Valuation of Malleable Deformation by Crushing Method using X-Ray Diffraction Peak with down feed
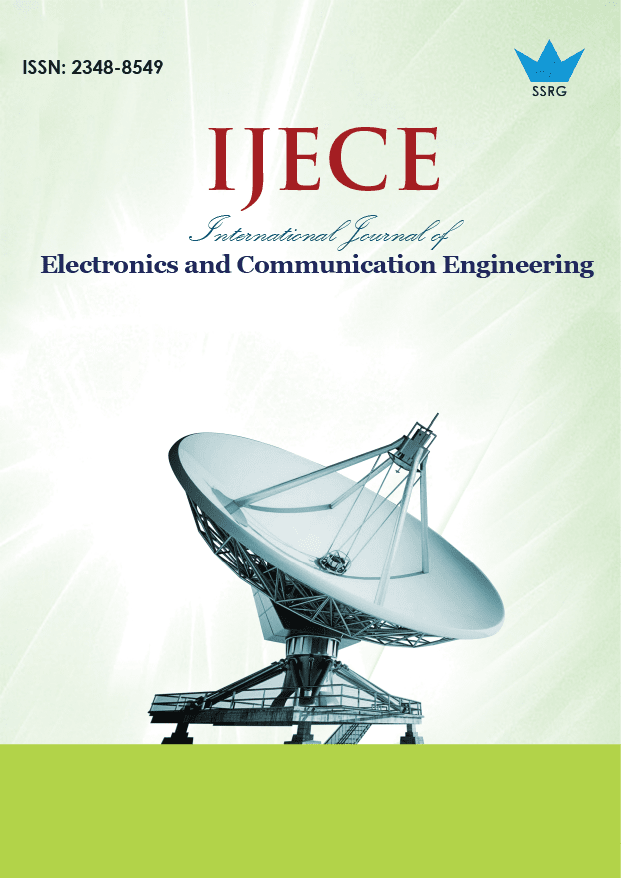
International Journal of Electronics and Communication Engineering |
© 2017 by SSRG - IJECE Journal |
Volume 4 Issue 2 |
Year of Publication : 2017 |
Authors : G.Velmurugan and K.Ragulkumar |
How to Cite?
G.Velmurugan and K.Ragulkumar, "Valuation of Malleable Deformation by Crushing Method using X-Ray Diffraction Peak with down feed," SSRG International Journal of Electronics and Communication Engineering, vol. 4, no. 2, pp. 16-19, 2017. Crossref, https://doi.org/10.14445/23488549/IJECE-V4I2P105
Abstract:
X-ray powder diffraction (XRD) is a fast analytical method mainly used for phase identification of a crystal-like substantial and can deliver information on elemental cell sizes. The analyzed structure is finely powdered, standardized, and typical bulk composition is resolute.X-ray diffraction (XRD) depends on the twin wave/element landscape of X-rays to gain information about the assembly of crystal-like materials. A main use of the method is the identification and description of mixtures based on their diffraction pattern.X-ray diffraction (XRD) imageoutlines of intermediate carbon steel pulverizedmodels were analysed to measure the relentlessconvinced plastic distortion. Enlargement of XRD image profiles with advanceddown feeddesignated the conceivable malleabledistortion. XRD scan outlines were studied to quantity full width at half maximum of profiles for valuation of malleable deformation at several level of depressed feed. FWHM examinationexposed that FWHM upsurges with downfeed due to malleabledistortion. Ounce size of distorted layers was also assessed using Schererequivalence to confirm the results foundover FWHM examination. Valuation of grinding encouraged plastic distortion using XRD profiles established the applicability of this novelmethod forqualitative amount of superficial integrity features like micro stiffness and exterior roughness. Micro stiffness measurement and exterior roughness examination of ground models have been agree toapprove the results found by FWHM study.
Keywords:
[1] M. G. Moore and W. P.Evans, Mathematical Corrections in Removal Layers in X- Ray Diffraction Residual Stress Analysis, SAE Trans., 66 (1958) 340–345.
[2] M. J. Balart, A. Bouzina, L. Edwards and M. E. Fitzpatrick, The onset of tensile residual stress in grinding of hardened steels, Mater. Sci. and Eng., 367 (2004) 132– 42.
[3] M. Lindgren and T. Lepisto, Effect of prestraining on
[4] Barkhausen noise vs. stress relation, NDT&E Int., 34 (2001) 337–344.
[5] W. B. Rowe, S. C. E. Black and B. Mills, Temperature Control in CBN Grinding, Int. J. of Adv. Manuf. Tech, 12 (1996) 387- 392
[6] I. C. Noyan and J. B. Cohen, Residual Stress- Measurement byDiffraction and Interpretation, (1987) Springer-Verlag, NewYork
[7] I. F. Pariente and M. Guagliano, ‘About the role of residualstresses and surface work hardening on fatigue ΔKth of anitrided and shot peened low-alloy steel’, Surf. And Coat. Tech.,202 (2008) 3072–3080.
[8]S. Malkin, Grinding of metals: Theory and application, ASM J.of App. Met. Work, 3 (1984) 95-109.
[9]X. Chen and W. B. Rowe, Analysis and simulation of the grinding process. part 2: Mechanics of grinding, Int. J. of Mach. Tool. and Manuf., 36 (1996) 883-896.
[10]R. Elilarassi and G.Chandrasekaran, Effect of annealing on structural and optical properties of zinc oxide films, Mater.Chem. andPhy., 121 (2010)378–384
[11]R. A. Poggie and J. J. Wert ‘The influence of surface finish and strain hardening on near-surface residual stress and the friction and wear behaviour of A2, D2 and CPM-10V tool steels, Wear, 149 (1991) 209–220.
References:
[1] M. G. Moore and W. P.Evans, Mathematical Corrections in Removal Layers in X- Ray Diffraction Residual Stress Analysis, SAE Trans., 66 (1958) 340–345.
[2] M. J. Balart, A. Bouzina, L. Edwards and M. E. Fitzpatrick, The onset of tensile residual stress in grinding of hardened steels, Mater. Sci. and Eng., 367 (2004) 132– 42.
[3] M. Lindgren and T. Lepisto, Effect of prestraining on
[4] Barkhausen noise vs. stress relation, NDT&E Int., 34 (2001) 337–344.
[5] W. B. Rowe, S. C. E. Black and B. Mills, Temperature Control in CBN Grinding, Int. J. of Adv. Manuf. Tech, 12 (1996) 387- 392
[6] I. C. Noyan and J. B. Cohen, Residual Stress- Measurement byDiffraction and Interpretation, (1987) Springer-Verlag, NewYork
[7] I. F. Pariente and M. Guagliano, ‘About the role of residualstresses and surface work hardening on fatigue ΔKth of anitrided and shot peened low-alloy steel’, Surf. And Coat. Tech.,202 (2008) 3072–3080.
[8]S. Malkin, Grinding of metals: Theory and application, ASM J.of App. Met. Work, 3 (1984) 95-109.
[9]X. Chen and W. B. Rowe, Analysis and simulation of the grinding process. part 2: Mechanics of grinding, Int. J. of Mach. Tool. and Manuf., 36 (1996) 883-896.
[10]R. Elilarassi and G.Chandrasekaran, Effect of annealing on structural and optical properties of zinc oxide films, Mater.Chem. andPhy., 121 (2010)378–384
[11]R. A. Poggie and J. J. Wert ‘The influence of surface finish and strain hardening on near-surface residual stress and the friction and wear behaviour of A2, D2 and CPM-10V tool steels, Wear, 149 (1991) 209–220.