Operations Management Model for Automotive Service Workshops in Peru: Service Level Improvement through Lean Manufacturing and SLP
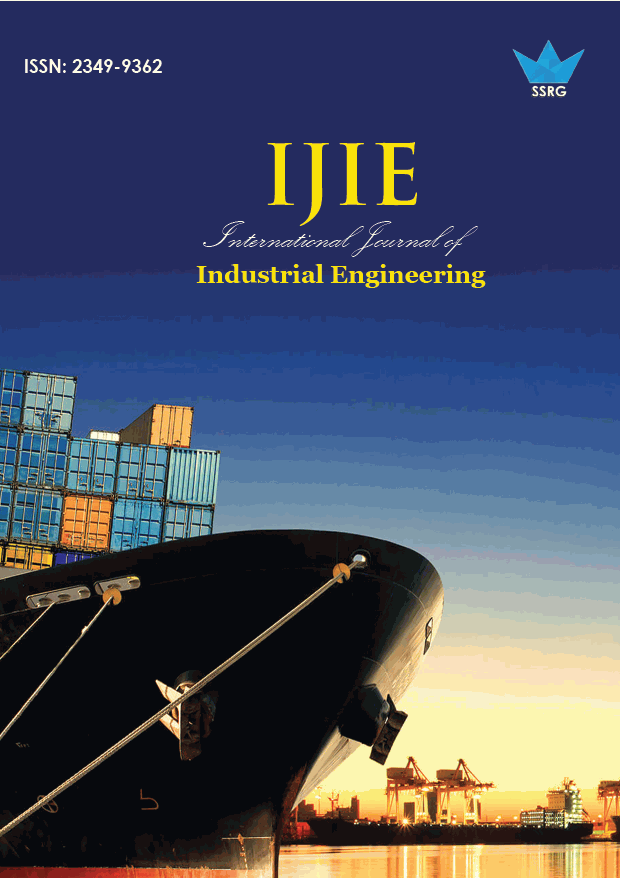
International Journal of Industrial Engineering |
© 2025 by SSRG - IJIE Journal |
Volume 12 Issue 1 |
Year of Publication : 2025 |
Authors : Ximena Fiorella Miranda-Bazán, Alvaro Adrián Taboada-Ramírez, Wilson David Calderón-Gonzales |
How to Cite?
Ximena Fiorella Miranda-Bazán, Alvaro Adrián Taboada-Ramírez, Wilson David Calderón-Gonzales, "Operations Management Model for Automotive Service Workshops in Peru: Service Level Improvement through Lean Manufacturing and SLP," SSRG International Journal of Industrial Engineering, vol. 12, no. 1, pp. 12-21, 2025. Crossref, https://doi.org/10.14445/23499362/IJIE-V12I1P102
Abstract:
Latin America's automotive repair SME sector faces persistent operational challenges that hinder its efficiency and competitiveness. Prior studies have explored Lean methodol ogies and Systematic Layout Planning (SLP) in large-scale industries, leaving a gap in adapting these tools for smaller automotive workshops. The discrepancies above are sought to be solved through the formulation and verification of an integrated operations management model that combines the Lean Manufacturing approach and SLP. It applied the 5S technique, layout optimization, and process standardization to minimize movements and delays. The verification step showed substantial improvement in the service level from 84.91% to 95.00%, along with a 32.99% improvement in the diagnostic time. These results demonstrate that the model can enhance service quality and operational efficiency and contribute to the academic literature and practice by providing a model usable by SMEs. Further research should assess the sustainability of the model and the use of digital monitoring systems.
Keywords:
Continuous improvement, Process optimization, Waste reduction, Workflow efficiency, Automotive service SMEs.
References:
[1] Ernest Emeka Izogo, and Ike-Elechi Ogba, “Service Quality, Customer Satisfaction and Loyalty in Automobile Repair Services Sector,” International Journal of Quality & Reliability Management, vol. 32, no. 3, pp. 250-269, 2015.
[CrossRef] [Google Scholar] [Publisher Link]
[2] Tamas Bence Venczel, Krisztian Hriczo, and Laszlo Berenyi, “Agile in Automotive: A Literature Review,” Journal of Physics: Conference Series, vol. 2848, pp. 1-8, 2024.
[CrossRef] [Google Scholar] [Publisher Link]
[3] Ernest Emeka Izogo, “Customers’ Service Quality Perception in Automotive Repair,” African Journal of Economic and Management Studies, vol. 6, no. 3, pp. 272-288, 2015.
[CrossRef] [Google Scholar] [Publisher Link]
[4] Fuad Dwi Hanggara, “Facility Layout Planning in Small Industry to Increase Efficiency (Case Study: Big Boy Bakery, Batam, Kepulauan Riau, Indonesia),” Journal of Industrial Engineering Management, vol. 5, no. 2, pp. 72-81, 2020.
[CrossRef] [Google Scholar] [Publisher Link]
[5] Jorge Luis Garcia-Alcaraz et al., “Lean Manufacturing Tools Applied to Material Flow and Their Impact on Economic Sustainability,” Sustainability, vol. 13, no. 19, pp. 1-18, 2021.
[CrossRef] [Google Scholar] [Publisher Link]
[6] Sharfuddin Ahmed Khan et al., “Application of Continuous Improvement Techniques to Improve Organization Performance: A Case Study,” International Journal of Lean Six Sigma, vol. 10, no. 2, pp. 542-565, 2019.
[CrossRef] [Google Scholar] [Publisher Link]
[7] Qing Hu et al., “Lean Implementation within SMEs: A Literature Review,” Journal of Manufacturing Technology Management, vol. 26, no. 7, pp. 980-1012, 2015.
[CrossRef] [Google Scholar] [Publisher Link]
[8] Saumyaranjan Sahoo, “Assessing Lean Implementation and Benefits within Indian Automotive Component Manufacturing SMEs,” Benchmarking: An International Journal, vol. 27, no. 3, pp. 1042-1084, 2020.
[CrossRef] [Google Scholar] [Publisher Link]
[9] Vikas Swarnakar, and S. Vinodh, “Deploying Lean Six Sigma Framework in an Automotive Component Manufacturing Organization,” International Journal of Lean Six Sigma, vol. 7, no. 3, pp. 267-293, 2016.
[CrossRef] [Google Scholar] [Publisher Link]
[10] Aline Dresch et al., “Inducing Brazilian Manufacturing SMEs Productivity with Lean Tools,” International Journal of Productivity and Performance Management, vol. 68, no. 1, pp. 69-87, 2019.
[CrossRef] [Google Scholar] [Publisher Link]
[11] Jugraj Singh Randhawa, and Inderpreet Singh Ahuja, “Examining the Role of 5S Practices as a Facilitator of Business Excellence in Manufacturing Organizations,” Measuring Business Excellence, vol. 21, no. 2, pp. 191-206, 2017.
[CrossRef] [Google Scholar] [Publisher Link]
[12] Vitoria Amaral, Ana C. Ferreira, and Bruna Ramos, “Internal Logistics Process Improvement using PDCA: A Case Study in the Automotive Sector,” Business Systems Research, vol. 13, no. 3, pp. 100-115, 2022.
[CrossRef] [Google Scholar] [Publisher Link]
[13] Franziska Scharold, Julian Schrof, and Kristin Paetzold-Byhain, “Analysis of the Correlation Between Agile Team Maturity and Standardised Key Performance Indicators in Automotive Development,” Proceedings of the International Conference on Engineering Design (ICED23), Bordeaux, France, vol. 3, pp. 573-582, 2023.
[CrossRef] [Google Scholar] [Publisher Link]
[14] Jugraj Singh Randhawa, and Inderpreet Singh Ahuja, “Empirical Investigation of Contributions of 5S Practice for Realizing Improved Competitive Dimensions,” International Journal of Quality & Reliability Management, vol. 35, no. 3, pp. 779-810, 2018.
[CrossRef] [Google Scholar] [Publisher Link]
[15] Alberto Bayo‐Moriones, Alejandro Bello‐Pintado, and Javier Merino‐Diaz de Cerio, “5S Use in Manufacturing Plants: Contextual Factors and Impact on Operating Performance,” International Journal of Quality & Reliability Management, vol. 27, no. 2, pp. 217-230, 2010.
[CrossRef] [Google Scholar] [Publisher Link]
[16] Mariano Jimenez et al., “Extension of the Lean 5S Methodology to 6S with An Additional Layer to Ensure Occupational Safety and Health Levels,” Sustainability, vol. 11, no. 14, pp. 1-18, 2019.
[CrossRef] [Google Scholar] [Publisher Link]
[17] Bhavesh Kanabar et al., “The Impact and Challenges of the Implementation of 5S Methodology in Healthcare Settings: A Systematic Review,” Cureus, vol. 16, no. 7, pp. 1-13, 2024.
[CrossRef] [Google Scholar] [Publisher Link]
[18] Carmen Jaca et al., “Learning 5S Principles from Japanese Best Practitioners: Case Studies of Five Manufacturing Companies,” International Journal of Production Research, vol. 52, no. 15, pp. 4574-4586, 2014.
[CrossRef] [Google Scholar] [Publisher Link]
[19] Manisha Singh et al., “Implementation of 5S Management Method for Lean Healthcare in Clinical Biochemistry Laboratory of a Government Hospital in India,” International Journal of Health Sciences, vol. 6, no, s3, pp. 12124-12135, 2022.
[CrossRef] [Google Scholar] [Publisher Link]
[20] Jugraj Singh Randhawa, and Inderpreet Singh Ahuja, “An Investigation into Manufacturing Performance Achievements Accrued by Indian Manufacturing Organization through Strategic 5S Practices,” International Journal of Productivity and Performance Management, vol. 67, no. 4, pp. 754-787, 2018.
[CrossRef] [Google Scholar] [Publisher Link]
[21] John H.T. Waldhausen et al., “Application of Lean Methods Improves Surgical Clinic Experience,” Journal of Pediatric Surgery, vol. 45, no. 7, pp. 1420-1425, 2010.
[CrossRef] [Google Scholar] [Publisher Link]
[22] Jency Philipose, “Trauma Resuscitation Room Organization Using 5S Methodology: A Quality Improvement Initiative,” Journal of Trauma Nursing, vol. 29, no. 5, pp. 272-277, 2022.
[CrossRef] [Google Scholar] [Publisher Link]
[23] Jugraj Singh Randhawa, and Inderpreet Singh Ahuja, “Structural Equation Modeling for Validating Impact of 5S Implementation on Business Excellence of Manufacturing Organizations,” International Journal of Quality & Reliability Management, vol. 34, no. 9, pp. 1592-1615, 2017.
[CrossRef] [Google Scholar] [Publisher Link]
[24] Fengxiao Yu et al., “An Analysis of Optimization for Car PBS Scheduling Based on Greedy Strategy State Transition Algorithm,” Applied Sciences, vol. 13, no. 10, pp. 1-17, 2023.
[CrossRef] [Google Scholar] [Publisher Link]