Fractural Mechanics Crack Propagation Study of Welded Joint of Different Material and Different Crack Location in ANSYS
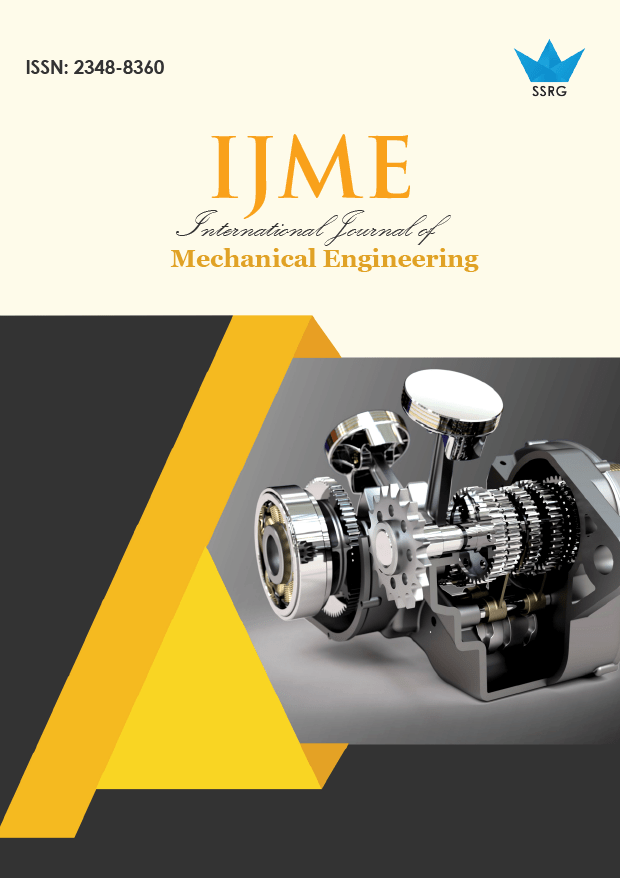
International Journal of Mechanical Engineering |
© 2021 by SSRG - IJME Journal |
Volume 8 Issue 5 |
Year of Publication : 2021 |
Authors : Mr.V.V.Hinde, Dr.S.G.Mantri |
How to Cite?
Mr.V.V.Hinde, Dr.S.G.Mantri, "Fractural Mechanics Crack Propagation Study of Welded Joint of Different Material and Different Crack Location in ANSYS," SSRG International Journal of Mechanical Engineering, vol. 8, no. 5, pp. 1-6, 2021. Crossref, https://doi.org/10.14445/23488360/IJME-V8I5P101
Abstract:
Fracture mechanics is the field of mechanics concerned with the study of the propagation of cracks in materials. It uses methods of analytical solid mechanics to calculate the driving force on a crack and those of experimental solid mechanics to characterize the material's resistance to fracture. For the simulations and calculations done in this thesis, the FE program ANSYS 19.1 is used. Six different variations of material and crack tip of the welded joint are analyzed, one where the v-notch near the weld and second one where the v-notch is near the or in the hole where bolt assembly is there. For the one joint, the crack assumes to start near the weld and for the other joint the crack can originate either from hole where the stress intensity of joint is increased.From this it is concluded that if we need more life and less stress resistance then one can use aluminum alloy. On the other hand if we need more stress resistance and less no of cycles or life of part then go for either structural steel or stainless steel. Hardness of material plays an important role in resisting crack propagation. The modules of elasticity or constant use in Paris law such as material constant (which came from experimental investigation) influence strength and life of material.
Keywords:
Fracture Mechanics, Crack tip , Welded Joint, Strength & Life of Material, Ansys.
References:
[1] P. PARIS and F. ERDOGAN A Critical Analysis of Crack Propagation Laws, Journal of Basic Engineering, DECEMBER 1963.
[2] Wolf Elber, Fatigue Crack Closure Under Cyclic Tension, Engineering Fracture Mechanics, 2 (1970) 37-45.
[3] R. J. DONAHUE et.al. Crack Opening Displacement and The Rate of Fatigue Crack Growth, International Journal of Fracture Mechanics, 8 (2) , (1972).
[4] B. Budiansky And J. W. Hutchinson, Analysis of Closure in Fatigue Crack Growth, Journal of Applied Mechanics, 45 (1978).
[5] M.H. EL HADDAD et.al, J integral applications for short fatigue cracks at notches, International Journal of Fracture, 16(1) (1980).
[6] M. H. EL HADDAD et.al., Prediction of Non-Propagating Cracks, Engineering Fracture Mechanics, 11 (1979) 573-584.
[7] G. I. BARENBLATT et.al., Incomplete Self-Similarity Of Fatigue In The Linear Range Of Crack Growth, Fatigue of Engineering Materials and Structures Pergamon Press. 3 (1981) 193-202.
[8] R. O. RITCHIE AND J. LANKFORD, Small Fatigue Cracks: A Statement of the Problem and Potential Solutions, Materials Science and Engineering, 84 (1986) 11-16.
[9] M W Brown, Aspects of fatigue crack growth, Proc Instn Mech Engineers, 202, (1988).
[10] N. A. FLECK et.al. The Cyclic Properties Of Engineering Materials, Acta metall, mater. 42(2) (1994) 365-381.
[11] F. Erdogan, Fracture mechanics, International Journal of Solids and Structures, 37 (2000) 171-183.
[12] O. NGUYEN et.al. A cohesive model of fatigue crack growth, International Journal of Fracture, 110 (2001) 351–369.
[13] Weicheng Cui, A state-of-the-art review on fatigue life prediction methods for metal structures, Journal of Marine Science Technology 7 (2002) 43–56.
[14] Neilor Cesar dos Santos And Volnei Tita and Jonas de Carvalho, Comparison Between Methods To Evaluation J-Integral On 2-D Fracture Problems, National congress of mechanical engineering, 2002.
[15] S.T. Lie et.al. Model and mesh generation of cracked tubular Y-joints, Engineering Fracture Mechanics, 70 (2003) 161–184.
[16] G.I. Barenblatt, Scaling Phenomena In Fatigue And Fracture, Lawrence Berkeley National Laboratory, DECEMBER 2004.
[17] J. POLAK And P. ZEZULKA, Short crack growth and fatigue life in austenitic-ferritic duplex stainless steel, Fatigue Fracture Engineering Material Structural, 28 (2005) 923–935.
[18] N. Pugno et.al. A generalized Paris’ law for fatigue crack growth, Journal of the Mechanics and Physics of Solids, 54 (2006) 1333–1349.
[19] M. Balda, Identification of low cycle fatigue parameters, Applied and Computational Mechanics, 3 (2009) 259–266.
[20] M.M. Alam et.al. The influence of surface geometry and topography on the fatigue cracking behaviour of laser hybrid welded eccentric fillet joints, Applied Surface Science 256 (2010) 1936–1945.
[21] Alfredo S. Ribeiro et.al. Evolution of Fatigue History, 21st Brazilian Congress of Mechanical Engineering, 24-28, (2011).
[22] Abdelkader Boulenouar et.al. “Fe Model for Linear-Elastic Mixed Mode Loading: Estimation of SIFS And Crack Propagation”, Journal of Theoretical and Applied Mechanics, Vol. 52, No. 2, pp. 373-383, 2014.
[23] M.A. Mohamed et.al. Finite Element-Based Fatigue Life Prediction of a Load carrying Cruciform Joint, Journal of Mechanical Engineering and Sciences, 8 (2015) 1414-1425.
[24] R. Citarella et.al., Coupled FEM-DBEM Simulation Of 3D Crack Growth Under Fatigue Load Spectrum, 21st European Conference on Fracture, 21 (2016) 20-24.
[25] Greg Thorwald, Analysis of 3D Cracks in an Arbitrary Geometry with Weld Residual Stress, Structural Reliability Technology.