Re-design of an Aircraft Bracket Using Topology Optimization Technique
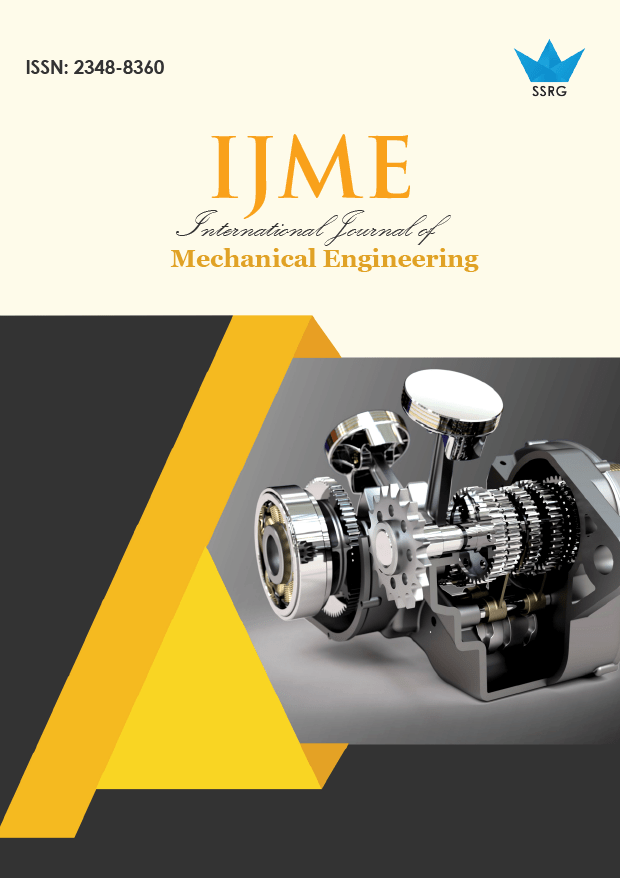
International Journal of Mechanical Engineering |
© 2020 by SSRG - IJME Journal |
Volume 7 Issue 11 |
Year of Publication : 2020 |
Authors : Mohammed Viquar Mohiuddin, Md Muqtar Ahmed Khan |
How to Cite?
Mohammed Viquar Mohiuddin, Md Muqtar Ahmed Khan, "Re-design of an Aircraft Bracket Using Topology Optimization Technique," SSRG International Journal of Mechanical Engineering, vol. 7, no. 11, pp. 42-53, 2020. Crossref, https://doi.org/10.14445/23488360/IJME-V7I11P106
Abstract:
The project's objective is to explore the possibility of using Aluminium Alloy to optimize an existing aircraft bracket using the Topology optimization technique. Topology optimization is performed using Altair Inspire software. Topology optimization is carried out with single draw shape control based on five-volume retentions each. Volume is specified as 20%, 30% 40%, 50% and 60% of the total design space volume. Post optimization analysis of all the five optimized geometries is performed. Finally, one model based on manufacturing feasibility is selected, and a smoothing operation is carried out using Polynurbs fit. SolidWorks is used to re-design the bracket by taking optimized topology design as a reference. The re-designed and original bracket prototype is printed in ABS plastic using the Fused Deposition Modeling (FDM) technique. The re-designed model is compared with the original bracket. The re-designed model has a weight reduction of 39.18% and a significant stress reduction of 15.7%, 28.2%, 39.5%, and 28.2% in vertical, horizontal, oblique, and torsional load cases, respectively. By performing, topology optimization combined with re-design, 6.3% and 5.4% lower Displacement is observed in vertical and oblique load cases, respectively, when compared with conventional geometry
Keywords:
Topology Optimization, Aircraft bracket, Shape control, Aluminium 7075, Weight reduction, design, and Non-design space.
References:
[1] Orme, M., Madera, I., Gschweitl, M., & Ferrari, M. (2018). Topology optimization for additive manufacturing as an enabler for lightweight flight hardware. Designs, 2(4) 51.
[2] Lim, S. T., & Wong, T. T. (2018, November). Unleash the potential of additive manufacturing with topology optimization. In AIP Conference Proceedings. 2035(1) 040007. AIP Publishing LLC.
[3] Rozvany, G. I. A critical review of established methods of structural topology optimization. Structural and multidisciplinary optimization, 37(3) (2009) 217-237.
[4] Reddy K, S. N., Ferguson, I., Frecker, M., Simpson, T. W., & Dickman, C. J. Topology optimization software for additive
manufacturing: A review of current capabilities and a real-world example. In International Design Engineering Technical Conferences and Computers and Information in Engineering Conference. 50107 (2016) V02AT03A029. American Society of Mechanical Engineers.
[5] Morgan, H. D., Levatti, H. U., Sienz, J., Gil, A. J., & Bould, D. C. GE Jet engine bracket challenge: a case study in sustainable design. Sustainable Design and Manufacturing. (2014) 95-107.
[6] Seong, S., Younossi, O., & Goldsmith, B. W. Titanium: industrial base, price trends, and technology initiatives. Rand Corporation (2009).
[7] Norgate, T. E., Jahanshahi, S., & Rankin, W. J. Assessing the environmental impact of metal production processes. Journal of Cleaner Production, 15(8-9) (2007) 838-848.
[8] Lu, X., Hiraki, T., Nakajima, K., Takeda, O., Matsuabe, K., Zhu, H. M., ... & Nagasaka, T. Thermodynamic analysis of separation of alloying elements in the recycling of end-of-life titanium products. Separation and purification technology, 89 (2012) 135-141.
[9] Carter, W. T., Erno, D. J., Abbott, D. H., Bruck, C. E., Wilson, G. H., Wolfe, J. B., ... & Stevens, R. G. The GE aircraft engine bracket challenge: an experiment in crowdsourcing for mechanical design concepts. In Solid Freeform Fabrication Symposium (2014) 1402-1411.
[10] Kavita, Rakesh Saxena, Lalit Ranakoti, Ashish Bedwal. Topological Optimization using Guide Weight Method. SSRG International Journal of Mechanical Engineering 2(7) (2015) 18-22.
[11] Tomlin, M., & Meyer, J. Topology optimization of an additive layer manufactured (ALM) aerospace part. In Proceeding of the 7th Altair CAE technology conference. (2011) 1-9.
[12] Ferro, C., Grassi, R., Seclì, C., & Maggiore, P. Additive manufacturing offers new opportunities in UAV research. Procedia CIRP, 41, 1004-1010 (2016).
[13] Patil, A. V., Kumar, R. C., & Patel, R. Topology Optimization of a Lower Barrel in Nose Landing Gear. International Research Journal of Engineering and Technology (IRJET). 6(6) (2019) 1493.
[14] Junk, S., Klerch, B., Nasdala, L., & Hochberg, U. Topology optimization for additive manufacturing using a component of a humanoid robot. Procedia CIRP. 70 (2018) 102-107.
[15] Brackett, D., Ashcroft, I., & Hague, R. Topology optimization for additive manufacturing. In Proceedings of the solid freeform fabrication symposium, Austin, TX. 1 (2011) 348-362.
[16] Vipul Matariya, Hiren Patel, Topological Optimization of Automobile Rotor Disk Brake, SSRG International Journal of Mechanical Engineering 6.4 (2019) 23-27.
[17] Walton, D., & Moztarzadeh, H. Design and development of an additive manufactured component by topology optimization. Procedia CIRP, 60 (2017) 205-210.
[18] Tao, W., & Leu, M. C. (2016, August). Design of lattice structure for additive manufacturing. In 2016 International Symposium on Flexible Automation (ISFA) 325-332. IEEE.
[19] Liu, J., & Ma, Y. A survey of manufacturing-oriented topology optimization methods. Advances in Engineering Software, 100 (2016) 161-175