Double Stator Induction Machine for Variable Speed And Variable Torque Applications
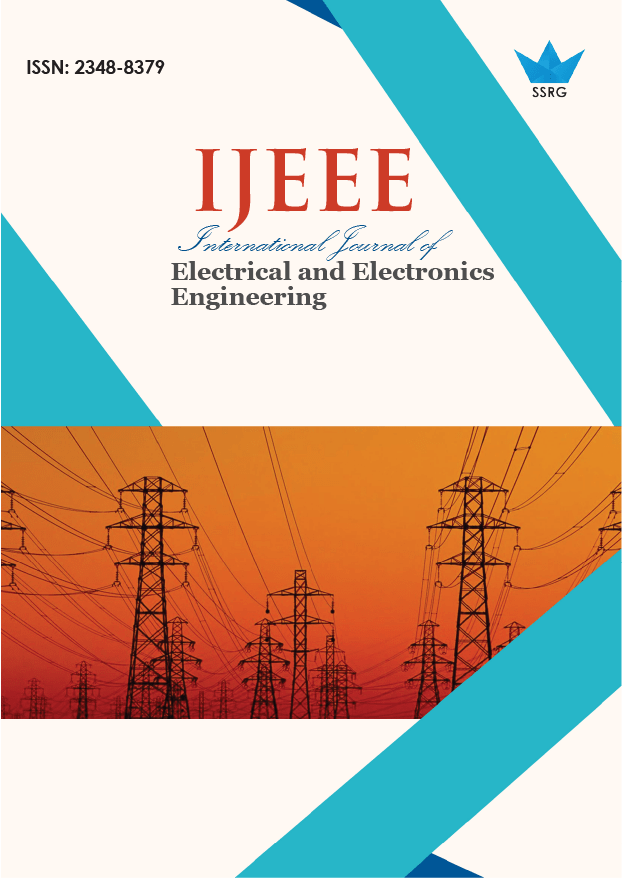
International Journal of Electrical and Electronics Engineering |
© 2021 by SSRG - IJEEE Journal |
Volume 8 Issue 12 |
Year of Publication : 2021 |
Authors : Anagha R. Soman, R. M. Holmukhe |
How to Cite?
Anagha R. Soman, R. M. Holmukhe, "Double Stator Induction Machine for Variable Speed And Variable Torque Applications," SSRG International Journal of Electrical and Electronics Engineering, vol. 8, no. 12, pp. 1-4, 2021. Crossref, https://doi.org/10.14445/23488379/IJEEE-V8I12P101
Abstract:
Conventional Induction machine has only one drawback of not having a smooth speed control if compared with DC Machines. But because of recent developments in technology such as semiconductors, drives, this drawback can be ruled out. A conventional Induction machine has a single speed-torque characteristic. The application of a respective machine depends on the load characteristics. Many applications in the industry need variable torque and variable speed. A double stator induction machine is so designed that there are two different stator windings housed in the same stator core, which then gives the best of both machines in a single machine. Using a simple controller, a wide range of speed and torque is available using a single machine. Such machines will find applications in the Textile, EV, Food industries where variable torques and speeds are required.
The windings housed in the stator core can be for the same/ different.number of poles [1]. As per the rotor construction, the conventional induction machines are classified as squirrel cage and Split wound. Both these constructions have their own merits and demerits. Typically, Squirrel cage induction motors find applications in vivid areas due to simple and rugged construction and negligible maintenance. This type of Induction machine has versatile applications in various fields, covering almost 90% share in the electrical machines market. Speed -torque characteristics of such machines are almost constant. The variation in torque can be achieved by changing resistance in the rotor circuit. However, in squirrel cage induction machines, this method is not feasible. The only way to vary torque or speed is the stator side control. Stator side control methods are change of poles, change of supply frequency, change of supply voltage, change of the ratio of voltage/frequency, and adding an additional resistance/impedance in stator circuit. The common methods to vary the speed as discussed above are not flexible enough to achieve the required Torque-Speed characteristics of the motor suitable to the load requirement pertaining to a particular application. In addition to this, these methods also have a problem that the electrical
frequency changes with the mechanical speed (n = (2f/p)(1−s)). Hence, smooth control over Torque-speed is not feasible. Voltage Source Inverter (VSI) fed Induction machine does not face this issue. But this induces harmonics in the system and makes the machine less reliable and also costlier. Variable Frequency Drives (VFD) require filters to limit the rate of change of voltage (dV/dt) up to 6 kV/ μS, which otherwise may cause insulation failure. As per the above discussion, it is concluded that a Double Stator Induction Machine (DSIM) can provide a better option for variable speed applications.
Keywords:
Torque-Speed characteristics, DSIM, VSI
References:
[1] A. R. Munoz and T. A. Lipo, Dual Stator Winding Induction Machine Drive, IEEE Transactions on Industry Applications. 36(5) (2000) 1369-1379.
[2] S.Basak and C. Chakraborty, Dual Stator Winding Induction Machine, Problems, Progress, and Future Scope, IEEE Transactions on Industrial Electronics. 62(7) (2015) 4641-4652.
[3] A.R.Soman, Design And Development of Dual Stator Induction Machine, Ph.D. Dissertation, Dept. Elect. Eng., Bharati Vidyapeeth Deemed to be Univ. College of Engineering, Pune. (2020).
[4] A.R.Munoz-Garcia, Analysis and Control of a Dual Stator Winding Squirrel Cage Induction Machine, Ph.D. Dissertation, Dep. Elect. Comp. Eng., Univ. Wisconsin, Madison. (1999).
[5] Anagha Soman, Sachin Madaan, Shubh Gupta, Abhishek Singh, Ankit Tiwari , Performance Analysis of Dual Stator Induction Motor, International Research Journal of Engineering and Technology. 5(5) (2018) 1-6
[6] A.R.Soman, Dr.D.G.Bharadwaj, Dr.R.M.Holmukhe, Variation in Torque of DSWIM by Changing Voltage Keeping the Speed Constant, Asian Journal of Convergence in Technology. 5(1) 1-4
[7] A.R.Soman, Dr.D.G.Bharadwaj, Dr.R.M.Holmukhe, Multispeed Operation and Testing of the Dual Stator Winding Induction Machine, International Journal of Scientific & Technology Research. (2020).
[8] Paul C. Krause, Oleg Wasynczuk and Scott D. Sudhoff, Analysis of Electric Machinery and Drive Systems, International Research Journal of Engineering and Technology (IRJET), IEEE Press Series on Power Engineering, John Wiley and Sons Inc. Publication.
[9] Anagha Soman, Nupoor Lokhande, Performance Analysis of 3 Phase Dual Stator Induction Motor Using ANSYS Maxwell, International Journal of Pure and Applied Mathematics. 118(16) (2018) 269-281.
[10] Anagha Soman, Dr.D.G.Bharadwaj, Dr.R.M.Holmuk.,He Analyzing and Testing of the Performance of DSWIM by ANSYS Maxwell, International Journal of Scientific & Technology Research. (2020).
[11] A.R.Soman, Dr.D.G.Bharadwaj, Dr.R.M.Holmukhe, Analyzing Performance of 3-PH Dual Stator Induction Motor, Conference Proceedings of 2nd International Conference on Electrical Electronics and Computer Science, Siliguri. (2018).
[12] Luigi Alberti, and Nichola Bianchi, Impact of Winding Arrangement in Dual 3-Phase Induction Motor for Fault-Tolerant Applications, XIX International Conference on Electrical Machines-ICEM. (2010) 1-6.