A Study on the Machinability Characteristics of Superalloys Inconel-718 during High-Speed Milling
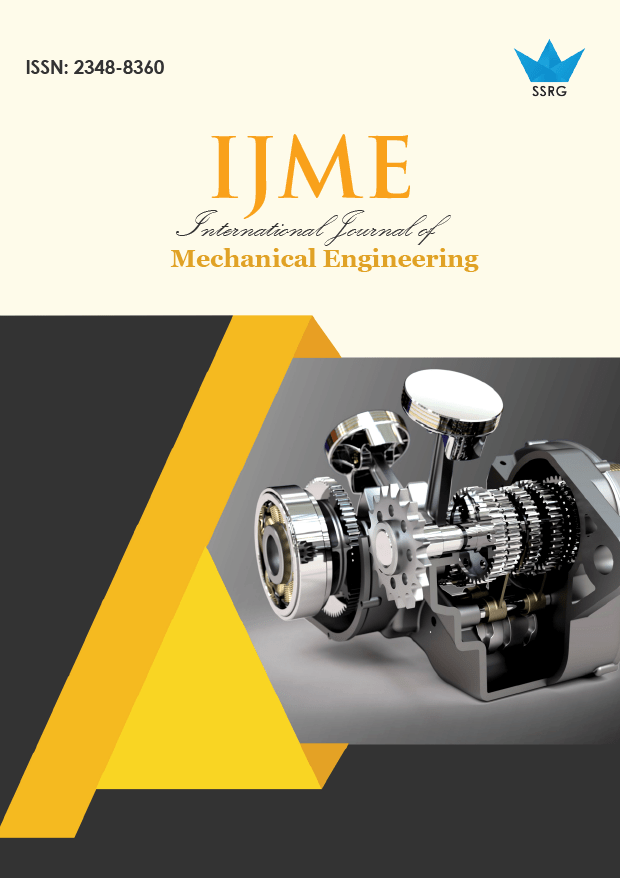
International Journal of Mechanical Engineering |
© 2021 by SSRG - IJME Journal |
Volume 8 Issue 2 |
Year of Publication : 2021 |
Authors : Nandkumar N. Bhopale, Datttatraya. S. Pimpalgaonkar |
How to Cite?
Nandkumar N. Bhopale, Datttatraya. S. Pimpalgaonkar, "A Study on the Machinability Characteristics of Superalloys Inconel-718 during High-Speed Milling," SSRG International Journal of Mechanical Engineering, vol. 8, no. 2, pp. 1-7, 2021. Crossref, https://doi.org/10.14445/23488360/IJME-V8I2P101
Abstract:
The greater challenge to manufacturing engineers is to the machining of complex shapes on Nickel-based superalloy Inconel 718 due to its physical and mechanical properties, i.e., high resistance, toughness, hardness, strength to weight ratio, and chemical property react with tool materials, creep resistance and low thermal conductivity. The Nickel-based superalloys are mainly used for turbine parts as well as high-temperature elements, although these whole properties are necessary to design requirements. The ball end milling machining process is generally used for machining complex shapes three-dimensional sculptured surfaces with definite curvature, and It's a greater challenge due to high temperature and stresses generated during the machining of Inconel 718. This paper presents a detailed experimental investigation of the effect of deflection and machining parameters on the quality of surface integrity in ball-end milling of cantilever-shaped thin plates of Inconel 718. A distinct variation is observed in the measured values of deflection of the workpiece, surface roughness, surface damage, and microhardness in different regions, i.e., fixed end, mid part, and the free end of machined surface and subsurface.
Keywords:
Superalloys, Milling, Deflection, Surface Integrity
References:
[1] Thakur A and Gangopadhyay S, State of the art in surface integrity in the machining of nickel-based superalloys, International Journal of Machine Tool and Manufacture, 100 (2016) 25-54.
[2] Ezugwu E.O., Wang, Z.M., and Machado A. R., The Machinability of nickel-based alloys: a review, Journal Materials Processing Technology, 86(1999) 1-16.
[3] Pawade R. S., Joshi S.S, Brahmankar P.K. and Rahman M, An investigation of cutting forces and surface damage in high –speed turning of Inconel 718 International Journal of Materials Processing Technology, 192 (2007) 139-146.
[4] Jean – Philippe Costes, Yoann Guillet, Gerard Poulachon, and Michel Dessoly,‘ Tool life and wear mechanism of CBN tools in the machining of Inconel 718, International Journal of Machine Tools and Manufacture, 47(2007) 1081-1087.
[5] Gajrani K, K., DhannaRam and MamillaRavi Shankar, Biodegradation and hard machining performance comparison ofeco–friendly cutting fluid and mineral oil using flood cooling and minimum quantity cutting fluid techniques, Journal of Cleaner Production, 165 (2017) 1420-1435.
[6] Arunachalam R. and Mannan M.A., Machinability of nickel-based high-temperature alloys, International Journal of Machining Science and Technology, 4(2000) 127-168.
[7] Lee P. and Altintas Y., Prediction of ball-end milling forces from orthogonal cutting Data, International Journal of Machine Tools and Manufacture, 36(1996) 1059-1072.
[8] Arizmendi M., Fernandez J., Lamikiz A., Gil A., and Sanchez J. A., Model development for the reduction of surface topography generated by ball end mills taking into account the tool parallel axis offset experimental validation, CIRP Annual Manufacturing Technology, 57(2008) 101-104.
[9] Kennametal Master Tooling Catalog, Sustainable solution for Aerospace Manufacturing and Advance Material for a new generation (2012).
[10] Montgomery D.C., Design and Analysis of Experiments, John Wiley and Sons, New York 4th Edition (1997).
[11] Prof. (Dr) .V. R. Naik, Mr.G.C.Mekalke, Mr.A.V.Sutar, Implementation of Response Surface Methodology for Analysis of Milling Process Using Multi Point Cutting Tool for Surface Finish SSRG International Journal of Mechanical Engineering 2.7(2015) 1-7.