Reduction of Long Delivery Time by Implementing Advanced Kaizen (Problem Solving Approach)
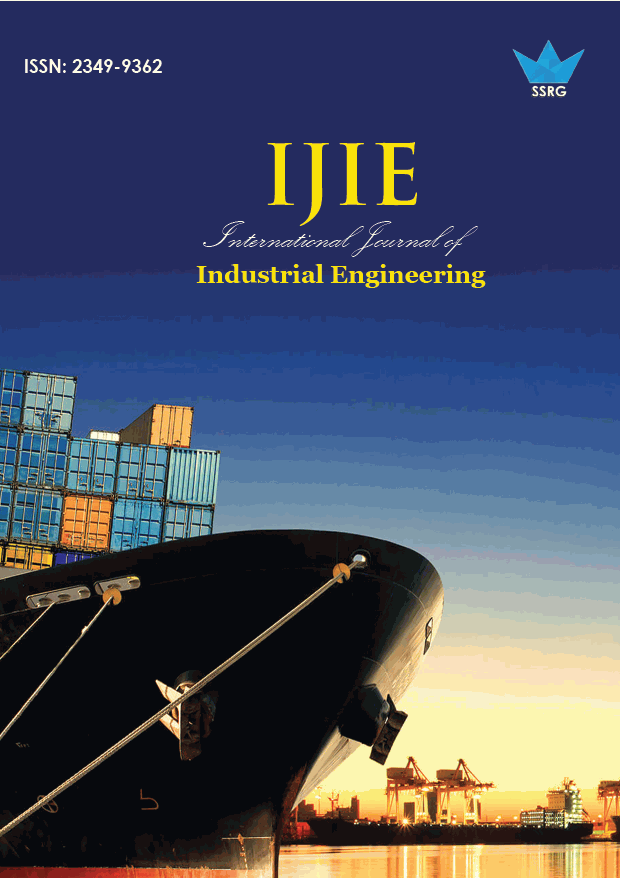
International Journal of Industrial Engineering |
© 2017 by SSRG - IJIE Journal |
Volume 4 Issue 3 |
Year of Publication : 2017 |
Authors : Haftu Hailu and Tewedros Hailu |
How to Cite?
Haftu Hailu and Tewedros Hailu, "Reduction of Long Delivery Time by Implementing Advanced Kaizen (Problem Solving Approach)," SSRG International Journal of Industrial Engineering, vol. 4, no. 3, pp. 26-48, 2017. Crossref, https://doi.org/10.14445/23499362/IJIE-V4I6P103
Abstract:
The purpose of the project is to minimize existing long delivery time of shoe Venice model by integration of 7QC tools and Quality control story formula. At this time most of Ethiopian manufacturing industries are facing big challenges to exceed their customers’ expectations. For the reason that these industries could not achieve the delivery time that fixed by the customer. Sheba leather Industry PLC is one of Ethiopian leather and shoe manufacturing industry facing this problem. As well, generating skilled manpower capable of continuously solve problems analytically. At the time of the project, there was customer complaint. This was originated from not achieving delivery time of Venice model shoe. It takes more than three months to dispatch 240 pairs of Venice model shoe. In addition, there was concentration of wastes like transportation, waiting, defect and inventory. The methodology followed for this project is problem solving approach. Ten steps of quality control story formula integrated with quality control seven tools were used. The findings of the project after the completion of nine month implementation period, the team confirmed the result with set target by holding again process analysis. 38 activities were non-value adding that are wastes. Due to this reason, the delivery time is shortening by 18,236.55 min with 51.08 % improvement. In addition, process analysis and application of quality control process chart were familiarized. Any manufacturing industries can similarly use and follow the problem solving approach and 7 QC tools to eliminate wastes. Due to time constraint, the project is only focused on Venice model shoe, however there were more than 30 model shoe types. At the end, the cross functional team members should solve another chronic problem by practicing problem solving approach. The top management should monitor and evaluate the activities in order to sustain intermediate level kaizen implementation.
Keywords:
Delivery time, 7 QC Tools, QC story, Intermediate level kaizen, Cross-functional team, Sheba.
References:
[1]. Anonymous, Manufacturing Lead time, http://www.businessdictionary.com/definition/manufacturing-leadtime.
[2]. html#ixzz25yFudpnc, Date of retrieval: 29/09/2011
[3]. Antonides, G., Verhoef, P.C., and Aalst, M.V., (2002), Consumer Perception and Evaluation of Waiting Time: A Field Experiment, Journal of Consumer Psychology Vol. 12, No. 3, pp. 193-202
[4]. Basu, R. (2004).Implementing Quality–A Practical Guide to Tools and Techniques, Thomson Learning, UK.
[5]. Bielen, F., and Demoulin, N., (2007), Waiting time influence on the satisfaction-loyalty relationship in services, Managing Service Quality, Vol. 17, No. 2, pp. 174-19
[6]. Deepak Mavatoor (2013). Flow Manufacturing: How to Achieve Superior Customer Response. Cognizant 20-20 Insights.
[7]. Ethiopia Kaizen Institute (2011). The Study on Quality and Productivity Improvement manual in Ethiopia.
[8]. Fred N. Horning, John McCann (2003). Cycle Time Reduction Gives Life to Productivity
[9]. Kehone, Dennis. 1990. The fundamental of Quality Management London: Chapman and Hall.
[10]. Mirko Soković1, Jelena Jovanović, Zdravko Krivokapić, Aleksandar Vujović (2009). Basic Quality Tools in Continuous
[11]. Improvement Process. Journal of Mechanical Engineering 55(2009)5, Start Page-End Page.
[12]. Muhammad Abdus Samad, MD. SaifulAlam, and NishatTusnim (2013). Value stream mapping to reduce manufacturing lead time in a semi-automanted factory. ATE ISSN: 2221-4267, Volume 02 Issue 06
[13]. Osanna, P.H., Durakbasa, M.N., Afjehi- Sadat, A. (2004). Quality in Industry, Vienna University of Technology, TU AuM, Wien.
[14]. Pryun, A., and Smidts, A., (1998), Effects of waiting on the satisfaction with the service: Beyond objective time measures, International Journal of Research in Marketing, Vol. 15, No. 4, pp. 321-334
[15]. Ranjan Raj Urs S, Dr. B.P.Mahesh, Sandesh S (2014). On-Time Delivery Improvement Using Lean Concepts
[16]. Sheba Leather Industry (2015). Business Plan 2015 to 2020 E.C.
[17]. Stank, T., Goldsby, T., and Vickery, S. (1999), Effect of Service Supplier Performance on Satisfaction and Loyalty of Store Managers in the Fast Food Industry, Journal of Operations Management, Vol.17, pp. 429 – 447
[18]. Tague, N.R. (2005). The quality toolbox, ASQ Quality press,Wisconsin.
[19]. Taylor, S.A., (1994), An assessment of the relationship between service quality and customer satisfaction in the formation of consumers purchase intentions, Journal of Retailing, Vol. 70, No. 2, pp. 163-178
[20]. Toyota-global.com, (2015). Toyota Global Site | Financial Highlights. Retrieved 23 January 2015, from
[21]. http://www.toyota-global.com/investors/financial_data/high-light.html
[22]. Vikas Kumar, Luciano Batista, Roger Maull, (2011) The Impact of Operations Performance on Customer Loyalty.
[23]. Service Science 3(2):158-171. https://doi.org/10.1287/serv.3.2.158