Failure of Frontline Tubes of a Superheater Bundle in a Waste Heat Recovery Boiler Due to Thermal Fatigue Stresses and Solution to Eliminate them
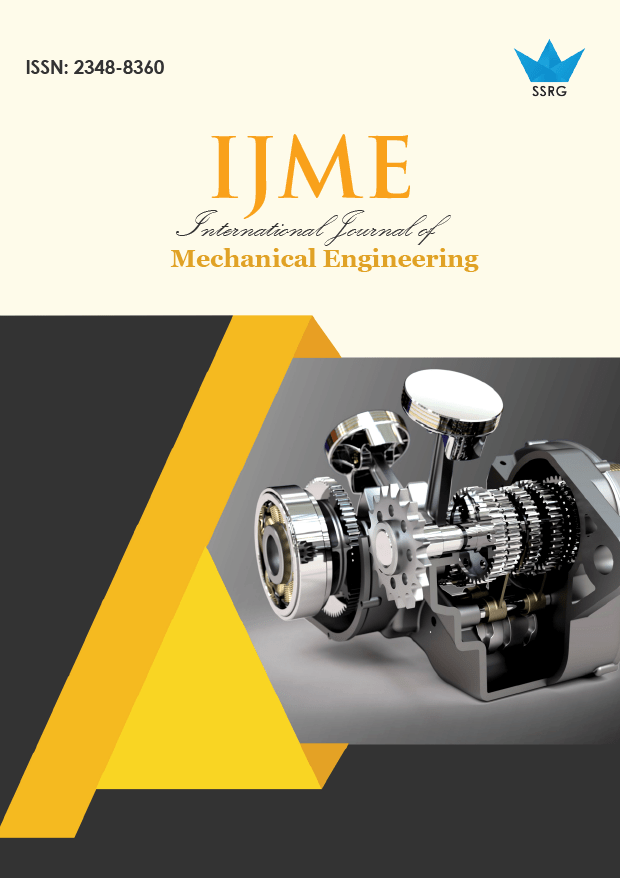
International Journal of Mechanical Engineering |
© 2022 by SSRG - IJME Journal |
Volume 9 Issue 12 |
Year of Publication : 2022 |
Authors : Ajay Mehta |
How to Cite?
Ajay Mehta, "Failure of Frontline Tubes of a Superheater Bundle in a Waste Heat Recovery Boiler Due to Thermal Fatigue Stresses and Solution to Eliminate them," SSRG International Journal of Mechanical Engineering, vol. 9, no. 12, pp. 7-13, 2022. Crossref, https://doi.org/10.14445/23488360/IJME-V9I12P102
Abstract:
Waste Heat Recovery Boiler is designed to recover the escaping heat of a combustion process through heat transfer between hot flue gases and banks of tube bundles (Figure 1). The frontline tubes of the superheater bundle of a Waste Heat Recovery Boiler (WHRB) face high-temperature flue gases entering the boiler, raising the steam temperature to the designed superheated level before the steam escapes through the outlet header. It is reported that the frontline tubes of the superheater bundle frequently fail during operations. The metallurgical failure analysis of the frontline tube reported that the tubes developed fatigue cracks at the joint where they weld to the couplings connecting the outlet header of the superheater bundle. On reviewing the reports of metallurgical failure analysis, the author observes that the cracks develop only on the front side of the tube periphery and that incoming hot gases do not heat the tubes at the same uniform temperature around its periphery resulting in a differential thermal expansion between the front and rear side of same tubes causing the tubes to bow (a bimetallic strip effect). The author observes that the design and construction of the superheater bundle tube do not allow free movement in the front line of tubes to accommodate changes in tube length due to differential thermal expansion, causing the bowing effect on the tube resulting in severe fissures at the weld joint with outlet header coupling. The paper recommends engineering solution to the design by introducing a tube-coil (loop) between the superheater tube and header coupling to absorb the thermal expansion such that the thermal fatigue stresses are minimised/eliminated, preventing premature tube failure at the weld joint with the steam header above. The bowed tube generates moments at the coil joint, which then transfers the same moment to the header coupling joint. The stresses due to differential thermal expansion are widespread and very high in magnitude. They are normally present in every boiler design. The above-described solution can be applied to varieties of waste heat recovery boilers.
Keywords:
WHRB- Waste heat recovery boiler, Superheater- Bundle of tubes in a boiler which comes in contact of hot gases at highest temperature (upstream) to heat up the steam converting it into superheated state, Bowing- Bending of the tube due to differential temperature between front and rear of the same tube causing uneven length expansion, Fissures-concentration of cracks due to excessive stresses either compressive or tensile.
References:
[1] Victor Rogers, “Heat Recovery Steam Generators: Vulnerable to Failure,” Engineering 360, 2016.
[Google Scholar]
[2] M. Pronobis, W. Wojnar, and J. Czepelak, “Influence of Non-Uniform Heating on the Stresses in Tubes of Superheaters in Boilers,” Forsch Ingenieurwes, vol. 69, pp. 29–37, 2004.
[CrossRef] [Google Scholar] [Publisher Link]
[3] H. Othman, J. Purbolaksono, and B. Ahmad, “Failure Investigation on Deformed Superheater Tubes,” Engineering Failure Analysis, vol. 16, no. 1, pp. 329-339, 2009.
[CrossRef] [Google Scholar] [Publisher Link]
[4] NYR-PW132964-01 6-2 SH2755 Tube Bundle Failure Analysis.
[5] NYR-PW122734-01 Bundle Tube Failure Analysis.
[6] Ajay Mehta, "Thermal Fatigue Stresses in Reinforcement Pads and Shell Wall Below, in an Un-Insulated Shut Down Vessel Operating at High Temperature," SSRG International Journal of Mechanical Engineering, vol. 6, no. 8, pp. 16-25, 2019.
[CrossRef] [Publisher Link]
[7] Henry H Bednar, Pressure Vessel Design Handbook, Second Edition, pp. 3-4 and 241–256, 1986.
[8] Warren C Young, and Richard G Budynas, Roark’s Formulas for Stress and Strain, Seventh Edition, McGraw-Hill.
[9] ASME B31.3 Process Piping Flexibility in Process Piping, 2016.
[10] AS 1228-2006 Pressure Equipment – Boilers, Superheater Tubes.
[11] API RP 571: Damage Mechanisms Affecting Fixed Equipment in the Refining Industry, API (American Petroleum Institute), 2003. [Online]. Available: https://mycommittees.api.org/standards/cre/sci/Shared%20Documents/2019%20API%20Conferences/2019%20Fall/571_e3%20PP2.pdf
[12] API 579-1/ASME FFS-1- Fitness-for-Service, API (American Petroleum Institute), 2007.
[13] MA143802-1-1 - Temperature Monitoring of HSRG Superheater Tubes.
[14] ASME II PART D-2017 Table 1A.
[15] DIN 17175 ST35.8 High Pressure Boiler Tubes Mechanical Properties