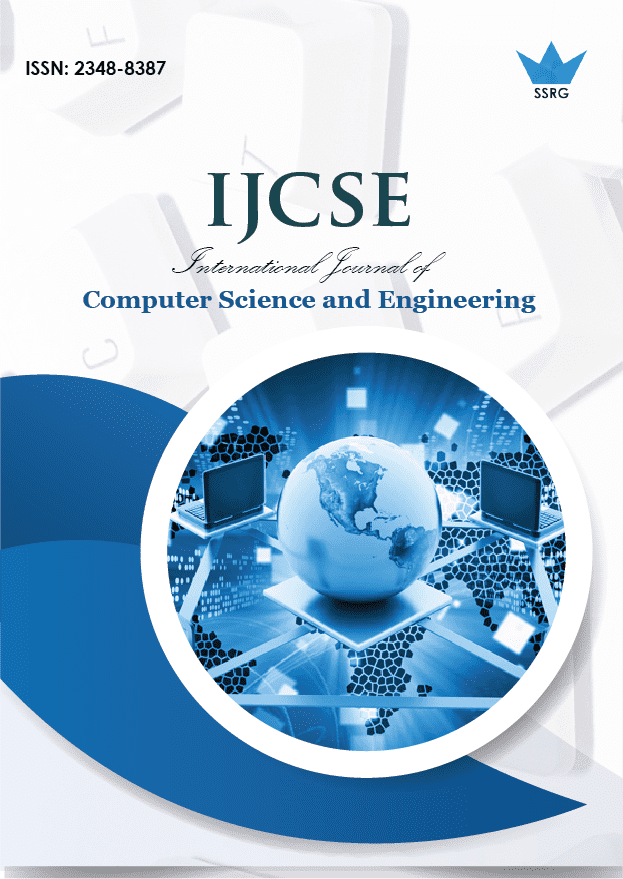
International Journal of Computer Science and Engineering |
© 2016 by SSRG - IJCSE Journal |
Volume 3 Issue 11 |
Year of Publication : 2016 |
Authors : Andres Sauceda Cienfuegos, Baidya Nath Saha, Jesus Romero-Hdz, David Ortega |
How to Cite?
Andres Sauceda Cienfuegos, Baidya Nath Saha, Jesus Romero-Hdz, David Ortega, "Efficient Integration of Template Matching, Calibration and Triangulation for Automating Peg Hole Insertion Task Using Two Cameras," SSRG International Journal of Computer Science and Engineering , vol. 3, no. 11, pp. 1-5, 2016. Crossref, https://doi.org/10.14445/23488387/IJCSE-V3I11P112
Abstract:
This paper integrates template matching, calibration and triangulation algorithms in an efficient way to automate peg-hole insertion task using a pair of cameras. First we implement a fast template matching (fast correlation based block matching) algorithm for automatically finding the peg and hole using two cameras. We exploit the templates of the peg and hole at different orientation and illumination to improve the accuracy of the template matching algorithm. Then we implement the Direct Linear Transform (DLT) method based calibration algorithm to find the intrinsic and extrinsic parameters of the camera. We then refine the camera calibration parameters through Levenberg-Marquardt (LM) based non-linear optimization method. We used two cameras to prevent the occlusion of peg and hole occurred due to robot movement and to reduce calibration error. Finally we implement a DLT based triangulation method to find the three dimensional world coordinates of the peg and hole from the images captured by two cameras. We use square and circular grids to reduce triangulation error. For triangulation method similar feature points of two images are matched through Harris corner detection for square and sift features for circular grids. Optimum camera parameters for triangulation method are determined based on minimum rectification based calibration error. We conducted the experiment on gantry robot. Experimental results demonstrate that efficient integration of template matching, calibration and triangulation method can successfully automate peg hole insertion task.
Keywords:
Direct Lineal Transformation, Template Matching Algorithm, Harris corner detection, SIFT, Levenberg-Marquardt Algorithm, Triangulation method, peg-hole insertion task, gantry robot.
References:
[1] A. Mahmood, and S. Khan, “Early termination algorithms for correlation coefficient based block matching,” In: Proceedings of the International Conference on Image Processing, ICIP, pp. II 469– II472 , 2007.
[2] L. Di Stefano, S. Mattoccia,, and F. Tombari, “Zncc-based template matching using bounded partial correlation,” Pattern Recognition Letters, vol. 26, pp. 2129-2134, 2005.
[3] Choi, J.W., Fang, T.H., Yoo, W.S., Lee, M.H., “Sensor data fusion using perception net for a precise assembly task.” IEEE/ASME transactions on mechatronics 8(4), 513–516 (2003).
[4] Kim, J., Cho, H.S., “Visual sensor-based measurement for deformable peg-in-hole tasks.” In: Intelligent Robots and Systems, 1999. IROS’99. Proceedings. 1999 IEEE/RSJ International Conference on. vol. 1, pp. 567–572. IEEE (1999).
[5] Xue, G., Fukuda, T., Arai, F., Asama, H., Kaetsu, H., Endo, I., “Dynamically reconfigurable robotic system assembly of new type cells as a dual-peg-in-hole problem.” In: Distributed Autonomous Robotic Systems, pp. 383–394. Springer (1994).
[6] Newman,W.S., Zhao, Y., Pao, Y.H., “Interpretation of force and moment signals for compliant peg-in-hole assembly.” In: Robotics and Automation, 2001. Proceedings 2001 ICRA. IEEE International Conference on. vol. 1, pp. 571–576. IEEE (2001).
[7] Hartley, R.,I. and Zisserman, A., ”Multiple View Geometry in Computer Vision”, Cambridge University Press, 2004 [8] Tian Shao-xiong, Lu Shan, Liu Zong-ming, “Levenberg-Marquardt Algorithm Based Nonlinear Optimization of Camera Calibration for Relative Measurement” Proceedings the 34th Chinese Control Conference, 2015
[9] Bradley, Derek, Wolfgang Heidrich “Binocular Camera Calibration Using Rectification Error”, In: CRV, IEEE Computer Society, pp. 183-190, 2010
[10] Zhang, X., He, G., & Yuan, J. (2009, October). “A rotation invariance image matching method based on Harris corner detection.” In: Image and Signal Processing, 2009. CISP'09. 2nd International Congress on (pp. 1-5). Ieee.
[11] Fusiello, A., Trucco, E., & Verri, A. (2000). “A compact algorithm for rectification of stereo pairs.” Machine Vision and Applications, 12(1), 16-22.
[12] Lewis, J. P. "Fast normalized cross-correlation." Vision interface. Vol. 10. No. 1. 1995.
[13] Lowe, David G. "Distinctive image features from scale-invariant keypoints."International journal of computer vision 60.2 (2004): 91-110.
[14] Daehie Hong, Woo-Chang Lee, Baeksuk Chu, Tae-Hyung Kim, Woo Chun Choi “Gantry Robot with Extended Workspace for Pavement Sign Painting Operations." International Journal of Precision Engineering and Manufacturing 9.3 (2008): 85-91.
[15] Shapiro, Robert. "Direct linear transformation method for three-dimensional cinematography." Research Quarterly. American Alliance for Health, Physical Education and Recreation 49.2 (1978): 197-205.
[16] T. Hastie, R. Tibshirani, and J. Friedman, “The Elements of Statistical Learning, Data Mining, Inference, and Prediction,” Second Edition, 2008.
[17] J. D. Ratcliffe, P. L. Lewin, E. Rogers, J. J. Hätönen, and D. H. Owens, “Norm-Optimal Iterative Learning Control Applied to Gantry Robots for Automation Applications,” IEEE Transactions on Robotics, vol. 22, no. 6, pp. 1303–1307, 2006.
[18] L. Balletti, A. Rocchi, F. Belo, M. Catalano, M. Garabini, G. Grioli, and A. Bicchi, “Towards variable impedance assembly : the VSA peg-in-hole.” , IEEE-RAS International Conference on Humanoid Robots (Humanoid), pp. 504-508, 2012.