An Experimental Study for Surface Roughness Effect on SS 316L by Copper Electrode in Biomedical Fabrication Machined using EDM
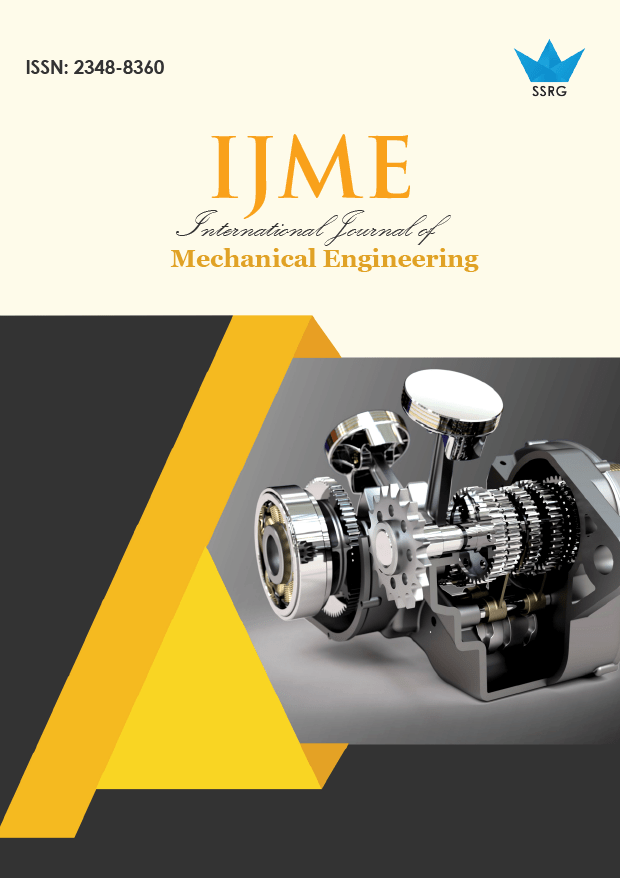
International Journal of Mechanical Engineering |
© 2022 by SSRG - IJME Journal |
Volume 9 Issue 4 |
Year of Publication : 2022 |
Authors : Mohammed Imran, M.A. Saloda, B.L. Salvi, Chitranjan Agarwal, S. Jindal |
How to Cite?
Mohammed Imran, M.A. Saloda, B.L. Salvi, Chitranjan Agarwal, S. Jindal, "An Experimental Study for Surface Roughness Effect on SS 316L by Copper Electrode in Biomedical Fabrication Machined using EDM," SSRG International Journal of Mechanical Engineering, vol. 9, no. 4, pp. 11-17, 2022. Crossref, https://doi.org/10.14445/23488360/IJME-V9I4P102
Abstract:
Hydrophobic surfaces are actively studied across a wide range of applications in different industries. Now in the biomedical arena, these surfaces play a major role as substrates to control protein absorption, bacterial growth, and cellular interaction and provide a better platform for drug delivery devices. Researchers have used various methods to generate hydrophobicity on metallic surfaces which are naturally hydrophilic. Surface texture plays an important role in generating hydrophobic surfaces; these textures are fabricated by non-conventional electric discharge machining (EDM) on a metallic surface. In this work, the authors are analyzing the effects of various EDM operating parameters such as discharge current, pulse on time, pulse off time, and voltage for measuring surface roughness (SR) and contact angle (CA) on stainless steel 316 L (SS 316L). The machinability of SS 316L is investigated using a copper electrode having a 16 mm diameter to achieve the high surface roughness value. The results are observed using the surface roughness tester SJ216. The copper electrode in biomedical hydrophobic surfaces is treated as an antibacterial coating to reduce infections. The copper electrode at a high current intensity gives a high SR value. Surface roughness values are obtained from 7.47µm to 13.81µm, which shows the better roughness value for hydrophobic nature SS 316L after EDM
Keywords:
EDM, Biomedical implants, SS 316L, Electrode, Surface texture, Hydrophobic.
References:
[1] U. Ashok kumar, P. Laxminarayana, and N. Aravindan, “Study of Surface Morphology on Micro machined Surfaces of AISI 316 by Die Sinker EDM,” Materials Today: Proceedings, vol. 4, no. 2, pp. 1285–1292, 2017.
[CrossRef] [Google Scholar] [Publisher Link]
[2] S. Jithin et al., “Analysis of Electrical Discharge Texturing Using Different Electrode Materials,” Advances in Materials and Processing Technologies, vol. 4, no. 3, pp. 466–479, 2018.
[CrossRef] [Google Scholar] [Publisher Link]
[3] Ahsan Ali Khan et al., “Relationship of Surface Roughness with Current and Voltage during Wire EDM,” Journal of Applied Sciences, vol. 6, no. 10, pp. 2317-2320, 2006.
[CrossRef] [Google Scholar] [Publisher Link]
[4] J. Strasky, M. Janecek, and P. Harcuba, “Electric Discharge Machining of Ti-6Al-4V Alloy for Biomedical Use,” WDS'11 Proceedings of Contributed Papers, Part III, pp. 127–131, 2011.
[Google Scholar] [Publisher Link]
[5] Jai Hindus et al., “Experimental Investigations on Electrical Discharge Machining of SS 316L,” International Journal on Mechanical Engineering and Robotics (IJMER), vol. 1, no. 2, pp. 2321–5747, 2013.
[Publisher Link]
[6] Safian Sharif et al., “Experimental Study of Electrical Discharge Machine (Die Sinking) on Stainless Steel 316L Using Design of Experiment,” Procedia Manufacturing, vol. 2, pp. 147–152, 2015.
[CrossRef] [Google Scholar] [Publisher Link]
[7] M. Bigerelle, K. Anselme, B. Noel, I. Ruderman, P. Hardouin, A. Iost, Biomaterials. , pp. 1563–1577, 2022. [8] A. Mahajan, and S. S. Sidhu, “Surface Modification of Metallic Biomaterials for Enhanced Functionality a Review,” Materials Technology, vol. 33, no. 2, pp. 93-105, 2018.
[CrossRef] [Google Scholar] [Publisher Link]
[9] S. Jithin, Upendra V. Bhandarkar, and Suhas S. Joshi, “Analytical Simulation of Random Textures Generated in Electrical Discharge Texturing,” Journal of Manufacturing Science Engineering, vol. 139, no. 11, pp. 1–12, 2017.
[CrossRef] [Google Scholar] [Publisher Link]
[10] A. Torres, C. J. Luis, and I. Puertas, “EDM Machinability and Surface Roughness Analysis of TiB2 using Copper Electrodes,” Journal of Alloys and Compounds, vol. 690, pp. 337–347, 2017.
[CrossRef] [Google Scholar] [Publisher Link]
[11] W. M. Wang, and K. P. Rajurkar, “Improvement of EDM Performance with Advanced Monitoring and Control Systems,” Journal of Manufacturing Science Engineering, vol. 119(4B), pp. 770-78, 1997.
[CrossRef] [Google Scholar] [Publisher Link]
[12] Kushendarsyah Saptaji et al., “Machining of Biocompatible Materials a Review,” The International Journal of Advanced Manufacturing Technology, vol. 97, no. 5, pp. 2255-2292, 2018.
[CrossRef] [Google Scholar] [Publisher Link]
[13] S. Jithin et al., “Analysis of Electrical Discharge Texturing Using Different Electrode Materials,” Advances in Materials and Processing Technologies, vol. 4, no. 3, pp. 466–479, 2018.
[CrossRef] [Google Scholar] [Publisher Link]
[14] Quanshui Zheng, and Cunjing Lü, “Size Effects of Surface Roughness to Superhydrophobicity,” Procedia IUTAM, vol. 10, pp. 462–475, 2014.
[CrossRef] [Google Scholar] [Publisher Link]
[15] A. Arslan et al., “Surface Texture Manufacturing Techniques and Tribological Effect of Surface Texturing on Cutting Tool Performance a Review,” Critical Reviews in Solid State and Materials Science, vol. 41, no. 6, () pp. 447–81, 2016.
[CrossRef] [Google Scholar] [Publisher Link]
[16] M. Peters et al., “Titanium Alloys for Aerospace Applications,” Advanced Engineering Materials, vol. 5, no. 6, pp. 419-427, 2003.
[CrossRef] [Google Scholar] [Publisher Link]
[17] Yanling Tian, Xianping Liu, and Houjun Qi, “Generation of Stainless Steel Super Hydrophobic Surfaces Using WEDM Technique,” Ninth International Symposium on Precision Engineering Measurement and Instrumentation, vol. 9446, 2015.
[CrossRef] [Google Scholar] [Publisher Link]
[18] Alaa M. Ubaid et al., “Optimization of Electro Discharge Machining Process Parameters with Fuzzy Logic for Stainless Steel 304 (ASTM A340),” Journal of Manufacturing Science and Engineering, vol. 140, no. 1, pp. 1-13, 2018.
[CrossRef] [Google Scholar] [Publisher Link]
[19] Katarzyna Peta et al., “Contact Angle Analysis of Surface Topographies Created by Electric Discharge Machining,” Tribology International, vol. 163, pp. 107-139, 2021.
[CrossRef] [Google Scholar] [Publisher Link]
[20] Shankar Singh, S. Maheshwari, and P. C. Pandey, “Some Investigations Into the Electric Discharge Machining of Hardened Tool Steel Using Different Electrode Materials,” Journal of Materials Processing Technology, vol. 149, no. 1-3, pp. 272–277, 2004.
[CrossRef] [Google Scholar] [Publisher Link]
[21] D. Amrish Raj, and T. Senthilvelan, “Empirical Modeling and Optimization of Process Parameters of Machining Titanium Alloy by Wire- EDM using RSM,” Materials today Proceedings, vol. 2, pp. 4-5, 2015.
[CrossRef] [Google Scholar] [Publisher Link]
[22] MINITAB Student Version. (2017). [Online]. Available:
https://www.kruss-scientific.com/products/drop-shape/dsa100/drop-shape-analyzer dsa100/?gclid=Cj0KCQiAnNXiBRCoARIsAJe_1cpXreV97J1ZsHKDeUY_LcfKgf6s1NlsPApS-uO37iIiqJSsn4thiOkaAroMEALw_wcB