Experimental and Numerical Analysis of the Tensile Test on the A633 HSLA Steel Plate Specimens with Edge Crack
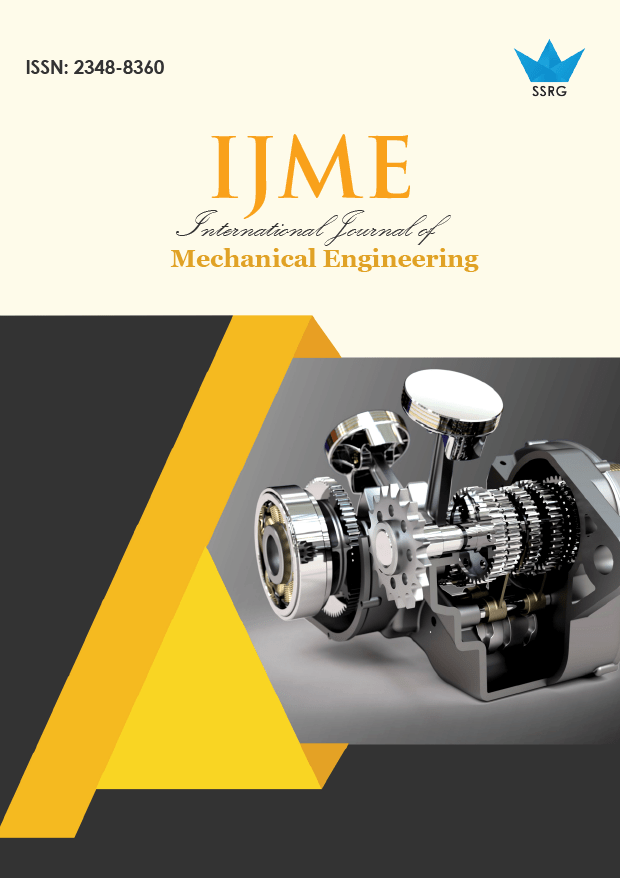
International Journal of Mechanical Engineering |
© 2014 by SSRG - IJME Journal |
Volume 1 Issue 7 |
Year of Publication : 2014 |
Authors : Shahin Nayyeri Amiri, Caesar Abishdid, Asad Esmaeily |
How to Cite?
Shahin Nayyeri Amiri, Caesar Abishdid, Asad Esmaeily, "Experimental and Numerical Analysis of the Tensile Test on the A633 HSLA Steel Plate Specimens with Edge Crack," SSRG International Journal of Mechanical Engineering, vol. 1, no. 7, pp. 16-25, 2014. Crossref, https://doi.org/10.14445/23488360/IJME-V1I7P103
Abstract:
This paper presents an experimental and numerical study of the mechanical behavior of ASTM A633 high-strength low-alloy (HSLA) steel plate specimens with edge crack at the middle during the tensile test. Experimental analysis and numerical method are used to analyze the load-displacement curve for the steel specimens with various edge crack length. Four A633 HSLA steel plate specimens are tested in FIU’s Material Laboratory using a high capacity universal testing machine, and results are compared with the mesh-free and finite element results. A mesh-free method called Reproducing Kernel Particle Method (RKPM) is used to calculate the J-integral and load-displacement. RKPM is a mesh-free technology which is used to analyze the domain of interest only with particles using Ramberg-Osgood stress-strain relationship. A numerical analysis was performed using the finite element program ANSYS to exhibit the efficacy of RKPM in analyzing crack problems. This paper studies the effect of crack length on the load-displacement curve and the J-integral of A633 HSLA specimens after tensile tests. Results of load-displacement curves and J-integral curves found using the experimental, finite element, and mesh-free methods were compared and validated against each other for samples with various crack lengths.
Keywords:
Tensile Test, A633 HSLA, Steel Plate Specimens, Edge Crack, Reproducing Kernel Particle Method, Mesh-free Technology, Load-displacement Curve, J-integral, Finite Element Method.
References:
1. ASTM, ASTM E1820-09. Standard Test Method for Measurement of Fracture Toughness. American Society for Testing and Materials, Philadelphia, 2009.
2. Liu W K, Jun S, Zhang YF (1995). Reproducing Kernel Particles Methods. International Journal for Numerical Methods in Fluids, vol. 20, pp. 1081-1106.
3. Gingold RA and Monaghan JJ (1977). Smoothed particle hydrodynamics: theory and application to non-spherical stars.” Monthly Notices Royal Astronomical Society, Vol. 181, pp. 375-389.
4. Belytschko T, Y Krongauz, D Organ, M Fleming, P Krysl, (1996). Meshless Methods: An overview and recent developments Computer methods in applied mechanics and engineering, Vol 139, pp3-47.
5. Zhu T, Atluri S N (1998). A modified collocation method and a penalty formulation for enforcing the essential boundary conditions in the element free Galerkin method. Computational Mechanics, vol. 21, pp. 211-222.
6. Rice J R (1968). A path independent integral and the approximate analysis of strain concentration by notches and cracks. Journal of Applied Mech., vol. 35, pp. 379-386.
7. Ernst H A, Paris P C, Rossow M, Hutchinson J W, (1979). Analysis of load displacement relationship to determine J-R curve and tearing instability material properties. Fracture Mechanics. ASTM STP 677, C. W. Smith, Ed., American Society for Testing and Materials, Philadelphia, pp. 581-599.
8. Macon D J (2006). Nonlinear Elastic J-Integral Measurements in Mode I Using a Tapered Double Cantilever Beam Geometry. Mathematical and Computer Science, pp 33.
9. Vinnakota S (2006). Steel Structures: Behavior and LRFD. McGraw-Hill, 1 st Edition, pp. 29-46.
10. Ashby M (2006). Engineering Materials 1: An Introduction to Properties, Applications and Design. 3rd ed. Butterworth-Heinemann.
11. Celentano DJ, (2001). A Large Strain Thermovicsoplastic Formulation for the Solidification of S.G.Cast iron in a green sand mould, International journal of Plasticity,Vol.17,pp.1623-1658.
12. Gozzi J, Olsson A, and Lagerqvist O (2005). Experimental investigation of the behavior of extra high strength steel. Experimental Mechanics. Volume 45, Number 6, p. 533-540.
13. Jin X, Li G, Aluru, N R (2001). On the equivalence between leastsquares and kernel approximations in meshless methods. CMES: Computer Modeling in Engineering & Sciences, vol. 2, pp. 447-462.
14. Jacobsen TK, Sorensen BF (2001). Mode I intra-laminar crack growth in composites modeling of R-curves from measured bridging laws. Composites Part A., 32: 1-1 1.
15. Cao R, Li L, Chen JH, Zhang J, (2010). Study on compression deformation, damage and fracture behavior of TiAl alloys Part II. Fracture behavior, Materials Science and Engineering A 527 2468–2477.
16. Xia L, Shih F, Hutchinson JW, (1995). A computational approach to ductile crack growth under large-scale yielding conditions. Journal of Mech Phys Solids, 43:389–413.
17. Simonsen BC, Lauridsen LP, (2000). Energy absorption and ductile failure in metal sheets under lateral indentation by a sphere. Int J Impact Eng, 24:1017–39.
18. Panda S K, Kumar, D R, Kumar, H, Nath, AK (2007). Characterization of tensile properties of tailor welded IF steel sheets and their formability in stretch forming, Journal of Materials Processing Technology 183, 321–332.
19. Grønwold E (2003). Experimental set-up for large-scale fracture mechanics testing. Master thesis, Department of Mechanical Engineering, Maritime Engineering, and Technical University of Denmark.
20. Hajali, M., & Abishdid, C. (2013). Determination of Two-Dimensional Plastic Zone Shape and SIF at Crack-Tip Using RKPM. Journal of Iron and Steel Research, International, 20(12), 103-114.
21. Hajali, M., Abishdid, C., Johansson, S., & Moverare, J. (2013, March). 126 Evaluation of the Mode I Plastic Zone Size at the Crack Tip Using RKPM and FEM. In CP2012.
22. Hajali, M., & Abishdid, C. (2012, January). Effect of Dilation Parameter On the Stress Intensity Factor At the Crack Tip Using RKPM. In 46th US Rock Mechanics/Geomechanics Symposium. American Rock Mechanics Association.