Condition Monitoring of CNC Drill Bit for the Manufacturing Sector Using Wavelet Analysis and Artificial Neural Network Based on Feedforward Multilayer Perceptron (MLP)
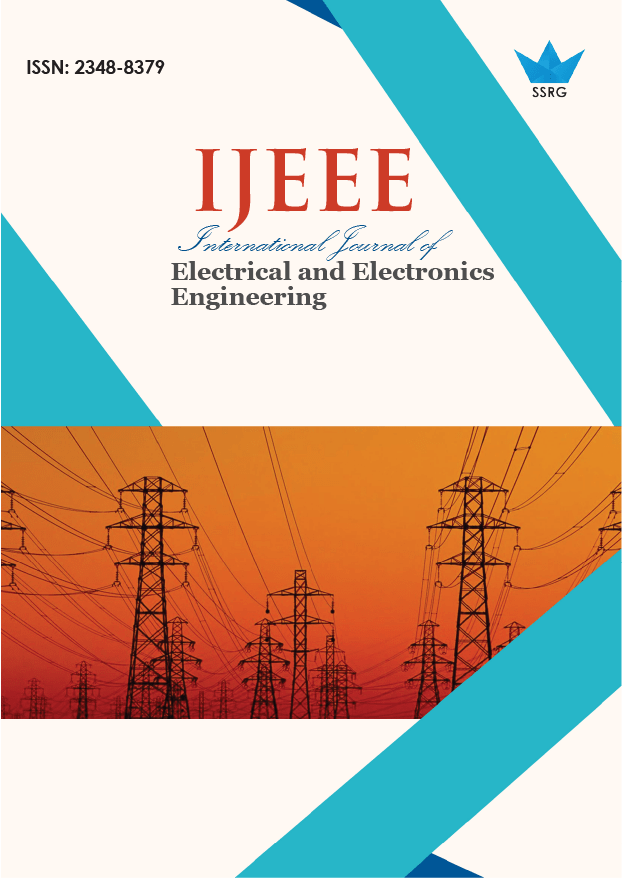
International Journal of Electrical and Electronics Engineering |
© 2024 by SSRG - IJEEE Journal |
Volume 11 Issue 12 |
Year of Publication : 2024 |
Authors : Amuthakkannan Rajakannu, Ramachandran K.P, Vijayalakshmi K, Sri Rajkavin A.V |
How to Cite?
Amuthakkannan Rajakannu, Ramachandran K.P, Vijayalakshmi K, Sri Rajkavin A.V, "Condition Monitoring of CNC Drill Bit for the Manufacturing Sector Using Wavelet Analysis and Artificial Neural Network Based on Feedforward Multilayer Perceptron (MLP)," SSRG International Journal of Electrical and Electronics Engineering, vol. 11, no. 12, pp. 61-75, 2024. Crossref, https://doi.org/10.14445/23488379/IJEEE-V11I12P106
Abstract:
Real-time condition monitoring and precision health assessment systems are necessary for effective maintenance programs in the industrial sector. Rapid advancements in information technology and other engineering technologies have invited more proactive attention from research and development in industrial sectors, particularly in condition monitoring of machines and related Industrial processes. In this work, drill bit condition monitoring techniques have been developed based on wavelet analysis and Artificial Neural Networks (ANN) for automatic drill bit fault detection and classification. An experimental work has been conducted to capture the vibration signals for analysis. The CNC drill machine uses a high-carbon steel drill bit and mild steel material as work pieces in this experiment. The cutting condition parameters are kept constant, and the wear level varies from 0.2 to 0.6 mm. Using an accelerometer, the Data Acquisition system (DAQ) with Lab VIEW software captures the vibration signals for drill bits with different wear conditions. The captured vibration data are analyzed using Continuous Wavelet Transform (CWT) with Morlet and Daubechies wavelet as prime functions. The CWT coefficient is generally used to generate the input features to ANN for automatic tool condition classification, with two outputs (0, 1) for healthy and (1, 0) for faulty. The outcome of ANN showed 98% accuracy in the wear prediction, and these results show the effectiveness of the combed WT and ANN for the automatic classification of tool wear conditions with a high success rate.
Keywords:
Artificial Neural Network, Condition monitoring, Lab VIEW software, Wavelets transform analysis.
References:
[1] Akhil A. Deshpande, Vinayak V. Kulkarni, and Vinayak R. Patil, “Experimental Comparison of Bearing Vibration Amplitudes Obtained Using MATLAB and LabVIEW Software for Developing a Condition Monitoring System,” IAETSD Journal for Advanced Research in Applied Sciences, vol. 4, no. 1, pp. 138-145, 2017.
[2] Mustafa Kuntoğlu et al., “A Review of Indirect Tool Condition Monitoring Systems and Decision-Making Methods in Turning: Critical Analysis and Trends,” Sensors, vol. 21, no. 1, 2021.
[CrossRef] [Google Scholar] [Publisher Link]
[3] Qiao Sun et al., “Feature Extraction with Discrete Wavelet Transform for Drill Wear Monitoring,” Journal of Vibration and Control, vol. 11, no. 11, pp. 1375-1396, 2005.
[CrossRef] [Google Scholar] [Publisher Link]
[4] Masoud Hatami Garousi et al., “Vibration Analysis of a Centrifugal Pump with Healthy and Defective Impellers and Fault Detection Using Multi-Layer Perceptron,” Eng, vol. 5, no. 4, pp. 2511-2530, 2024.
[CrossRef] [Google Scholar] [Publisher Link]
[5] Yasir Hassan Ali, “Artificial Intelligence Application in Machine Condition Monitoring and Fault Diagnosis,” Artificial Intelligence - Emerging Trends and Applications, pp. 275-291, 2018.
[CrossRef] [Google Scholar] [Publisher Link]
[6] Lior Kitain, Condition Monitoring in the Oil and Gas Industry, Medium, 2018. [Online]. Available: https://medium.com/@lior.kitain/condition-monitoring-in-the-oil-and-gas-industry-991805ea9335
[7] Monica Tiboni, and Carlo Remino, “Condition Monitoring of Pneumatic Drive Systems Based on the AI Method Feed-Forward Backpropagation Neural Network,” Sensors, vol. 24, no. 6, 2024.
[CrossRef] [Google Scholar] [Publisher Link]
[8] Miho Klaic, Tomislav Staroveski, and Toma Udiljak, “Tool Wear Classification Using Decision Treesin Stone Drilling Applications: A Preliminary Study,” Procedia Engineering, vol. 69, pp. 1326-1336, 2014.
[CrossRef] [Google Scholar] [Publisher Link]
[9] Rui Zhao et al., “Deep Learning and Its Applications to Machine Health Monitoring,” Mechanical Systems and Signal Processing, vol. 115, pp. 213-237, 2019.
[CrossRef] [Google Scholar] [Publisher Link]
[10] P. Krishnakumar, K. Rameshkumar, and K.I. Ramachandran, “Machine Learning Based Tool Condition Classification Using Acoustic Emission and Vibration Data in High-Speed Milling Process Using Wavelet Features,” Intelligent Decision Technologies, vol. 12, no. 2, pp. 265-282, 2018.
[CrossRef] [Google Scholar] [Publisher Link]
[11] Yaochen Shi et al., “Wear Identification of Vibration Drilling Bit Based on Improved LMD and BP Neural Network,” Mathematical Problems in Engineering, vol. 2020, no. 1, 2020.
[CrossRef] [Google Scholar] [Publisher Link]
[12] Lang Dai et al., “An Improved Deep Learning Model for Online Tool Condition Monitoring Using Output Power Signals,” Shock and Vibration, vol. 2020, no. 1, 2020.
[CrossRef] [Google Scholar] [Publisher Link]
[13] Qun Wang et al., “Overview of Tool Wear Monitoring Methods Based on Convolutional Neural Network,” Applied Sciences, vol. 11, no. 24, 2021.
[CrossRef] [Google Scholar] [Publisher Link]
[14] Juan Luis Ferrando Chacón et al., “A Novel Machine Learning-Based Methodology for Tool Wear Prediction Using Acoustic Emission Signals,” Sensors, vol. 21, no. 17, 2021.
[CrossRef] [Google Scholar] [Publisher Link]
[15] Petr Kolar et al., “Indirect Drill Condition Monitoring Based on Machine Tool Control System Data,” MM Science Journal, pp. 5905-5912, 2022.
[CrossRef] [Google Scholar] [Publisher Link]
[16] Tim Reeber et al., “Tool Condition Monitoring in Drilling Processes Using Anomaly Detection Approaches Based on Control Internal Data,” Procedia CIRP, vol. 121, pp. 216-221, 2024.
[CrossRef] [Google Scholar] [Publisher Link]
[17] Markus Netzer, Yannic Palenga, and Jürgen Fleischer, “Machine Tool Process Monitoring by Segmented Time series Anomaly Detection Using Subprocess-Specific Thresholds,” Production Engineering, vol. 16, pp. 597-606, 2022.
[CrossRef] [Google Scholar] [Publisher Link]
[18] Shixu Sun et al., “A Semisupervised Autoencoder-Based Method for Anomaly Detection in Cutting Tools,” Journal of Manufacturing Processes, vol. 93, pp. 315-327, 2023.
[CrossRef] [Google Scholar] [Publisher Link]
[19] Imran Ahmed et al., “A Smart-Anomaly-Detection System for Industrial Machines Based on Feature Autoencoder and Deep Learning,” Micromachines, vol. 14, no. 1, 2023.
[CrossRef] [Google Scholar] [Publisher Link]
[20] Guang Li et al., “Deep Anomaly Detection for CNC Machine Cutting Tool Using Spindle Current Signals,” Sensors, vol. 20, no. 17, 2020.
[CrossRef] [Google Scholar] [Publisher Link]
[21] Tim Von Hahn, and Chris K. Mechefske, “Self-Supervised Learning for Tool Wear Monitoring with a Disentangled-Variational-Autoencoder,” International Journal of Hydromechatronics, vol. 4, no. 1, pp. 69-98, 2021.
[CrossRef] [Google Scholar] [Publisher Link]
[22] Vishy Karri, and Tossapol Kiatcharoenpol, “Tool Condition Monitoring in Drilling Using Artificial Neural Networks,” AI 2003: Advances in Artificial Intelligence, pp. 293-301, 2003.
[CrossRef] [Google Scholar] [Publisher Link]
[23] Srinivasan Ramakrishnan, “Introductory Chapter: Wavelet Theory and Modern Applications,” Modern Applications of Wavelet Transform, IntechOpen, 2024.
[CrossRef] [Google Scholar] [Publisher Link]
[24] Bruno Torrésani, “An Overview of Wavelet Analysis and Time-Frequency Analysis (A Minicourse),” International Workshop on Self-Similar Systems, pp. 9-34, 1998.
[Google Scholar] [Publisher Link]
[25] Saiyam Sakhuja, Limitations of Fourier Transform and the Role of Wavelet Transform, Medium, 2024. [Online]. Available: https://sakhujasaiyam.medium.com/disadvantages-of-fourier-transform-and-the-role-of-wavelet-transform-a4218d8cc6de
[26] H.S. Kumar, and Gururaj Upadhyaya, “Fault Diagnosis of Rolling Element Bearing Using Continuous Wavelet Transform and K- Nearest Neighbor,” Materials Today: Proceedings, vol. 92, pp. 56-60, 2023.
[CrossRef] [Google Scholar] [Publisher Link]
[27] Yanxue Wang et al., “Spectral Kurtosis for Fault Detection, Diagnosis and Prognostics of Rotating Machines: A Review with Applications,” Mechanical Systems and Signal Processing, vol. 66-67, pp. 679-698, 2016.
[CrossRef] [Google Scholar] [Publisher Link]
[28] Jennifer L. Green et al., “Descriptive Statistics,” International Encyclopedia of Education (Fourth Edition), pp. 723-733, 2023.
[CrossRef] [Publisher Link]
[29] Khalil Khanafer, Junqian Cao, and Hussein Kokash, “Condition Monitoring in Additive Manufacturing: A Critical Review of Different Approaches,” Journal of Manufacturing and Materials Processing, vol. 8, no. 3, 2024.
[CrossRef] [Google Scholar] [Publisher Link]
[30] Matias Marticorena et al., “RA-6 Research Reactor Automatic Condition Monitoring System - Applications for Predictive Maintenance,” International Conference on Research Reactors: Addressing Challenges and Opportunities to Ensure Effectiveness and Sustainability, Buenos Aires, Argentina, 2019.
[Google Scholar] [Publisher Link]
[31] Yuqing Zhou et al., “A New Tool Wear Condition Monitoring Method Based on Deep Learning under Small Samples,” Measurement, vol. 189, 2022.
[CrossRef] [Google Scholar] [Publisher Link]
[32] Onur Surucu, Stephen Andrew Gadsden, and John Yawney, “Condition Monitoring Using Machine Learning: A Review of Theory, Applications, and Recent Advances,” Expert Systems with Applications, vol. 221, 2023.
[CrossRef] [Google Scholar] [Publisher Link]
[33] R.R. Srikant, P. Vamsi Krishna, and N.D. Rao, “Online Tool Wear Prediction in Wet Machining Using Modified Back Propagation Neural Network,” Proceedings of the Institution of Mechanical Engineers, Part B: Journal of Engineering Manufacture, vol. 225, no. 7, pp. 1009-1018, 2011.
[CrossRef] [Google Scholar] [Publisher Link]
[34] Issam Abu-Mahfouz, “Drilling Wear Detection and Classification Using Vibration Signals and Artificial Neural Network,” International Journal of Machine Tools & Manufacture, vol. 43, no. 7, pp. 707-720, 2003.
[CrossRef] [Google Scholar] [Publisher Link]
[35] Luis A. Camuñas-Mesa, Bernabé Linares-Barranco, and Teresa Serrano-Gotarredona, “Neuromorphic Spiking Neural Networks and their Memristor-CMOS Hardware Implementations,” Materials, vol. 12, no. 17, 2019.
[CrossRef] [Google Scholar] [Publisher Link]
[36] Monica Tiboni et al., “A Review on Vibration-Based Condition Monitoring of Rotating Machinery,” Applied Sciences, vol. 12, no. 3, 2022.
[CrossRef] [Google Scholar] [Publisher Link]
[37] Irie Daniela Yamaguti Ebner et al., “Wavelet Analysis and Artificial Neural Networks Applied to Condition Monitoring in High Speed Milling,” ABCM Symposium Series in Mechatronics, vol. 2, pp. 121-128, 2006.
[Google Scholar] [Publisher Link]
[38] Elyas Salimi, and Behrouz Niromandfam, “Condition Monitoring of Hydraulic Pump by Wavelet Transform and Artificial Neural Network,” Journal of Novel Applied Science, vol. 4, no. 11, pp. 1123-1128, 2015.
[Google Scholar] [Publisher Link]
[39] Ana Andrade et al., “Development of a Methodology Using Artificial Neural Network in the Detection and Diagnosis of Faults for Pneumatic Control Valves,” Sensors, vol. 21, no. 3, 2021.
[CrossRef] [Google Scholar] [Publisher Link]
[40] Hongche Wang et al., “A Novel Tool Condition Monitoring Based on Gramian Angular Field and Comparative Learning,” International Journal of Hydromechatronics, vol. 6, no. 2, pp. 93-107, 2023.
[CrossRef] [Google Scholar] [Publisher Link]
[41] Snehsheel Sharma, S.K. Tiwari, and Sukhjeet Singh, “Diagnosis of Gear Tooth Fault in a Bevel Gearbox Using Discrete Wavelet Transform and Autoregressive Modeling,” Life Cycle Reliability and Safety Engineering, vol. 8, pp. 21-32, 2019.
[CrossRef] [Google Scholar] [Publisher Link]
[42] Anil Kumar et al., “Latest Innovations in the Field of Condition-Based Maintenance of Rotatory Machinery: A Review,” Measurement Science and Technology, vol. 35, no. 2, 2023.
[CrossRef] [Google Scholar] [Publisher Link]