On The Mechanical Aspects Concrete Containing Mill Scale
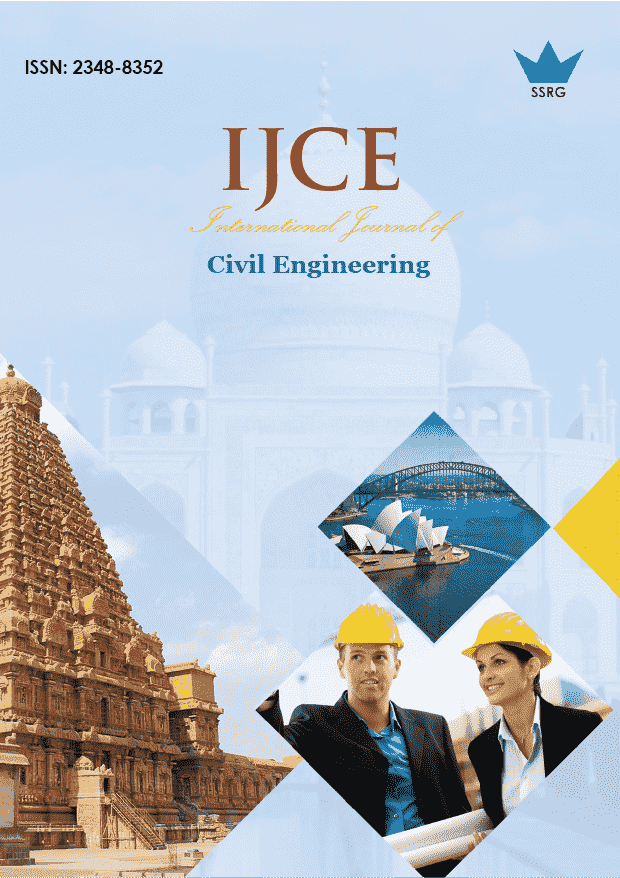
International Journal of Civil Engineering |
© 2021 by SSRG - IJCE Journal |
Volume 8 Issue 8 |
Year of Publication : 2021 |
Authors : Yogesh Iyer Murthy |
How to Cite?
Yogesh Iyer Murthy, "On The Mechanical Aspects Concrete Containing Mill Scale," SSRG International Journal of Civil Engineering, vol. 8, no. 8, pp. 23-34, 2021. Crossref, https://doi.org/10.14445/23488352/IJCE-V8I8P103
Abstract:
The current paper experimentally investigates the effects of partial replacement of fine aggregate by mill scale in concrete in varying proportions by weight. Mill scale was added by weight of fine aggregate with partial replacement of 0%, 10%, 20%, 30%, 40%, 50% and 60% and using Portland Pozzolana Cement in C20/25 grade of concrete. The physical and mechanical properties of concrete so produced were evaluated. The fresh concrete produced showed a drastic reduction of slump with increasing percentage replacement with 74% reduction at 60% replacement compared to the control mix. Further, the compressive, flexural and split tensile strength also showed a drop in strength by 34.5%, 27% and 19% with respect to control mix for 60% replacement respectively. From the microstructural studies, it could be concluded that mill scale acts as a filler material and can be used as partial replacement of sand effectively up to 40% by weight of cement in concrete.
Keywords:
Mill Scale, concrete aggregates, physical and mechanical properties, durability, waste utilization.
References:
[1] World Steel Association. 2019. Global crude steel output in 2018. Accessed March 21, 2019. https://www.worldsteel.org/.
[2] Eissa M., Ahmed A., and El-Fawkhry M. Conversion of mill scale waste into valuable products via carbothermic reduction. Journal of Metallurgy, (2015) 1-9.
[3] Murthy Y.I., Stabilization of expansive soil using mill scale. International Journal of Engineering , Science and Technology, 3(4) (2012) 143-147.
[4] Cho S. and Lee J., Metal recovery from stainless steel mill scale by microwave heating. Metals and materials international, 14(2) (2008) 193-196.
[5] Bagatini, M.C., Zymla, V., Osório, E. and Vilela, A.C.F., Characterization and reduction behavior of mill scale. ISIJ international, 51(7) (2011) 1072-1079. [6] Matsushita, K., Tateishi, M., Tanaka, H. and Harada, T., Kobe Steel Ltd,. Method for producing reduced iron agglomerates. U.S. Patent 6,254,665 (2001).
[7] R. D. Young and D. Norris, Process for using mill scale in cement clinker production, US Patent, no. 6709510B1, (2004).
[8] L. Camci, S. Aydin, and C. Arslan, Reduction of iron oxide in solid wastes generated by steelworks, Turkish Journal of Engineering and Environmental Sciences, 26 (2002) 37–44.
[9] Legodi, M.A. and De Waal, D,. The preparation of magnetite, goethite, hematite and maghemite of pigment quality from mill scale iron waste. Dyes and Pigments, 74(1) (2007) 161-168.
[10] Al-Otaibi, S. Recycling steel mill scale as fine aggregate in cement mortars. European Journal of Scientific Research, 24(3) (2008) 332-338.
[11] Pradip, M.S., Vaidyanathan, D., Panjwani, A. and Kapur, P.C., December. CT Manufacture of energy efficient hydraulic cements from industrial and mining waste materials. In Proceedings of Conference on Mineral Processing: Recent Advances and Future Trends, Kanpur (1995) 816-823.
[12] Pereira, F.M., Verney, J.C.K.D. and Lenz, D.M.,. Evaluation of the use of mill scale as fine aggregate in concrete. Rem: Revista Escola de Minas, 64(4) (2011) 463-469.
[13] Singhal, A., Bhunia, D. and Pandel, B. Effect o f Sand Replacement by Mill Scale on the Properties of Concrete. International Journal of Engineering Technology and Scientific Research (2015) 60-67.
[14] Li, Y.F., Yao, Y. and Wang, L.,. Recycling of industrial waste and performance of steel slag green concrete. Journal of Central South university of technology, 16(5) (2009) 768.
[15] Manso, J.M., Gonzalez, J.J. and Polanco, J.A.,. Electric arc furnace slag in concrete. Journal of materials in civil engineering, 16(6) (2004) 639-645.
[16] Muhmood, L., Vitta, S. and Venkateswaran, D.,. Cementitious and pozzolanic behavior of electric arc furnace steel slags. Cement and Concrete Research, 39(2) (2009) 102-109.
[17] Zhao, J.; Wang, D.; Yan, P. Design and experimental study of a ternary blended cement containing high volume steel slag and blast-furnace slag based on Fuller distribution model. Constr. Mater, 140 (2017) 248–256.
[18] Lee, J.Y., Choi, J.S., Yuan, T.F., Yoon, Y.S. and Mitchell, D., Comparing Properties of Concrete Containing Electric Arc Furnace Slag and Granulated Blast Furnace Slag. Materials, 12(9) (2019) 1371.
[19] IS 1489 (Part-1): 2015, Specification for Portland pozzolana cement : Flyash based, Bureau of Indian Standards (BIS), New Delhi, India.
[20] IS 10500: 2012 Indian Standard Drinking Water-Specification (Second revision). Bureau of Indian Standards (BIS), New Delhi.
[21] IS: 10262-2009, Recommended Guidelines for Concrete Mix Design. Bureau of Indian Standards (BIS), New Delhi, India.
[22] IS 7320, Specification for concrete slump test apparatus. Bureau of Indian Standards (BIS), New Delhi, India.
[23] IS: 1199: 1959. Methods of sampling and analysis of concrete.
[24] IS:13311(Part-1):1992, Non Destructive testing of Concrete-Methods of test." Bureau of Indian Standards (BIS), New Delhi, India.
[25] Azad, A. M., and Kesavan, S. Enviro-friendly hydrogen generation from steel mill-scale via metal-steam reforming, Bulletin of Science, Technology & Society, 26(4) (2006) 305-313.
[26] IS 1727:1967, Indian Standard Methods of Test for pozzolanic Materials, Bureau of Indian Standards, New Delhi.
[27] IS: 1199-1959. Indian Standard Methods of Sampling and analysis of concrete. Bureau of Indian Standards, New Delhi.
[28] IS 456-2000 (2000) Indian Standard Plain and Reinforced Concrete Code of Practice. Bureau of Indian Standards, New Delhi.
[29] Erdoğan, T. Concrete. – METU Press Publishing Company, Turkey, 2003. P. 741 [in Turkish]
[30] Papadakis, Vagelis G., Michael N. Fardis, and Costas G. Vayenas. Hydration and carbonation of pozzolanic cements. Materials Journal, 89(2) (1992) 119-130.
[31] Gonen, Tahir, and Salih Yazicioglu., The influence of mineral admixtures on the short and long-term performance of concrete." Building and Environment, 42(8) (2007) 3080-3085.
[32] Demirel, B. The effect of the using waste marble dust as fine sand on the mechanical properties of the concrete . International journal of physical sciences 5(9) (2010) 1372-1380.
[33] IS:516 1991, Methods of test for strength of concrete. Bureau of Indian Standards (BIS), New Delhi, India.
[34] ACI Committee 318. Building Code Requirements for Structural Concrete, American Concrete Institute, 2011.
[35] Topcu IB. Statistics in Civil Engineering. Eskiehir, (2006) 153-162.
[36] Topcu, Bekir I., Bilir T., and Uygunoğlu T. Effect of waste marble dust content as filler on properties of self-compacting concrete. Construction and Building Materials, 23(5) (2009) 1947-1953.