Intelligent Fault Diagnosis of Rotating Machinery Using Deep Learning Algorithms: A Comparative Analysis of MLP, CNN, RNN, and LSTM
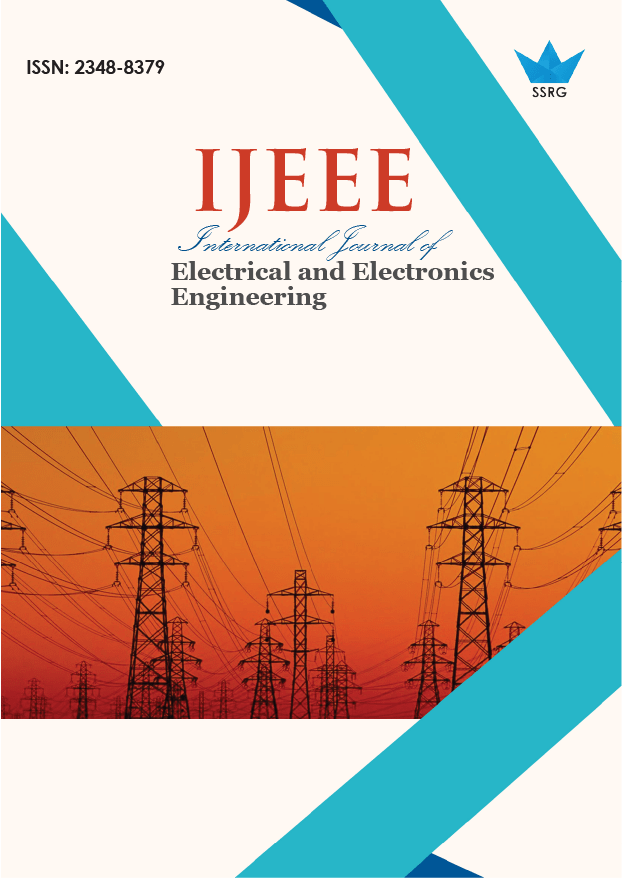
International Journal of Electrical and Electronics Engineering |
© 2024 by SSRG - IJEEE Journal |
Volume 11 Issue 9 |
Year of Publication : 2024 |
Authors : Vijayalakshmi K, Amuthakkannan Rajakannu, Mohsina Kamarudden, Ramachandran KP Sri Rajkavin A V |
How to Cite?
Vijayalakshmi K, Amuthakkannan Rajakannu, Mohsina Kamarudden, Ramachandran KP Sri Rajkavin A V, "Intelligent Fault Diagnosis of Rotating Machinery Using Deep Learning Algorithms: A Comparative Analysis of MLP, CNN, RNN, and LSTM," SSRG International Journal of Electrical and Electronics Engineering, vol. 11, no. 9, pp. 294-315, 2024. Crossref, https://doi.org/10.14445/23488379/IJEEE-V11I9P127
Abstract:
Health management in industrial systems is crucial for maintenance management, and it plays an important role in productivity, fault diagnosis, safety, efficiency, and economy in manufacturing industries. Early detection of faults in machinery may increase the effectiveness of maintenance actions and will avoid unwanted consequences in process operations and maintenance. Existing fault diagnosis methods have limitations such as insufficient accuracy, slow detection rate, and handling large and complex data sets. In this digital age, Industry 4.0 techniques have been applied across all fields, including the condition monitoring of machines. This research addresses the gaps in traditional fault diagnosis by using deep learning, a modern AI technique effective for diagnosing faults in various machines. In this research work, vibration signals are collected using the National Instruments- Data Acquisition (NI-DAQ) system, accelerometer, and LabVIEW software. These signals are processed using a series of steps, including sampling strategy, shuffling, standardization, and reshaping data augmentation. Deep learning algorithms Multilayer Perceptron (MLP), Convolutional Neural Network (CNN), and Recurrent Neural Network (RNN) with Long Short-Term Memory (LSTM) are tested for fault diagnosis using vibration datasets collected from Spectra Quest Machinery Fault Simulator (SQMFS). The result shows that MLP accuracy in the fault prediction is 0.9, CNN reached 0.95, and RNN and LSTM with 0.57 and 0.45, respectively. The high performance of CNN is due to its ability to effectively capture spatial patterns in vibration data, which is crucial for fault diagnosis in rotating machinery, followed by MLP due to its faster convergence during training. When the data is scaled, MLP performs better than CNN, demonstrating its adaptability to increased data complexity and volume. RNN and LSTM resulted in lower accuracy due to the need for larger datasets and temporal patterns in the vibration data, which they are designed to handle. This study shows that CNN has given better results than other deep learning algorithms, such as MLP, RNN, and LSTM, in fault diagnosis of rotating machinery. Future research could explore applying these techniques to different types of machinery and fault conditions.
Keywords:
Condition monitoring, Convolutional Neural Network (CNN), Long Short-Term Memory (LSTM), Machine fault simulator, Multilayer Perceptron (MLP), Recurrent Neural Network (RNN).
References:
[1] H.S. Kumar, and Gururaj Upadhyaya, “Fault Diagnosis of Rolling Element Bearing Using Continuous Wavelet Transform and K- Nearest Neighbour,” Materials Today: Proceedings, vol. 92, pp. 56-60, 2023.
[CrossRef] [Google Scholar] [Publisher Link]
[2] Anirbid Sircar et al., “Application of Machine Learning and Artificial Intelligence in Oil and Gas Industry,” Petroleum Research, vol. 6, no. 4, pp. 379-391, 2021.
[CrossRef] [Google Scholar] [Publisher Link]
[3] Karali Patra, “Acoustic Emission Based Tool Condition Monitoring System in Drilling,” Proceedings of the World Congress on Engineering, London, pp. 1-5, 2011.
[Google Scholar] [Publisher Link]
[4] Shuping Cao et al., “Research on Fault Diagnosis Technology of Centrifugal Pump Blade Crack Based on PCA and GMM,” Measurement, vol. 173, 2021.
[CrossRef] [Google Scholar] [Publisher Link]
[5] Onur Surucu, Stephen Andrew Gadsden, and John Yawney, “Condition Monitoring Using Machine Learning: A Review of Theory, Applications, and Recent Advances,” Expert Systems with Applications, vol. 221, 2023.
[CrossRef] [Google Scholar] [Publisher Link]
[6] G. Serin et al., “Review of Tool Condition Monitoring in Machining and Opportunities for Deep Learning,” The International Journal of Advanced Manufacturing Technology, vol. 109, no. 3-4, pp. 953-974, 2020.
[CrossRef] [Google Scholar] [Publisher Link]
[7] Josef Koutsoupakis, Panagiotis Seventekidis, and Dimitrios Giagopoulos, “Machine Learning Based Condition Monitoring for Gear Transmission Systems Using Data Generated by Optimal Multibody Dynamics Models,” Mechanical Systems and Signal Processing, vol. 190, 2023.
[CrossRef] [Google Scholar] [Publisher Link]
[8] Long Zhang et al., “An Imbalanced Fault Diagnosis Method Based on TFFO and CNN for Rotating Machinery,” Sensors, vol. 22, no. 22, 2022.
[CrossRef] [Google Scholar] [Publisher Link]
[9] Erkki Jantunen, “A Summary of Methods Applied to Tool Condition Monitoring in Drilling,” International Journal of Machine Tools & Manufacture, vol. 42, no. 9, pp. 997-1010, 2002.
[CrossRef] [Google Scholar] [Publisher Link]
[10] Pushkar Dehspande et al., “Acoustic Emission and Machine Learning Based Classification of Wear Generated Using A Pin-on-Disc Tribometer Equipped with A Digital Holographic Microscope,” Wear, vol. 476, 2021.
[CrossRef] [Google Scholar] [Publisher Link]
[11] Rui Zhao et al., “Deep Learning and Its Applications to Machine Health Monitoring,” Mechanical Systems and Signal Processing, vol. 115, pp. 213-237, 2019.
[CrossRef] [Google Scholar] [Publisher Link]
[12] Lang Dai et al., “An Improved Deep Learning Model for Online Tool Condition Monitoring Using Output Power Signals,” Shock and Vibration, vol. 2020, 2020.
[CrossRef] [Google Scholar] [Publisher Link]
[13] Qun Wang et al., “Overview of Tool Wear Monitoring Methods Based on Convolutional Neural Network,” Applied Sciences, vol. 11, no. 24, 2021.
[CrossRef] [Google Scholar] [Publisher Link]
[14] Mariela Cerrada et al., “A Review on Data-Driven Fault Severity Assessment in Rolling Bearings,” Mechanical Systems and Signal Processing, vol. 99, pp. 169-196, 2018.
[CrossRef] [Google Scholar] [Publisher Link]
[15] Olivier Janssens et al., “Convolutional Neural Network Based Fault Detection for Rotating Machinery,” Journal of Sound and Vibration, vol. 377, pp. 331-345, 2016.
[CrossRef] [Google Scholar] [Publisher Link]
[16] Yong Yao et al., “Learning Attention Representation with a Multi-Scale CNN for Gear Fault Diagnosis under Different Working Conditions,” Sensors, vol. 20, no. 4, 2020.
[CrossRef] [Google Scholar] [Publisher Link]
[17] Wei Zhang et al., “A Deep Convolutional Neural Network with New Training Methods for Bearing Fault Diagnosis under Noisy Environment and Different Working Load,” Mechanical Systems and Signal Processing, vol. 100, pp. 439-453, 2018. [CrossRef] [Google Scholar] [Publisher Link]
[18] Manar Abdelmaksoud et al., “Convolutional-Neural-Network-Based Multi-Signals Fault Diagnosis of Induction Motor Using Single and Multi-Channels Datasets,” Alexandria Engineering Journal, vol. 73, pp. 231-248, 2023.
[CrossRef] [Google Scholar] [Publisher Link]
[19] Tshilidzi Marwala, “Multi-Layer Perceptron for Condition Monitoring in a Mechanical System,” Condition Monitoring Using Computational Intelligence Methods, pp. 53-69, 2011.
[CrossRef] [Google Scholar] [Publisher Link]
[20] Dino Zanic, and Alan Zupan, “Monitoring Transformer Condition with MLP Machine Learning Model,” The Journal of Energy, vol. 72, no. 2, pp. 3-7, 2023.
[CrossRef] [Google Scholar] [Publisher Link]
[21] Van-Quang Nguyen et al., “A Deep Learning Approach Based on MLP-Mixer Models for Bearing Fault Diagnosis,” 2023 International Conference on System Science and Engineering (ICSSE), Ho Chi Minh, Vietnam, pp. 16-21, 2023.
[CrossRef] [Google Scholar] [Publisher Link]
[22] Khoualdia Tarek et al., “Optimized Multi-Layer Perceptron Artificial Neural Network-Based Fault Diagnosis of Induction Motor Using Vibration Signals,” Diagnostyka, vol. 22, no. 1, pp. 65-74, 2021.
[CrossRef] [Google Scholar] [Publisher Link]
[23] Dhiraj Neupane et al., “CNN-Based Fault Detection for Smart Manufacturing,” Applied Sciences, vol. 11, no. 24, 2021.
[CrossRef] [Google Scholar] [Publisher Link]
[24] Andreas Lundgren, and Daniel Jung, “Data-Driven Fault Diagnosis Analysis and Open-Setclassification of Time-Series Data,” Control Engineering Practice, vol. 121, 2022.
[CrossRef] [Google Scholar] [Publisher Link]
[25] Guoqiang Li et al., “Deep Reinforcement Learning-Based Online Domain Adaptation Method for Fault Diagnosis of Rotating Machinery,” IEEE/ASME Transactions on Mechatronics, vol. 27, no. 5, pp. 2796-2805, 2022.
[CrossRef] [Google Scholar] [Publisher Link]
[26] Yongxiang Lei et al., “Processes Soft Modeling Based on Stacked Autoencoders and Wavelet Extreme Learning Machine for Aluminumplant-Wide Application,” Control Engineering Practice, vol. 108, 2021.
[CrossRef] [Google Scholar] [Publisher Link]
[27] Jinghui Tian et al., “A Multi-Source Information Transfer Learning Method with Subdomain Adaptation for Cross-Domain Fault Diagnosis,” Knowledge-Based Systems, vol. 243, 2022.
[CrossRef] [Google Scholar] [Publisher Link]
[28] Daoguang Yang, Hamid Reza Karimi, and Len Gelman, “A Fuzzy Fusion Rotating Machinery Fault Diagnosis Framework Based on the Enhancement Deep Convolutional Neural Networks,” Sensors, vol. 22, no. 2, 2022.
[CrossRef] [Google Scholar] [Publisher Link]
[29] Yongxiang Lei, Hamid Reza Karimi, and Xiaofang Chen, “A Novel Self-Supervised Deep LSTM Network for Industrial Temperature Prediction in Aluminum Processes Application,” Neurocomputing, vol. 502, pp. 177-185, 2022.
[CrossRef] [Google Scholar] [Publisher Link]
[30] Funa Zhou et al., “The Deep Learning Fault Diagnosis Method is Based on Global Optimization GAN for Unbalanced Data,” Knowledge-Based Systems, vol. 187, 2020.
[CrossRef] [Google Scholar] [Publisher Link]
[31] Haobo Wang et al., “Approach to the Quantitative Diagnosis of Rolling Bearings Based on Optimized VMD and Lempel-Ziv Complexity under Varying Conditions,” Sensors, vol. 23, no. 8, 2023.
[CrossRef] [Google Scholar] [Publisher Link]
[32] Liyue Chen et al., “Temperature Prediction of Seasonal Frozen Subgrades Based on CEEMDAN-LSTM Hybrid Model,” Sensors, vol. 22, no. 15, 2022.
[CrossRef] [Google Scholar] [Publisher Link]
[33] Levent Eren, Turker Ince, and Serkan Kiranyaz, “A Generic Intelligent Bearing Fault Diagnosis System Using Compact Adaptive 1DCNN Classifier,” Journal of Signal Processing Systems, vol. 91, pp. 179-189, 2019.
[CrossRef] [Google Scholar] [Publisher Link]
[34] Wei Zhang, Xiang Li, and Qian Ding, “Deep Residual Learning-Based Fault Diagnosis Method for Rotating Machinery,” ISA Transactions, vol. 95, pp. 295-305, 2019.
[CrossRef] [Google Scholar] [Publisher Link]
[35] Diwang Ruan et al., “CNN Parameter Design Based on Fault Signal Analysis and Its Application in Bearing Fault Diagnosis,” Advanced Engineering Informatics, vol. 55, 2023.
[CrossRef] [Google Scholar] [Publisher Link]
[36] Achyuth Kothuru, Sai Prasad Nooka, and Rui Liu, “Application of Deep Visualization in CNN-Based Tool Condition Monitoring for End Milling,” Procedia Manufacturing, vol. 34, pp. 995-1004, 2019.
[CrossRef] [Google Scholar] [Publisher Link]
[37] Feng Jia et al., “Deep Normalized Convolutional Neural Network for Imbalanced Fault Classification of Machinery and Its Understanding via Visualization,” Mechanical Systems and Signal Processing, vol. 110, pp. 349-367, 2018.
[CrossRef] [Google Scholar] [Publisher Link]
[38] Serhat Seker, Emine Ayaz, and Erduinc Turkcan, “Elman's Recurrent Neural Network Applications to Condition Monitoring in Nuclear Power Plant and Rotating Machinery,” Engineering Applications of Artificial Intelligence, vol. 16, no. 7-8, pp. 647-656, 2023.
[CrossRef] [Google Scholar] [Publisher Link]
[39] Chris Halliday et al., “A Recurrent Neural Network Method for Condition Monitoring and Predictive Maintenance of Pressure Vessel Components,” Pressure Vessels & Piping Conference, Las Vegas, Nevada, USA, pp. 1-5, 2022.
[CrossRef] [Google Scholar] [Publisher Link]
[40] Swetha R. Kumar, and Jayaprasanth Devakumar, “Recurrent Neural Network Based Sensor Fault Detection and Isolation for Nonlinear Systems: Application in PWR,” Progress in Nuclear Energy, vol. 163, 2023.
[CrossRef] [Google Scholar] [Publisher Link]
[41] Yahui Zhang et al., “Fault Diagnosis of Rotating Machinery Based on Recurrent Neural Networks,” Measurement, vol. 171, 2021.
[CrossRef] [Google Scholar] [Publisher Link]
[42] Zhuang Ye, and Jianbo Yu, “Health Condition Monitoring of Machines Based on Long Short-Term Memory Convolutional Autoencoder,” Applied Soft Computing, vol. 107, 2021.
[CrossRef] [Google Scholar] [Publisher Link]
[43] Haitao Zhao, Shaoyuan Sun, and Bo Jin, “Sequential Fault Diagnosis Based on LSTM Neural Network,” IEEE Access, vol. 6, pp. 12929-12939, 2018.
[CrossRef] [Google Scholar] [Publisher Link]
[44] Yasir Saleem Afridi et al., “LSTM-Based Condition Monitoring and Fault Prognostics of Rolling Element Bearings Using Raw Vibrational Data,” Machines, vol. 11, no. 5, 2023.
[CrossRef] [Google Scholar] [Publisher Link]
[45] Jiaqi Xie et al., “An End-to-End Model Based on Improved Adaptive Deep Belief Network and Its Application to Bearing Fault Diagnosis,” IEEE Access, vol. 6, pp. 63584-63596, 2018.
[CrossRef] [Google Scholar] [Publisher Link]
[46] Shaohua Qiu et al., “Deep Learning Techniques in Intelligent Fault Diagnosis and Prognosis for Industrial Systems: A Review,” Sensors, vol. 23, no. 3, 2023.
[CrossRef] [Google Scholar] [Publisher Link]
[47] SpectraQuest, Inc., User Operating Manual for Machinery Fault Simulator™, Richmond, 2020. [Online]. Available: https://spectraquest.com/machinery-fault-simulator/details/mfs/
[48] Selina S. Y. Ng, Peter W. Tse, and Kwok L. Tsui, “A One-Versus-All Class Binarization Strategy for Bearing Diagnostics of Concurrent Defects,” Sensors, vol. 14, no. 1, pp. 1295-1321, 2014.
[CrossRef] [Google Scholar] [Publisher Link]
[49] Soha A. Nossier et al., “A Comparative Study of Time and Frequency Domain Approaches to Deep Learning Based Speech Enhancement,” 2020 International Joint Conference on Neural Networks (IJCNN), Glasgow, UK, pp. 1-8, 2020.
[CrossRef] [Google Scholar] [Publisher Link]
[50] Kun Yi et al., “Frequency-Domain MLPs are More Effective Learners in Time Series Forecasting,” 37th Conference on Neural Information Processing Systems, pp. 1-24, 2023.
[Google Scholar] [Publisher Link]
[51] Ankur Mali et al., “Neural JPEG: End-to-End Image Compression Leveraging a Standard JPEG Encoder-Decoder,” 2022 Data Compression Conference (DCC), Snowbird, UT, USA, pp. 471-471, 2022.
[CrossRef] [Google Scholar] [Publisher Link]
[52] Lars Hertel, Huy Phan, and Alfred Mertins, “Comparing Time and Frequency Domain for Audio Event Recognition Using Deep Learning,” 2016 International Joint Conference on Neural Networks (IJCNN), Vancouver, BC, Canada, pp. 3407-3411, 2016.
[CrossRef] [Google Scholar] [Publisher Link]
[53] Hamid Karimi, Fault Diagnosis and Prognosis Techniques for Complex Engineering Systems, Springer, Berlin, 2021.
[Google Scholar] [Publisher Link]
[54] Keiron O'Shea, and Ryan Nash, “An Introduction to Convolutional Neural Networks,” arXiv Preprint, 2015.
[CrossRef] [Google Scholar] [Publisher Link]
[55] Yann LeCun, Yoshua Bengio, and Geoffrey Hinton, “Deep Learning,” Nature, vol. 521, no. 7553, pp. 436-444, 2015.
[CrossRef] [Google Scholar] [Publisher Link]
[56] Chaochun Zhong et al., “Improved MLP Energy Meter Fault Diagnosis Method Based on DBN,” Electronics, vol. 12, no. 4, 2023.
[CrossRef] [Google Scholar] [Publisher Link]
[57] Kurt Hornik, Maxwell Stinchcombe, and Halbert White, “Multilayer Feedforward Networks are Universal Approximators,” Neural Networks, vol. 2, no. 5, pp. 359-366, 1989.
[CrossRef] [Google Scholar] [Publisher Link]
[58] Alex Krizhevsky, Ilya Sutskever, and Geoffrey E. Hinton, “ImageNet Classification with Deep Convolutional Neural Networks,” Advances in Neural Information Processing Systems, vol. 25, pp. 1097-1105, 2012.
[Google Scholar] [Publisher Link]
[59] Kaiming He et al., “Deep Residual Learning for Image Recognition,” 2016 IEEE Conference on Computer Vision and Pattern Recognition (CVPR), Las Vegas, NV, pp. 770-778, 2016.
[CrossRef] [Google Scholar] [Publisher Link]
[60] Ian Goodfellow, Yoshua Bengio, and Aaron Courville, Deep Learning, Cambridge, MA: MIT Press, 2016.
[Google Scholar] [Publisher Link]
[61] Kaiming He et al., “Delving Deep into Rectifiers: Surpassing Human-Level Performance on ImageNet Classification,” 2015 IEEE International Conference on Computer Vision (ICCV), Santiago, Chile, pp. 1026-1034, 2015.
[CrossRef] [Google Scholar] [Publisher Link]
[62] John McGonagle, Christopher Williams, and Jimin Khim, Recurrent Neural Network. [Online]. Available: https://brilliant.org/wiki/recurrentneural-network/
[63] Sepp Hochreiter, and Jurgen Schmidhuber, “Long Short-Term Memory,” Neural Computation, vol. 9, no. 8, pp. 1735-1780, 1997.
[CrossRef] [Google Scholar] [Publisher Link]
[64] Divyanshu Thakur, LSTM and its Equations, Median, 2018. [Online]. Available: https://medium.com/@divyanshu132/lstm-and-its-equations-5ee9246d04af
[65] Alex Graves, Supervised Sequence Labelling with Recurrent Neural Networks, Springer Science & Business Media, 2012.
[CrossRef] [Google Scholar] [Publisher Link]