Performance of Perforated Clay Bricks with Charcoal Waste as an Additive
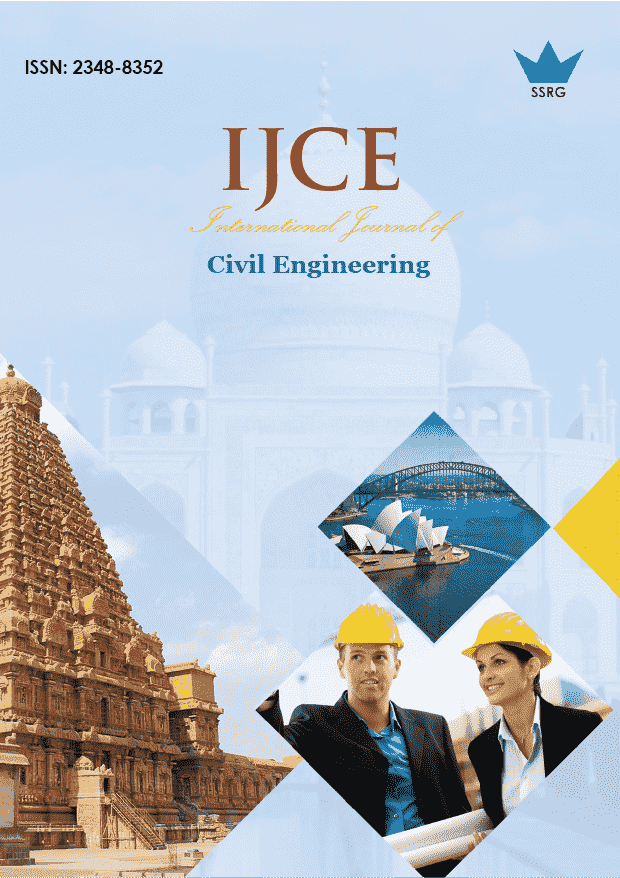
International Journal of Civil Engineering |
© 2023 by SSRG - IJCE Journal |
Volume 10 Issue 1 |
Year of Publication : 2023 |
Authors : Bayisenge Jean Pierre, Isaac Fundi Sanewu, Charles Kabubo |
How to Cite?
Bayisenge Jean Pierre, Isaac Fundi Sanewu, Charles Kabubo, "Performance of Perforated Clay Bricks with Charcoal Waste as an Additive," SSRG International Journal of Civil Engineering, vol. 10, no. 1, pp. 9-17, 2023. Crossref, https://doi.org/10.14445/23488352/IJCE-V10I1P102
Abstract:
In Rwanda, the traditional fired solid bricks embody high fuel consumption and quantity of clay during their molding. Traditional solid bricks are also heavy compared to perforated bricks. This study aimed at investigating the performance of perforated clay bricks made of clay soil (CS) mixed with charcoal waste (CW) as an additive. The physical, chemical and mechanical properties of CS mixed with 0, 10, 30, 40 and 50% of CW were determined. The bricks were extruded manually with the inclusion of a varied number of perforations: 4, 8, 12 and 15 number perforations. The chemical analysis included the determination of organic carbon, exchangeable acidity and chemical components (through XRD) in the soil matrix. The chemical analysis depicted an increase in CaO proportions with an increase in charcoal waste content. There was also an increase in the amounts of exchangeable cations. The research found that with an increase in perforations, weight loss is reduced. However, non-perforated bricks depicted the least abrasion resistance, followed by bricks with 4 perforations. As the CW content increased from 0 to 50%, bricks with 15 and 12 perforations displayed the highest abrasion resistance. The research concludes that an increase in charcoal waste led to an increase in the linear shrinkage of clay soil bricks due to increased calcium cations and reduced magnesium cations in the soil. An optimum of 30% of charcoal waste was identified for the linear shrinkage of clay soil bricks. Bricks having 12 perforations and below with 30% charcoal waste additive can be categorized as category I (load-bearing) bricks.
Keywords:
Brick durability, Charcoal waste, Fired perforated bricks, X-Ray Diffraction.
References:
[1] K. Fabien “Charcoal Value Chain and Improved Cookstove Sector Analyses” Courtney Blodgett, p. 48, 2010
[2] A.A. Kadir, H.H. Jamil, and A.S. Abdul Rahim, “Leachability of Fired Clay Bricks Incorporating with Sludge Waste from Mosaic Industry,” Materials science forum, vol. 803, pp. 233-238, 2014. Crossref, https://doi.org/10.4028/www.scientific.net/MSF.803.233
[3] Abbas Mohajerani, and Aeslina Abdul Kadir, “Effect of Heating Rate on Gas Emission and Properties of Fired Clay Bricks and Fired Clay Bricks Incorporated With Cigarette Butts,” Applied Clay Science, vol. 104, pp. 269-276, 2015. Crossref, https://doi.org/10.1016/j.clay.2014.12.005
[4] Kadir Aeslina Abdul Kadir, Nur Azian Mohd Zahari, and Noor Azizi Mardi, “Utilization of Palm Oil Waste into Fired Clay Brick,” Advances in Environmental Biology, vol. 7, no.12, pp. 3826-3834, 2013.
[5] A.S.A. Rahim, H.H. Jamil, and A.A. Kadir, “Leachability of Fired Clay Brick Incorporating with Sludge Waste from Mosaic Industry,” Material Science Forum, vol. 803, pp. 233-238, 2015.
[6] Kae Long Lin, “Feasibility Study of Using Brick Made from Municipal Solid Waste Incinerator Fly Ash Slag,” Journal of Hazardous Material, vol. 137, no. 3, pp. 1810-1816, 2006. Crossref, https://doi.org/10.1016/j.jhazmat.2006.05.027
[7] Banhidi Viktor, “Enhancement of Insulating Properties of Brick Clay by Renewable Agricultural Wastes,” Processing and Applications of Ceramics, vol. 2, no.2, pp. 75-79, 2008. Crossref, http://dx.doi.org/10.2298/PAC0802075B
[8] P Chindaprasirt et al., “Eco-Efficient Masonry Bricks and Blocks: Design, Properties and Durability,” Elsevier, 2015
[9] Sanu Babu Dangol, S. Adhikari and R.M. Byanju, “Use of Charcoal as Internal Fuel in Vertical Shaft Brick Kiln”, Remtech Symposium Compendium, vol. 3, pp. 22-25, 2013.
[10] BS EN 771-1, Specification for Masonry Units – Clay Masonry Units. BSI, 2003.
[11] BS 3921, Specification for clay bricks. BSI.
[12] E.O. Mclean, “Aluminium in Methods of Soil Analysis,” America Science Agronomy, Madison, Wisconsin, pp. 978-998, 1965
[13] BS 1377-3, Methods of Testing Soils for Civil Engineering Purposes, Chemical and Electro-Chemical Tests, British Standards Institution, 2 Park Street, London, 1990.
[14] BS 1377-2, Methods of Testing Soils for Civil Engineering Purposes, Classification Tests, British Standards Institution, 2 Park Street, London, 1990.
[15] Prashant Modi, and Aarif Jamal, “Geochemical Characterisation of Coal with Special Reference to Thermal Industries of Dhanpuri Open Cast Project, Sohagpur Coalfield, Madhya Pradesh, India,” International Journal of Engineering Trends and Technology, vol. 68, no. 4, pp. 36-42, 2020. Crossref, https://doi.org/10.14445/22315381/IJETT-V68I4P207S
[16] Rwanda standard, RS 359, 2009.
[17] KS EAS 54, Burnt Building Bricks – Specification, 1999.
[18] AASHTO - T 96-02, Standard Method of Test for Resistance to Degradation of Small Size Coarse Aggregate by Abrasion and Impact in the Los Angeles Machine, Washington D.C. USA, 2010.
[19] BS EN 7721-1, Methods of Test for Masonry Units, Determination of Compressive Strength, British standards, 2011.
[20] Uzoma Darlington Chima, Gabriel A. Adedeji, and Kingsley O. Uloho, “Preliminary Assessment of the Impact of Charcoal Production on Physico-Chemical Properties of Soil in Rivers State, Nigeria,” Ethiopian Journal of Environmental Studies and Management, vol. 6, no. 3, pp. 286 – 293, 2013. Crossref, http://dx.doi.org/10.4314/ejesm.v6i3.9
[21] Chellasamy Manoharan et al, “Characteristics of Some Clay Materials from Tamilnadu, India, and Their Possible Ceramic Uses,” Ceramica, vol. 58, no. 347, pp. 412-418, 2012. Crossref, http://dx.doi.org/10.1590/S0366-69132012000300021
[22] Kent J. Schwieger, “The Influence of Cation Exchange and Electrolyte Concentrations Upon the Atterberg Limits,” Masters Thesis. 5721, 1965.
[23] Oladunni Oyelola Alabi, Miracle Adegun, and Temitope Olatunji, “Chemical Characterization of Ijapo Clay and its Additives Towards Production of Refractory Bricks,” Indian Journal of Engineering, vol. 17, no. 48, pp. 342 – 350, 2020.
[24] Brick Industry Association (BIA, Technical Notes 9-Manufacturing, Classification, and Selection of Bricks Manufacturing: Part 1, vol. 14, 2004.
[25] Anuwat Srisuwan et al., “Preparation and Properties of Fired Clay Bricks with Added Wood Ash,” Journal of Metals, Materials and Minerals, vol. 30, no.4, pp. 84- 89, 2020. Crossref, http://dx.doi.org/10.14456/jmmm.2020.
[26] Kenya standard DKS 2801-1, Specification for Clay Masonry Units. Kenya Bureau of Standards
[27] BS 1377-1, Methods of Testing Soils for Civil Engineering Purposes, General Requirements and Sample Preparation, British Standards Institution, 2 Park Street, London, 1990.