Farmer Robot for Harvesting and Maintaining Plants
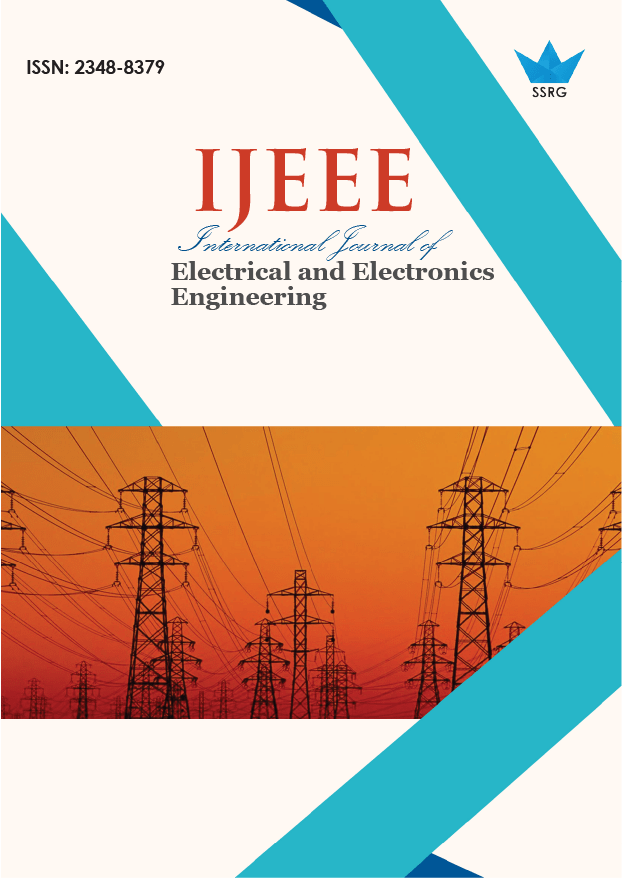
International Journal of Electrical and Electronics Engineering |
© 2020 by SSRG - IJEEE Journal |
Volume 7 Issue 1 |
Year of Publication : 2020 |
Authors : Mohammed Farhan Jawad , T.A.M. Ragib Shahriar, Fawjia Yeshmin Shakhi, Noushad Hossain, Md. Shariful Islam, Md. Mohsinur Rahman Adnan, Md Asaduz Zaman Mamun |
How to Cite?
Mohammed Farhan Jawad , T.A.M. Ragib Shahriar, Fawjia Yeshmin Shakhi, Noushad Hossain, Md. Shariful Islam, Md. Mohsinur Rahman Adnan, Md Asaduz Zaman Mamun, "Farmer Robot for Harvesting and Maintaining Plants," SSRG International Journal of Electrical and Electronics Engineering, vol. 7, no. 1, pp. 7-11, 2020. Crossref, https://doi.org/10.14445/23488379/IJEEE-V7I1P102
Abstract:
Agriculture falls vulnerable to the impacts of climate change, which implies that any change in the climate can significantly affect the quality of the crops produced. Moreover, issues like labour problems, labour costs, productivity problems, etc. are stumbling blocks of traditional cultivation systems. Also, farmers need to produce more, at a higher quality, and in a sustainable manner to feed the increasing population. All these complications necessitate an automated system in this sector. In this project, we have built an autonomous robot that can detect ripe fruits or vegetables using colour detection mechanism and successfully harvest those with a robotic hand. The system can be sub-categorized into three units– fruit picker, watering pump and sensing unit. The function of fruit picker is the identification of ripe fruits or vegetables by their colour, cut them off of the tree and then store them into suitable storage. The watering unit will pump water and necessary elements from the source tank and spread it in the field. The sensing unit is for the indication of the instant state of surroundings to help a farmer to choose the right steps to be taken. Although there are some initial costs to implement this system, this robot can precisely detect the right fruit (e.g. tomato or pepper) to be harvested and hence it can be used to pace up harvesting speed and save the labour and other associated costs. In this study, we have described the detailed processes followed to build this robot; hardware used; software implemented and assembly of the whole system as a functional unit.
Keywords:
Robotic arm, Convolution Neural Network (CNN), ATMega 2560 processor
References:
[1] A. Tombesi, “Physiological and mechanical advances in olive harvesting,” in International Symposium on Olive Growing 286, 1989, pp. 399– 412.
[2] S. Grimsen, R. N. Jaques, V. Erenst, and J. G. Balchen, “Aspects of automation in a lobster farming plant,” IFAC Proceedings Volumes, vol. 20, no. 7, pp. 221–224, 1987.
[3] T. M. Banhazi and J. L. Black, “Precision livestock farming: a suite of electronic systems to ensure the application of best practice management on livestock farms,” Australian Journal of Multi-disciplinary Engineering, vol. 7, no. 1, pp. 1–14, 2009.
[4] C. Rosenzweig, D. Hillel et al., Climate change and the global harvest: potential impacts of the greenhouse effect on agriculture. Oxford University Press, 1998.
[5] Design and Simulation of a Robot-Farmer for Gripping and Cutting Crops, Khulna, Bangladesh, 2014.
[6] M. Sujaritha, M. Lakshminarasimhan, C. J. Fernandez, and M. Chandran, “Greenbot: a solar autonomous robot to uproot weeds in a grape field,” International Journal of Computer Science and Engineering, vol. 4, no. 2, pp. 1351–1358, 2016.
[7] an autonomous robot for automated scoring of vineyards, Zurich, Switzerland, 2014.
[8] P. D. P. Md. Abu Bakar Siddik, Mou Deb and M. K. Dhar, “Robotics and automation in agriculture,” International Journal of Engineering Trends and Technology, vol. 38, no. 8, pp. 426–432, 2016.
[9] K. Dasgupta, “Analysis of a hydrostatic transmission system using low speed high torque motor,” Mechanism and machine theory, vol. 35, no. 10, pp. 1481–1499, 2000.
[10] B. Chapnik, G. R. Heppler, J. D. Aplevich et al., “Modeling impact on a one-link flexible robotic arm,” IEEE Transactions on Robotics and Automation, vol. 7, no. 4, pp. 479–488, 1991.
[11] R. Ramanath, W. E. Snyder, Y. Yoo, and M. S. Drew, “Color image processing pipeline,” IEEE Signal Processing Magazine, vol. 22, no. 1, pp. 34–43, 2005.
[12] M. Hosek and H. Elmali, “Trajectory planning and motion control strategies for a planar three-degree-of-freedom robotic arm,” Nov. 4 2003, uS Patent 6,643,563.