Reduction Analysis of Welding Defects using Lean Six Sigma and DMAIC Application – A Case Study
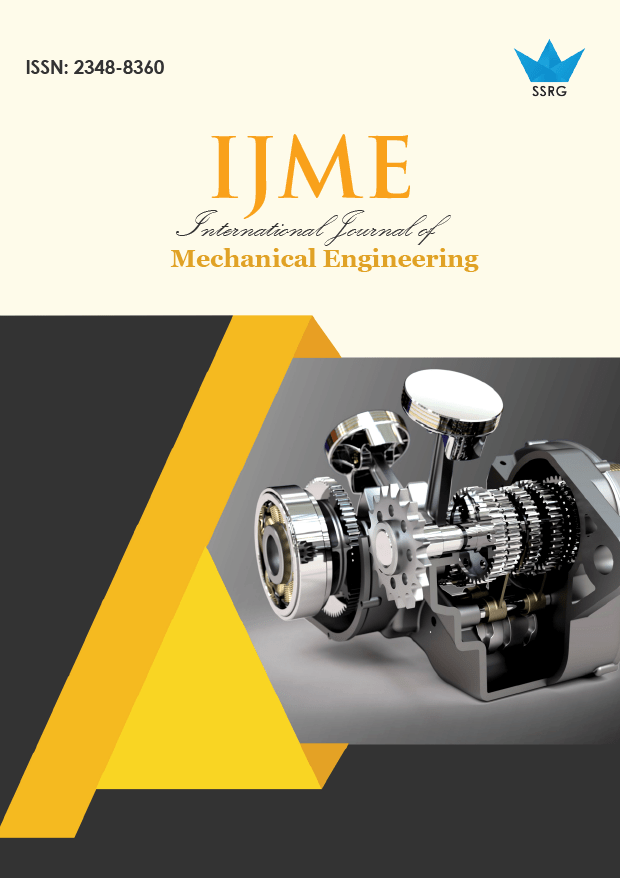
International Journal of Mechanical Engineering |
© 2023 by SSRG - IJME Journal |
Volume 10 Issue 4 |
Year of Publication : 2023 |
Authors : S. Nallusamy, P.S. Chakraborty, G.V. Punna Rao |
How to Cite?
S. Nallusamy, P.S. Chakraborty, G.V. Punna Rao, "Reduction Analysis of Welding Defects using Lean Six Sigma and DMAIC Application – A Case Study," SSRG International Journal of Mechanical Engineering, vol. 10, no. 4, pp. 13-20, 2023. Crossref, https://doi.org/10.14445/23488360/IJME-V10I4P103
Abstract:
This research aims to investigate the process of gas tungsten arc welding commonly used in the submersible pump industry. The weld abandons is a noteworthy concern prompting revamp, greater expenses, and in this manner, influencing the conveyance plan of the activity. This research article succeeds in deploying the six sigma Define, Measure, Analyze, Improve, and Control (DMAIC) structure to improve the action features and assess and eradicate different sources in an operational system referred to in the industry. To implement the fundamental methods in various tasks, best usage instigation of availabilities, variabilities moderations, and maintaining the consistent output six sigma tool is adopted. The root cause analysis of Tungsten Inert Gas (TIG) welding defects and static tools to recognize the potential causes for controlling and supporting a few changes with proposals are specified. The current level of deformity was found to be 15% in stator rejections for the period of one month. After implementing the proposal, the overall defect was expected to reduce.
Keywords:
Welding, Non-Destructive test, Lean six sigma, DMAIC, Stator.
References:
[1] G. V. S. S. Sharma, and P. Srinivasa Rao, “A DMAIC Approach for Process Capability Improvement an Engine Crankshaft Manufacturing Process,” Journal of Industrial Engineering International, vol. 10, pp. 65-76, 2014.
[CrossRef] [Google Scholar] [Publisher Link]
[2] Manish Bhargava, and Sanjay Gaur, “Process Improvement Using Six-Sigma (DMAIC Process) in Bearing Manufacturing Industry: A Case Study,” IOP Conference Series: Materials Science and Engineering, vol. 1017, 2021.
[Google Scholar] [Publisher Link]
[3] Sandeep Kumar Dwivedi, Manish Vishwakarma, and Akhilesh Soni, “Advances and Researches on Non Destructive Testing: A Review,” Materials Today: Proceedings, vol. 5, no. 2, pp. 3690-3698, 2018.
[CrossRef] [Google Scholar] [Publisher Link]
[4] Masoud Shaloo et al., “A Review of Non-Destructive Testing (NDT) Techniques for Defect Detection: Application to Fusion Welding and Future Wire Arc Additive Manufacturing Processes,” Materials, vol. 15, no. 10, p. 3697, 2022.
[CrossRef] [Google Scholar] [Publisher Link]
[5] Anirudh Sampath Madhvacharyula et al., “In Situ Detection of Welding Defects: A Review,” Weld World, vol. 66, pp. 611-628, 2022.
[CrossRef] [Google Scholar] [Publisher Link]
[6] Ana Lopez et al., “Non-Destructive Testing Application of Radiography and Ultrasound for Wire and Arc Additive Manufacturing,” Additive Manufacturing, vol. 21, pp. 298–306, 2018.
[CrossRef] [Google Scholar] [Publisher Link]
[7] S. Nallusamy, “Analysis of Welding Properties in FSW Aluminium 6351 Alloy Plates Added with Silicon Carbide Particles,” International Journal of Engineering Research in Africa, vol. 21, pp. 110-117, 2015.
[CrossRef] [Google Scholar] [Publisher Link]
[8] Yongfeng Song et al., “Nondestructive Testing of Additively Manufactured Material Based on Ultrasonic Scattering Measurement,” Measurement, vol. 118, pp. 105-112, 2018.
[CrossRef] [Google Scholar] [Publisher Link]
[9] Jéssica Galdino de Freitas, and Helder Gomes Costa, “Impacts of Lean Six Sigma over Organizational Sustainability: A Systematic Literature Review on Scopus Base,” International Journal of Lean Six Sigma, vol. 8, no. 1, pp. 89-108.
[CrossRef] [Google Scholar] [Publisher Link]
[10] S. Nallusamy, “A Proposed Model for Sustaining Quality Assurance Using Tqm Practices in Small and Medium Scale Industries,” International Journal of Engineering Research in Africa, vol. 22, pp. 184-190, 2016.
[CrossRef] [Google Scholar] [Publisher Link]
[11] Araman, H., and Saleh, “A Case Study on Implementing Lean Six Sigma: Dmaic Methodology in Aluminum Profiles Extrusion Process,” The TQM Journal, vol. 35, no. 2, pp. 337-365, 2023.
[CrossRef] [Google Scholar] [Publisher Link]
[12] Ilesanmi Daniyan et al., “Application of Lean Six Sigma Methodology Using Dmaic Approach for the Improvement of Bogie Assembly Process in the Railcar Industry,” Heliyon, vol. 8, no. 3, p. E09043, 2022.
[CrossRef] [Google Scholar] [Publisher Link]
[13] Pratima Mishra, and Rajiv Kumar Sharma, “A Hybrid Framework Based on Sipoc and Six Sigma DMAIC for Improving Process Dimensions in Supply Chain Network,” International Journal of Quality & Reliability Management, vol. 31, no. 5, pp. 522-546, 2014.
[CrossRef] [Google Scholar] [Publisher Link]
[14] Rao G V P, S. Nallusamy, and M. Rajaram Narayanan, “Augmentation of Production Level Using Different Lean Approaches in Medium Scale Manufacturing Industries,” International Journal of Mechanical Engineering and Technology, vol. 8, no. 12, pp. 360- 372, 2017.
[Google Scholar] [Publisher Link]
[15] John B, and Kadadevaramath, “Improving the Resolution Time Performance of An Application Support Process Using Six Sigma Methodology,” International Journal of Lean Six Sigma, vol. 11, no. 4, pp. 663–686, 2020.
[CrossRef] [Google Scholar] [Publisher Link]
[16] E. V. Gijo, Raniprasad Palod, and Jiju Antony, “Lean Six Sigma Approach in an Indian Auto Ancillary Conglomerate: A Case Study,” Production Planning & Control, vol. 29, no. 9, pp. 761-772, 2018.
[CrossRef] [Google Scholar] [Publisher Link]