Fabrication and Characterization of Magnesium Foam using TiH2 for Bio Medical Applications
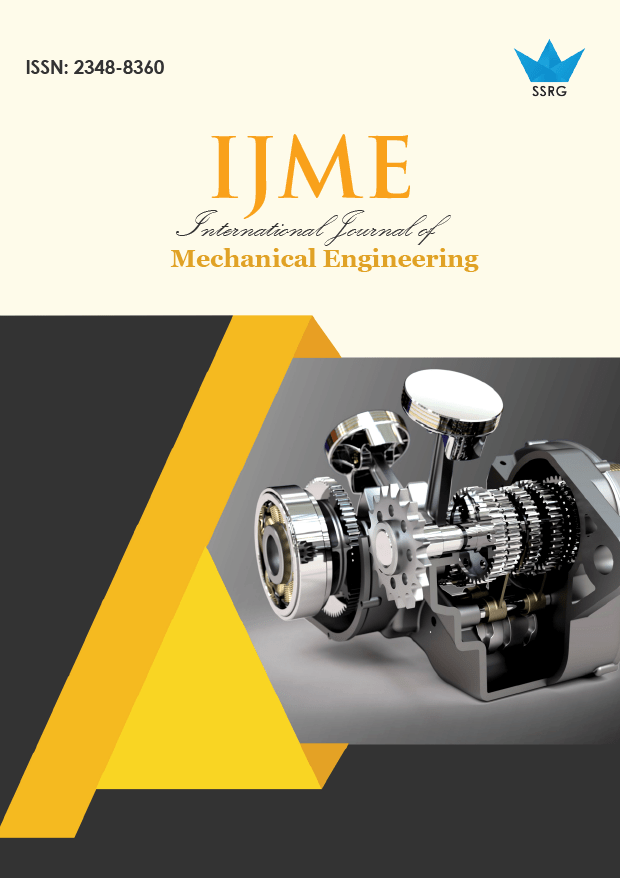
International Journal of Mechanical Engineering |
© 2019 by SSRG - IJME Journal |
Volume 6 Issue 2 |
Year of Publication : 2019 |
Authors : Augastin Santhiyagu I, Asir Samuel J, Esther Maria I, AshanAnto Fransis, Sai Charan |
How to Cite?
Augastin Santhiyagu I, Asir Samuel J, Esther Maria I, AshanAnto Fransis, Sai Charan, "Fabrication and Characterization of Magnesium Foam using TiH2 for Bio Medical Applications," SSRG International Journal of Mechanical Engineering, vol. 6, no. 2, pp. 1-7, 2019. Crossref, https://doi.org/10.14445/23488360/IJME-V6I2P101
Abstract:
Magnesium (Mg) and magnesium alloys are used for biomedical applications (e.g., Fracture fixation) since they have good mechanical properties, biocompatibilities, and reduced weight properties. The cellular structure of foam metals dissimilar to the bone; hence, magnesium foam can be used for biomedical applications. Fabrication of magnesium is a tough job due to its high risk of catching fire during the fabrication process and its low melting point. Powder metallurgy is one of the methods for fabricating Magnesium foam. Magnesium is blended with Titanium Hydride at various quantities, preformed, compacted, and cured to prepare the metal foam. The porosity and structure of the prepared metal foam are found out by SEM analysis; also hardness test is carried out. Metal foam is abundantly used in brakes absorber and a shock absorber, which is found in automobiles. Metal foam is used in automobiles. In addition, the metal, which is foamed, has good vibration resistance, disassembly, and other perfect properties when compared with foamed ceramics. Therefore, studying the compression deformation character and absorption of energy property of magnesium foam is essential.
Keywords:
Magnesium foam, Cellular structure, Powder metallurgy, SEM analysis, Titanium Hydride Deformation, Microhardness test.
References:
[1] Lefebvre, Louis-Philippe; Banhart, John; Dunand, David "Porous Metals and Metallic Foams": Current Status and
Recent Developments,2008 ref pg no: 777-785
[2] "Project report in New Energy and Industrial Technology DevelopmentOrganization (NEDO)," Japan, "Standardization of Testing Meth. of Porous Met" (in Japanese), 2006 & 2007.
[3] J.Banhart, "Progress in Materials Science" 46 (2001)pg no: 559–631
[4] Park C, Nutt SV. "Porous and cellular materials for structural applications." In: Schwartz DS, Shih, DS, Evans AG, Wadley HNG, editors. MRS Symp. Proc., vol. 521, 1998.Pg no: 315.
[5] "Mechanical properties of porous and cellular materials." In: Sieradzki K, Green DJ, Gibson LJ, editors. MRS Symp. Proc., vol. 207, 1990.
[6] Gibson LJ, "Ash by MF. Cellular solids." Cambridge, UK: Cambridge University Press, 1997.
[7] C.S.Y.Jee, N. O¨ Zgu¨ Ven, ZX. Guo, and J.R.G. Evans, "Metallurgical and material transactions" B, pg no:1346—Volume 31B, December 2000
[8] A.G.Evans, J.W. Hutchinson, and M.F. Ashby: Progr. Mater. Sci.,1999, vol. 43, pp. 171-221.[36,37]
[9] A.E.Simone and L.J. Gibson: Mater. Sci. Eng.A, 1997, vol. 229, pp.J.T. Dickey and G.P. Peterson: J. "Energy Resources
Technol.-Tran" s. VI. ASME, 1997, vol. 119, pp. 171-78
[10] Witte F, Kaese V, Haferkamp H, Switzer E, Meyer Lindenberg A, Wirth CJ, et al. "In vivo corrosion of four magnesium alloys and the associated bone
response.Biomaterials." 2005; pg no:26(17):3557-63.
[11] Saw BA. The corrosion resistance of magnesium alloys. In: DS, editor. ASM handbook volume 13a: "corrosion: fundamentals, testing and protection": UK: ASM Int.; 2003.
[12] Müller WD. NM, Zeddies M., Córsico M. "Magnesium and its Alloys as Degradable Biomaterials.Corrosion Studies Using Potential dynamics and EIS Electrochemical Techniques." J Mater Res. 2007;pg no:10(1):5-10.
[13] Kuwahara H, Al-Abdullat Y, Mazaki N, Tsutsumi S, Aizawa T. "Precipitation of magnesium apatite on pure magnesium surface during immersing in Hank's solution." Mater Trans. 2001;pg no:42:1317-21.
[14] M.Razavi, M.H. Fathi, M. Meratian, "Materials Characterization" • December 2010
[15] Song G. "Control of biodegradation of biocompatible magnesium alloy" s. CorrSci 2007;pg no: 49:1696–701.
[16] Witte F, Hort N, Vogt C, Cohen S, Kainer KU, Willumeit R. "Degradable biomaterials based on magnesium corrosion." J CurrOpin Solid State Mater Sci 2008;pg no: 12:63–72.
[17] Song YW, Shan DY, Han EH. "Electrodeposition of hydroxyapatite coating on AZ91D magnesium alloy for biomaterial application" Mater Lett 2008; pg no: 62:3276–9.
[18] Javier Trinidad,* In˜igo Marco, “GurutzeArruebarrena, Joachim Wendt, DietmarLetzig, EnekoS_aenz de Argandon˜a”and Russell Goodall, Advanced Engineering Materials • February 2014
[19] M.B.Kannan, R. K. S. Raman, Biomaterials, 2008, 29, 2306.
[20] Evarastics Polycarp, AzmiRahmat, MohdNazreeDerman, Gowon Baba "Hardness and Wear properties of Al-AlN Composite Produced using Powder Metallurgy Route,"International Journal of Engineering Trends and Technology (IJETT),
[21] F.Witte, V. Kaese, H. Haferkamp, E. Switzer, A. Meyer-Lindenberg, C. J.Wirth, H.Windhagen, Biomaterials, 2005, 26, 3557.
[22] F.Witte, F. Feyerabend, P. Maier, J. Fischer, M. Stormer, C. Blawert, W. Dietzel, N. Hort, Biomaterials 2007, 28,2163.
[23] F.Witte, J. Fisher, J. Nellesen, H. A. Crostack, V. Kaese, A. Pisch, F. Beckmann, H. Windhagen, Biomaterials 2006, 27, 1013.
[24] NT.Kirklanda, I. Kolbeinssona, T. Woodfield,c, G.J. Diasb, M.P. Staiger, "Materials Science and Engineering" B 176 (2011) 1666– 1672
[25] J.Banhart, "Manufacture, characterization, and application of cellular metals and metal foams," Progress in Materials Science 46 (2001) 559–563.
[26] T.Adachi, Y. Osako, M. Tanaka, M. Hojo, S.J. Hollister, "Framework for the optimal design of porous scaffold microstructure by computational simulation of bone regeneration," Biomaterials 27 (2006) 3964–3972.