Experimental Investigations on Mechanical Properties of Alkali Activated Coarse Aggregate in Concrete
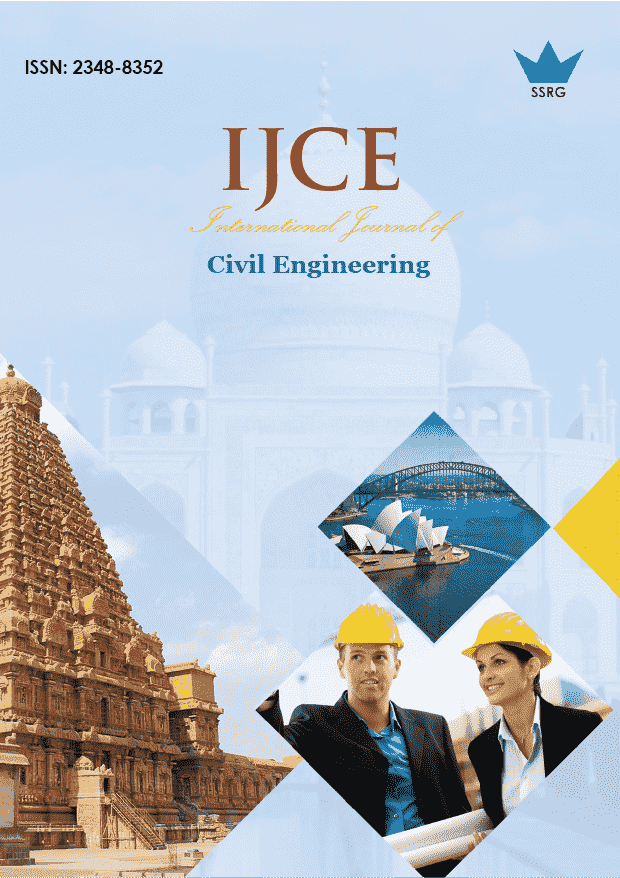
International Journal of Civil Engineering |
© 2022 by SSRG - IJCE Journal |
Volume 9 Issue 10 |
Year of Publication : 2022 |
Authors : M. P. Naveena, G. Narayana |
How to Cite?
M. P. Naveena, G. Narayana, "Experimental Investigations on Mechanical Properties of Alkali Activated Coarse Aggregate in Concrete," SSRG International Journal of Civil Engineering, vol. 9, no. 10, pp. 1-6, 2022. Crossref, https://doi.org/10.14445/23488352/IJCE-V9I10P101
Abstract:
The present study focused on developing Alkali Activated Fine Aggregate (AAFA) by palletization method. AAFA was manufactured using Ground Granulated Blast Furnace Slag (GGBS) and alkali activator solution at ambient conditions. Sodium hydroxide of six molarity and sodium silicate to sodium hydroxide ratio of 2.5 was used. AACA's properties are similar to Natural Aggregate except for flakiness and elongation index. The water absorption and Abrasion value have high for AACA compared to natural aggregate. The slump value is an increase in replacement level up to 40% replacement of AACA by Natural aggregate further replacement level there are decrees in a slump. Compressive, Split, and Flexural strength has shown noticeable strength increase for all replacement levels of AACA by natural aggregate. However, beyond the increase of 40 % replacement level, there is a decrease in strength. It may be attributed to the reduced bond between aggregate and paste
Keywords:
Pellitization, Molarity, Strength, GGBS.
References:
[1] K. Ganesh Babu, and V. Sree Rama Kumar, “Efficiency of GGBS in Concrete,” Cement and Concrete Research, vol. 30, no. 7, pp. 1031–1036, 2000. Crossref, http://doi.org/10.1016/S0008-8846(00)00271-4
[2] P. Saranya, P. Nagarajan, and A. P. Shashikala, “Eco-Friendly GGBS Concrete: A State-of-the-Art Review,” IOP Conference Series: Materials Science and Engineering, vol. 330, no. 1, 2018. Crossref, http://doi.org/10.1088/1757-899x/330/1/012057
[3] V. R. P. Kumar, K. Gunasekaran, and T. Shyamala, “Characterization Study on Coconut Shell Concrete with Partial Replacement of Cement By GGBS,” The Journal of Building Engineering, vol. 26, 2019. Crossref, http://doi.org/10.1016/J.Jobe.2019.100830
[4] Sanjay R. Salla, Chetankumar D. Modhera, and Uppara Raghu Babu, “An Experimental Study on Various Industrial Wastes in Concrete for Sustainable Construction,” Journal of Advanced Concrete Technology, vol. 19, no. 2, pp. 133–148, 2021. Crossref, http://doi.org/10.3151/JACT.19.133
[5] Nguyen Thanh Sang, and Nguyen Tan Khoa, “Experimental Study on the Effect of Ground Granulated Blast Furnace Slag of Strength and Durability of Sand Concrete,” Lecture Notes in Civil Engineering, vol. 54, no. 7, pp. 409–414, 2020. Crossref, http://doi.org/10.1007/978-981-15-0802-8_63
[6] Reshma Malipeddi, and S.Adiseshu, “Study of Dissolution Parameter of Ground Granulated Blast Furnace Slag As Cement Replacement on Mechanical Properties of Mortar,” Materials Today: Proceedings, vol. 44, pp. 642–650, 2021. Crossref, http://doi.org/10.1016/J.Matpr.2020.10.605
[7] V. Arularasi, et al., “Rheological Behavior and Strength Characteristics of Cement Paste and Mortar with Fly Ash and Ggbs Admixtures,” Sustainability, vol. 13, no. 17, 2021, Crossref, http://doi.org/10.3390/Su13179600
[8] Ismael Justo-Reinoso, Wil V.Srubar, et al., “Fine Aggregate Substitution By Granular Activated Carbon Can Improve Physical and Mechanical Properties of Cement Mortars,” Construction and Building Materials, vol. 164, pp. 750–759, 2018. Crossref, http://doi.org/10.1016/J.Conbuildmat.2017.12.181
[9] Subhashree Samantasinghar, and Suresh Prasad Singh, “Fresh and Hardened Properties of Fly Ash–Slag Blended Geopolymer Paste and Mortar,” the International Journal of Concrete Structures and Materials, vol. 13, no. 1, pp. 1–12, 2019. Crossref, http://doi.org/10.1186/S40069-019-0360-1
[10] Anuja Narayanan, and Prabavathy Shanmugasundaram, “An Experimental Investigation on Flyash-Based Geopolymer Mortar Under Different Curing Regime for Thermal Analysis,” Energy Building, vol. 138, pp. 539–545, 2017. Crossref, http://doi.org/10.1016/J.Enbuild.2016.12.079
[11] A. M. N. Kashyap, P. Varalakshmi, and T. C. Rao, “Influence of Alkali Concentration on Strength Characteristic of Ggbs Based Geopolymer Mortar,” Researchgate.Net, no. 4, pp. 9–12, 2018.
[12] Lizia Thankam Gnanadurai, Neelakantan Thruvas Renganathan, and Christopher Gnanaraj Selvaraj, “Synthesis and Characterization of Synthetic Sand By Geopolymerization of Industrial Wastes (Fly Ash and GGBS) Replacing the Natural River Sand,” Environmental Science and Pollution Research, vol. 28, no. 40, pp. 56294–56304, 2021. Crossref, http://doi.org/10.1007/S11356-021-14223-8
[13] U. S. Agrawal, S. P. Wanjari, and D. N. Naresh, “Characteristic Study of Geopolymer Fly Ash Sand as a Replacement to Natural River Sand,” Construction and Building Materials, vol. 150, pp. 681–688, 2017. Crossref, http://doi.org/10.1016/J.Conbuildmat.2017.06.029
[14] Lan-Ping Qian, Yan-Shuai Wang, et al., “Experimental Study on Full-Volume Fly Ash Geopolymer Mortars: Sintered Fly Ash Versus Sand As Fine Aggregates,” The Journal of Cleaner Production, vol. 263, 2020. Crossref, http://doi.org/10.1016/J.Jclepro.2020.121445
[15] Nigarila. R, Rajalakshmi. N, and Deepan Chakravarthi A.V, "Strength and Durability of Concrete Block By Partial Replacement of Cement with Granite Dust and Fine Aggregate with M-Sand," International Journal of Recent Engineering Science, vol. 7, no. 3, pp. 12-18, 2020. Crossref, https://doi.org//10.14445/23497157/IJRES-V7I3P103 M. P. Naveena & G. Narayana / IJCE, 9(10), 1-6, 2022 5
[16] S. Mundra, V. Agrawal, and R. Nagar, “Sandstone Cutting Waste as Partial Replacement of Fine Aggregates in Concrete: A Mechanical Strength Perspective,” The Journal of Building Engineering, vol. 32, no. 4, p. 101534, 2020. Crossref, https://doi.org/10.1016/J.Jobe.2020.101534
[17] K.I. Syed Ahmed Kabeer, and Ashok KumarVyas, “Experimental Investigation on Utilization of Dried Marble Slurry As Fine Aggregate in Lean Masonry Mortars,” The Journal of Building Engineering, vol. 23, no. 1, pp. 185–192, 2019. Crossref, https://doi.org/10.1016/J.Jobe.2019.01.034
[18] L Lalit Kumar Gupta, and Ashok Kumar Vyas, “Impact on Mechanical Properties of Cement Sand Mortar Containing Waste Granite Powder,” Construction and Building Materials, vol. 191, pp. 155–164, 2018. Crossref, https://doi.org/10.1016/J.Conbuildmat.2018.09.203
[19] Ji-Sun Kim, Jong-Young Lee, et al., “Evaluating the Eco-Compatibility of Mortars with Feldspar-Based Fine Aggregate,” Case Studies in Construction Materials, vol. 16, no. November 2021, p. E00781, 2022. Crossref, https://doi.org/10.1016/J.Cscm.2021.E00781
[20] P. Priyadharshini, K. Ramamurthy, and R. G. Robinson, “Influence of Temperature and Duration of Thermal Treatment on Properties of Excavated Soil as Fine Aggregate in Cement Mortar,” The Journal of Materials in Civil Engineering, vol. 31, no. 8, pp. 04019137, 2019. Crossref, https://doi.org/10.1061/(ASCE)Mt.1943-5533.0002759
[21] Vu-An Tran, Chao-Lung Hwang, and Duy-Hai Vo, “Manufacture and Engineering Properties of Cementitious Mortar Incorporating Unground Rice Husk Ash as Fine Aggregate,” The Journal of Materials in Civil Engineering, vol. 33, no. 10, pp. 04021258, 2021. Crossref, https://doi.org/10.1061/(ASCE)Mt.1943-5533.0003888
[22] Satyajit Das, Rakesh Kumar Patra, and Bibhuti Bhusan Mukharjee, “Feasibility Study of Utilisation of Ferrochrome Slag As Fine Aggregate and Rice Husk Ash As Cement Replacement for Developing Sustainable Concrete,” Innovative Infrastructure Solutions, vol. 6, no. 2, 2021. Crossref, https://doi.org/10.1007/S41062-021-00461-9
[23] K. Praveen Kumar, and X. X. Radhakrishna, “Workability Strength and Elastic Properties of Cement Mortar with Pond Ash As Fine Aggregates,” Materials Today: Proceedings, vol. 24, pp. 1626–1633, 2020. Crossref, https://doi.org/10.1016/J.Matpr.2020.04.484
[24] Branavan Arulmoly, Chaminda Konthesingha, and Anura Nanayakkara, “Performance Evaluation of Cement Mortar Produced with Manufactured Sand and Offshore Sand As Alternatives for River Sand,” Construction and Building Materials, vol. 297, 2021. Crossref, https://doi.org/10.1016/J.Conbuildmat.2021.123784
[25] S. C. Yaragal, S. N. Basavana Gowda, and C. Rajasekaran, “Characterization and Performance of Processed Lateritic Fine Aggregates in Cement Mortars and Concretes,” Construction and Building Materials, vol. 200, pp. 10–25, 2019. Crossref, https://doi.org/10.1016/J.Conbuildmat.2018.12.072
[26] Min Jae Kim, Woong Ik Hwang, and Won Jung Cho, “The Influence of Alkali Activators on the Properties of Ternary Blended Cement Incorporated with Ferronickel Slag,” Construction and Building Materials, vol. 318, no. 12, 2022. Crossref, https://doi.org/10.1016/J.Conbuildmat.2021.126174
[27] Bassirou Kone, John N. Mwero, Erick K. Ronoh, "Experimental Effect of Cassava Starch and Rice Husk Ash on Physical and Mechanical Properties of Concrete," International Journal of Engineering Trends and Technology, vol. 70, no. 3, pp. 334-341, 2022. Crossref, https://doi.org/10.14445/22315381/IJETT-V70I2P239
[28] Nanqiao You, Yong chao Liu, et al., “Rheology, Shrinkage and Pore Structure of Alkali-Activated Slag-Fly Ash Mortar Incorporating Copper Slag as Fine Aggregate,” Construction and Building Materials, vol. 242, 2020. Crossref, https://doi.org/10.1016/J.Conbuildmat.2020.118029
[29] Gaurav Singh, Souvik Das, et al., “Study of Granulated Blast Furnace Slag As Fine Aggregates in Concrete for Sustainable Infrastructure,” The Procedia - Social and Behavioral, vol. 195, pp. 2272–2279, 2015. Crossref, https://doi.org/10.1016/J.SBSPRO.2015.06.316.
[30] Zihao Liu, Koji Takasu, et al., “A Study on Engineering Properties and Environmental Impact of Sustainable Concrete with Fly Ash or GGBS,” Construction and Building Materials, vol. 316, no. 12, p. 125776, 2022. Crossref, https://doi.org/10.1016/J.Conbuildmat.2021.125776
[31] S. P. Wanjari, U. S. Agrawal, and D. N. Naresh, “Geopolymer Sand as a Replacement to Natural Sand in Concrete,” IOP Conference Series: Materials Science and Engineering, vol. 431, no. 9, 2018. Crossref, https://doi.org/10.1088/1757-899x/431/9/092011
[32] Gökhan Baykal, and Ata Gürhan Döven, “Utilization of Fly Ash by Pelletization Process; Theory, Application Areas and Research Results,” Resources, Conservation & Recycling, vol. 30, no. 1, pp. 59–77, 2000. Crossref, https://doi.org/10.1016/S0921- 3449(00)00042-2
[33] K. N. Shivaprasad, and B. B. Das, “Influence of Alkali Binder Dosage on the Efficiency of Pelletization of Aggregates from Iron Ore Tailing and Flyash,” International Journal of Engineering Research in Mechanical and Civil Engineering, vol. 2, no. 3, pp. 388–392, 2017.
[34] K. N. Shivaprasad, and B. B. Das, “Determination of Optimized Geopolymerization Factors on the Properties of Pelletized Fly Ash Aggregates,” Construction and Building Materials, vol. 163, pp. 428–437, 2018. Crossref, https://doi.org/10.1016/J.Conbuildmat.2017.12.038 M. P. Naveena & G. Narayana / IJCE, 9(10), 1-6, 2022 6
[35] Sudhakar M. Rao, and Indra Prasad Acharya, “Synthesis and Characterization of Fly Ash Geopolymer Sand,” Journal of Materials in Civil Engineering, vol. 26, no. 5, pp. 912–917, 2014. Crossref, https://doi.org/10.1061/(ASCE)Mt.1943-5533.0000880
[36] M. R. . Veeramanickam and M. Mohanapriya, “IOT Enabled Futures Smart Campus with Effective E-Learning : I-Campus,” International Journal of Engineering & Technology, vol. 2, no. 3, pp. 14–20, 2014. Crossref, https://doi.org/10.5176/2251-3701
[37] IS:12089-1987, “Specification for Granulated Slag for the Manufacture of Portland Slag Cement,” Bureau of Indian Standards, New Delhi, pp. 1–14, 1987.
[38] IS 5512-1983 Reaffirmed 2004, “Specification for Flow Table for use in Tests of Hydraulic Cements and Pozzolanic Materials,” Bureau of Indian Standards, New Delhi, vol. Reaffirmed, no. 2004, 1983.
[39] BIS, “Methods of Test for Aggregates for Conci Is : 2386 ( Part Vi) - 1963,” 1963.
[40] T. R. May and O. F. Indian, “Standard Code of Practice for Code of Practice,” vol. 1965, no. 5, 1966, 1995.
[41] Bureau of Indian Standards, “IS 3495 Parts 1-4 : Methods of Tests of Burnt Clay Building Brick,” IS 3495 1992 - Parts 1 to 4 - Methods Tests Burnt Clay Buildings Bricks, pp. 1–7, 1992.
[42] Indian Standard IS 2185-4, “Concrete Masonry Units, Part 4: Preformed Foam Cellular Concrete Blocks,” 2008.
[43] IS:2185, “Indian Standard Concrete Masonry Units, Part 1: Hollow and Solid Concrete Blocks,” Burea Indian Standard, New Delhi, pp. 17, 2005.
[44] IS: 383-2016, "Specification for Fine Aggregate," Burea Indian Standard, New Delhi.