Minimization of Rejection Rate and Lead Time in Medium Scale Foundry Industry by using Lean Manufacturing Practices
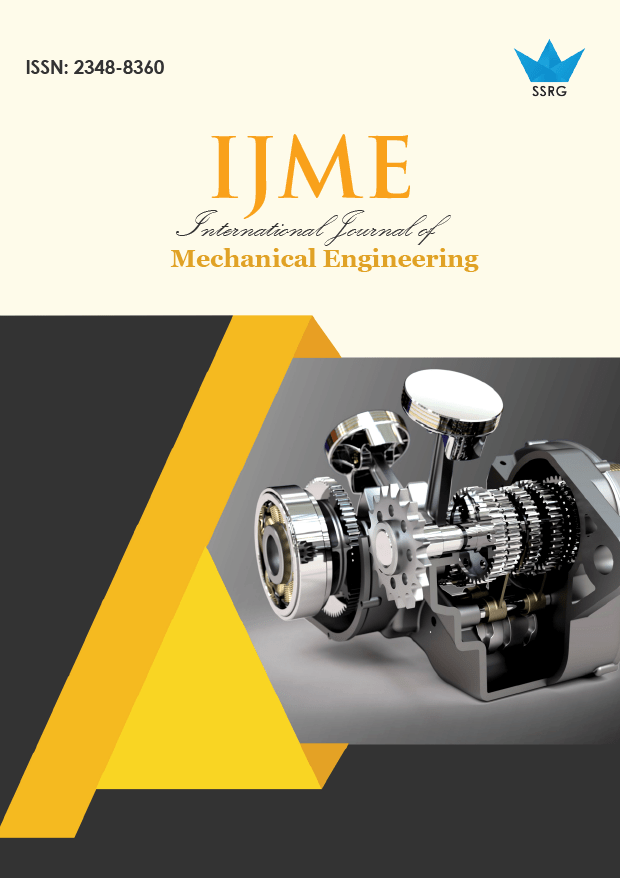
International Journal of Mechanical Engineering |
© 2020 by SSRG - IJME Journal |
Volume 7 Issue 11 |
Year of Publication : 2020 |
Authors : S. Nallusamy, Parthasarathi Chakraborty |
How to Cite?
S. Nallusamy, Parthasarathi Chakraborty, "Minimization of Rejection Rate and Lead Time in Medium Scale Foundry Industry by using Lean Manufacturing Practices," SSRG International Journal of Mechanical Engineering, vol. 7, no. 11, pp. 1-12, 2020. Crossref, https://doi.org/10.14445/23488360/IJME-V7I11P101
Abstract:
In the current globalization, production demand and customer satisfaction have progressively amplified with the development of a new technological process. This research's main objective is to reduce waste by reducing rejection in the manufacturing process and maintaining rejection percentages to meet company standards for specified departments. The industry's current rejection percentage was analyzed based on department wise and investigated the rejection rates for different products. After identifying the various causes of rejection in the current system, various methods are proposed to reduce the rejection level by identifying different defects. Different lean tools like Pareto analysis, cause and effect diagram, and VSM were applied to identify the defects and minimize rejection. The Pareto analysis was carried out to identify the major defects, and a cause and effect diagram was used to identify various methods to reduce the defects. Minitab statistical tool was used for Pareto analysis, and iGrafx is used for cause and effect diagram and also used for VSM to identify value-added, and non-value added activities. From the final results, it was noticed that the lead time was reduced by about 1000 minutes, and the rejection rate was reduced to less than 5%.
Keywords:
Foundry, Rejection, Lean Practices, Minitab, Productivity
References:
[1] Bhushan Shankar Kamble, Analysis of different sand casting defects in a medium-scale foundry industry - A review, International Journal of Innovative Research in Science, Engineering and Technology. 5(2) (2016) 102-108.
[2] B.K. Sharma, Manan Shukla, and Ganesh Dubey, Implementing lean manufacturing in the foundry industry - An overview, Indian Foundry Journal, 61(6) (2015) 112-120.
[3] Vaibhav Ingle and Madhukar Sorte, Defects, root causes in the casting process, and their remedies: review, International Journal of Engineering Research and Application. 7(3) (2017) 47-54.
[4] S. Nallusamy and Adil Ahamed M.A., Implementation of lean tools in the automotive industry for productivity enhancement - A case study, International Journal of Engineering Research in Africa, 29 (2017) 175-185.
[5] Tejaskumar S. Parsana and Mihir T. Patel, A case study: A process FMEA tool to enhance quality and efficiency of manufacturing industry, Bonfring, International Journal of Industrial Engineering and Management Science. 4(3) (2014) 65-72.
[6] Prasan Kinagi and Mench, A development of quality in casting by minimizing defects, International Journal of Recent Research in Civil and Mechanical Engg., 1(1) (2014) 31-36.
[7] P.G. Ratheesh, Standardization of work in the manufacturing industry, International Research Journal of Engineering and Technology. 2(8) (2015) 2395-2412.
[8] R. Shah and P.T. Ward, Defining and developing lean production measures, Journal of Operations Management. 25 (2007) 785-805.
[9] S. Nallusamy and Saravanan, Lean tools execution in a small scale manufacturing industry for productivity improvement-A case study, Indian Journal of Sci. and Technology. 9(35) (2016) 1-7.
[10] Shivappa, Rohit and A. Bhattacharya, Analysis of casting defects and identification of remedial measures-A diagnostic study, International Journal of Engg. Inventions. 1(6) (2012) 01-05.
[11] Avinash Juriani, Casting defects analysis in foundry and their remedial measures with industrial case studies, IOSR Journal of Mechanical and Civil Engineering. 12(6) (2015) 43-54.
[12] Kumar, Mani and Devraj, Production planning and process improvement in an impeller manufacturing using scheduling and OEE techniques, Materials Science, 5 (2014) 1710-1715.
[13] Gunji Venkata Punna Rao et al., Augmentation of production level using different lean approaches in medium scale manufacturing industries, International Journal of Mechanical Engineering and Technology, 8(12) (2017) 360-372.
[14] S.B. Dighe and A. Kakirde, Lean manufacturing implementation using value stream mapping: A case study of pumps manufacturing company, International Journal of Science and Research, 3(6) (2014) 2492-2498.
[15] A. Ashwin and K.S. Avinash, Rejection analysis in piston manufacturing unit, International Journal of Innovative Research in Science, Engineering and Technology. 4(3) (2015) 1157-1162.
[16] V. Saravanan, S. Nallusamy, and Abraham George, Efficiency enhancement in a medium-scale gearbox manufacturing company through different lean tools - A case study, Int. Journal of Engineering Research in Africa. 34 (2018) 128-138.
[17] Mayank Jha, R.K. Tyagi, and Gaurav Gupta, Reduction of rejected components in an automobile assembly line using quality tools, European Journal of Applied Engineering and Scientific Research. 2(3) (2013) 13-17.
[18] Sanjay Kumar, S.S. Mantha, and Arun Kumar Scrap, Reduction using total quality management tools, International Journal of Industrial Engineering. 16(4) (2009) 364-369.
[19] Afzal Matathil, Reduction of scrap in an electronic assembly line, SASTECH Journal, 11(2) (2012) 58-64.
[20] P. Kumar and N. Mohan Das Gandhi, Green manufacturing in the foundry, International Journal of Engineering Research & Technology. 2(1) (2013) 1203-1208.
[21] S. Nallusamy and Gautam Majumdar, Enhancement of overall equipment effectiveness using total productive maintenance in the manufacturing industry, International Journal of Performability Engineering. 13(2) (2017) 01-16.
[22] S. Sachin and J. Dileeplal, Six sigma methodology for improving the foundry industry's manufacturing process, International Journal of Advanced Engineering Research and Science 4(5) (2017) 2349-2356.
[23] S. Vinodh, K.R. Arvind and M. Somanaathan, Application of value stream mapping in an Indian camshaft manufacturing organization, Journal of Manufacturing Technology Management. 21(7) (2017) 888-900.
[24] J.M. Rohani and S.M. Zahraee, Production line analysis via value stream mapping: A lean manufacturing process of the color industry, Procedia Manufacturing. 2 (2015) 6-10.
[25] S. Gupta and S.K. Jain, A literature review of lean manufacturing, International Journal of Management Science and Engineering Management. 8(4) (2013) 241-249.
[26] S. Nallusamy and Saravanan, Enhancement of overall output on a small scale industry through VSM, line balancing, and work standardization, International Journal of Engineering Research in Africa. 26 (2016) 176-183.
[27] N. Upadhye, S.G. Deshmukh and S. Garg, Lean manufacturing system for medium-sized manufacturing enterprises: An Indian case, International Journal of Management Science and Engineering Management. 5(5) (2010) 362-375.
[28] T. Rohac and M. Januska, Value stream mapping demonstration on the real case study, Procedia Engineering. 100 (2015) 520-529.
[29] A. Gurumurthy and R. Kodali, Design of lean manufacturing systems using value stream mapping with simulation, Journal of Manufacturing Technology Mgt. 22 (2011) 444-473.
[30] M.L. Emiliani and D.J. Stec, Using value stream maps to improve leadership, The Leadership & Organization Development Journal. 25 (2004) 622- 645.