Analysis on Effect of Machining Parameters in Oil Pump Back Plate using Response Surface Methodology
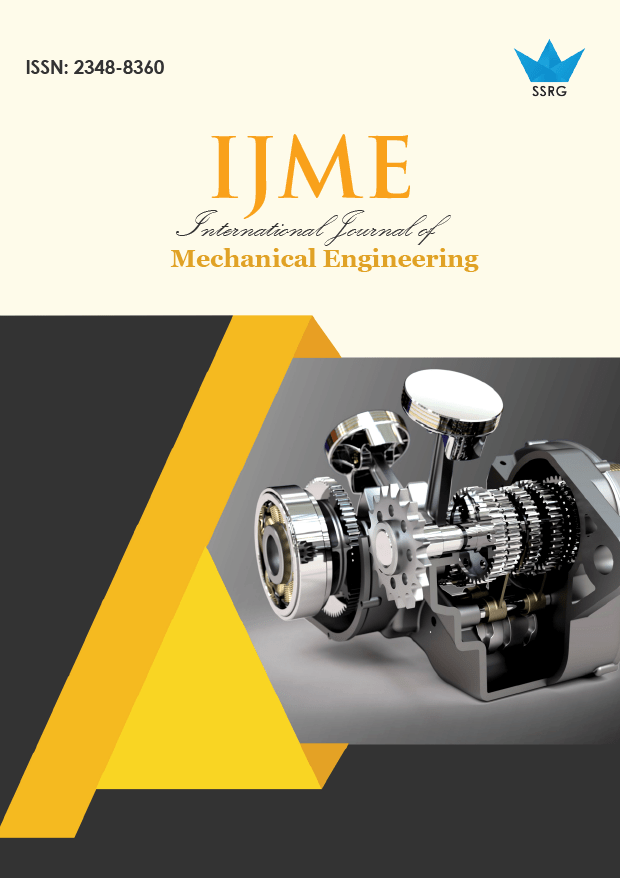
International Journal of Mechanical Engineering |
© 2020 by SSRG - IJME Journal |
Volume 7 Issue 9 |
Year of Publication : 2020 |
Authors : S. Nallusamy, Gautam Majumdar |
How to Cite?
S. Nallusamy, Gautam Majumdar, "Analysis on Effect of Machining Parameters in Oil Pump Back Plate using Response Surface Methodology," SSRG International Journal of Mechanical Engineering, vol. 7, no. 9, pp. 20-26, 2020. Crossref, https://doi.org/10.14445/23488360/IJME-V7I9P104
Abstract:
Surface finish plays an important role in auto component manufacturing industries. Optimized machining parameters are very important to produce good quality of surface finish components with lesser lead time and cost. Purpose of this research is to analyze the effect of machining parameters on the quality of the surface finish of the oil pump backplate. Oil pump base plate is made up of alloy steel EN19. The machining parameters that have been chosen are feed rate, depth of cut and spindle speed. The radial depth of cut is kept as constant of 0.12mm because the thickness of the backplate is varying from 3 mm to 6 mm. Work holding is a problem in lesser thickness plates while using high radial depth of cut. Cutting tool in this research is solid carbide end mill. After the milling process, surface roughness tests have been conducted. The results of each test specimen are analyzed, and the optimized machining parameter for EN19 steel plate surface roughness is found. The results of this research will help manufacturing industries to improve the component surface roughness and reduce production time.
Keywords:
Surface Roughness, Machining, Response Surface Methodology, EN19, Oil Pump
References:
[1] Aimin Yang, Yang Han, Yuhang Pan, Hongwei Xing and Jinze Li., Optimum surface roughness prediction for titanium alloy by adopting response surface methodology, International Journal of Results in Physics. 7 (2017) 1046–1050.
[2] Aezhisai Vallavim Muthusamy Subramanian, Mohan Das Gandhi Nachimuthu and Velmurugan Cinnasamy.,
Assessment of cutting force and surface roughness in LM6/SiCp using response surface methodology, Journal of Applied Research and Technology. 15 (2017) 283–296.
[3] Joao Eduardo Ribeiroa, Manuel Braz Cesara and Hernâni Lopes., Optimization of machining parameters to improve the surface quality, Procedia Structural Integrity, 5 (2017) 355-362.
[4] M. Subramanian, M. Sakthivel, K. Sooryaprakash and R. Sudhakaran., Optimization of Cutting Parameters for Cutting Force in Shoulder Milling of Al7075-T6 Using Response Surface Methodology and Genetic Algorithm, Procedia Engineering. 64 (2013) 690–700.
[5] Hessainia Zahia et al., On the prediction of surface roughness in the hard turning based on cutting parameters and tool vibrations, measurement. 46(5) (2013) 1671–1681.
[6] Benardos Panorios and Vosniakos George-Christopher., Offline flexible optimization of feed and speed in computer numerical control machining of sculptured surfaces exploiting dedicated cutting force metamodels, Part B: Journal of Engineering and Manufacturing. 228(6) (2014) 878–892.
[7] De Aguiar, Marcelo Mendes, Eduardo Diniz Anselmo and Pederiva Robson., Correlating surface roughness, tool wear and tool vibration in the milling process of hardened steel using long slender tools, Int Journal of Mechanical Tools Manufacturing. 68 (2013) 01–10.
[8] Pontes Fabrício Jose ., Optimization of radial basis function neural network employed for prediction of surface roughness in challenging turning process using Taguchi’s orthogonal arrays, Expert System Appliances. 39(9) (2012) 7776–87.
[9] Hanafi Issam et al., Prediction of surface roughness in turning of PEEK cf30 by using an artificial neural network, Journal of the Chinese Institute of Industrial Engineers. 29(5) (2012) 337–347.
[10] Yang Yi-Chao, Sun Da-Wen and Wang Nan-Nan., Rapid detection of browning levels of lychee pericarp as affected by moisture contents using hyperspectral imaging, Computers and Electronics in Agriculture. 113 (2015) 203–12.
[11] Wang H, To S and Chan CY., Investigation on the influence of tool-tip vibration on surface roughness and its representative measurement in ultra-precision diamond turning, International Journal of Mechanical Tools and Manufacturing. 69 (2013) 20–29.
[12] Mahesh, G., Muthu, S. and Devadasan, S. R., Prediction of surface roughness of end milling operation using genetic algorithm, International Journal of Advanced Manufacturing Technology. 77(1–4) (2015) 369–381.
[13] Joardar, H., Das, N., Sutradhar, G. and Singh, S., Application of response surface methodology for determining cutting force model in turning of LM6/SiCp metal matrix composite, measurement. 47(1) (2014) 452–465.
[14] Jeyakumar, S., Marimuthu, K. and Ramachandran, T., Prediction of cutting force, tool wear and surface roughness of Al6061/SiCp composite for end milling operations using RSM, Journal of Mechanical Science and Technology, 27(9) (2013) 2813–2822.
[15] Makadia and Nanavati., Optimization of machining parameters for turning operations based on response surface methodology, measurement. 46(4) (2013) 1521–1529.
[16] Ribeiro, J., Lopes, H., Queijo, L. and Figueiredo, D., Optimization of cutting parameters to minimize the surface roughness at the end milling process using the Taguchi method, Periodica Polytechnica Mechanical Engineering. 61 (2017) 30-35.
[17] Shivade, A., Bhagat, S., Jagdale, S., Nikam, A. and Londhe, P., Optimization of machining parameters for turning using Taguchi approach, International Journal of Recent Technology and Engineering. 3 (2014) 145-149.
[18] K. Jitendra, N.V.S. Shankar, Dr. H. Ravi Shankar, Dr. A. Gopichand., Effect of Moisture on Vibration Characteristics of SMA Particulate Reinforced Epoxy Matrix Composite, International Journal of Engineering Trends and Technology 67(6) (2019) 66-69.