Analysis and Predict Surface Roughness in the Hard Turning of Hardened SKD11 Steel using Mixed Ceramic Inserts
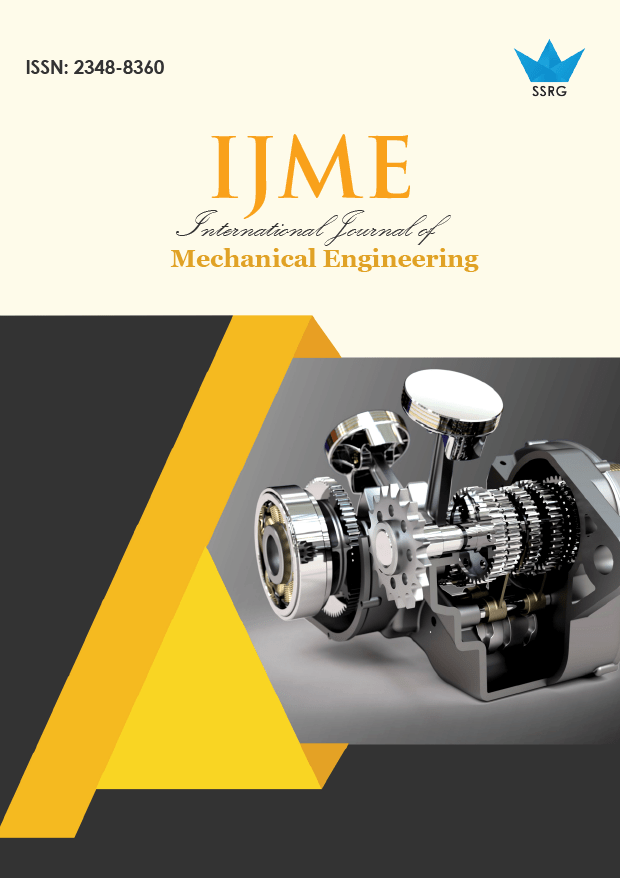
International Journal of Mechanical Engineering |
© 2023 by SSRG - IJME Journal |
Volume 10 Issue 5 |
Year of Publication : 2023 |
Authors : Minh Tuan Ngo |
How to Cite?
Minh Tuan Ngo, "Analysis and Predict Surface Roughness in the Hard Turning of Hardened SKD11 Steel using Mixed Ceramic Inserts," SSRG International Journal of Mechanical Engineering, vol. 10, no. 5, pp. 1-7, 2023. Crossref, https://doi.org/10.14445/23488360/IJME-V10I5P101
Abstract:
SKD11 steel is a high-carbon and high-chromium alloy tool steel used to do cold work or hot work dressing dies, sides of rollers, and screw heading molds. The hardened SKD11 steel has a high hardness of 58-62HRC, good wear resistance, and good toughness. Hard turning is an important process because manufacturers continually seek ways to manufacture their parts with lower cost, higher quality, rapid setups, lower investment, and smaller tooling inventory while eliminating non-valueadded activities where Surface roughness is an important parameter determining the accuracy and quality of parts. In this paper, an analysis of the surface roughness of SKD11 steel in hard turning with mixed ceramic inserts is performed based on variables like cutting speed, feed, and depth of cut. The feed rate is the most significant parameter affecting the surface roughness in the machining process. Prediction of surface roughness considering the simultaneous effect of cutting parameters is very difficult. Here, a mathematical model is developed based on the simultaneous effect of depth, cutting speed, and feed rate. Moreover, the developed model is validated using different sets of cutting conditions and found in close agreement with experimental results.
Keywords:
Ceramic insert, Hard turning, SKD11, Surface roughness.
References:
[1] Graham T. Smith, Cutting Tool Technology: Industrial Handbook, 1st ed. Springer-Verlag London, 2008.
[CrossRef] [Google Scholar] [Publisher Link]
[2] J. Paulo Davim, Machining of Hard Materials, London: Springer-Verlag London, 2011.
[CrossRef] [Google Scholar] [Publisher Link]
[3] Junfeng Yuan, German S. Fox-Rabinovich, Stephen C. Veldhuis, “Control of Tribofilm Formation in Dry Machining of Hardened AISI D2 Steel by Tuning the Cutting Speed,” Wear, vol. 402–403, pp. 30–37, 2018.
[CrossRef] [Google Scholar] [Publisher Link]
[4] Sarmad Ali Khan et al., “Experimental Investigations on Wiper Inserts’ Edge Preparation, Workpiece Hardness and Operating Parameters in Hard Turning of AISI D2 Steel,” Journal of Manufacturing Processes vol. 34, pp 187–196, 2018.
[CrossRef] [Google Scholar] [Publisher Link]
[5] V.N. Gaitonde et al., “Machinability Investigations in Hard Turning of AISI D2 Cold Work Tool Steel with Conventional and Wiper Ceramic Inserts,” International Journal of Refractory Metals and Hard Materials, vol. 27, no. 4, pp. 754–763, 2009.
[CrossRef] [Google Scholar] [Publisher Link]
[6] Tugrul Ozel et al., “Modelling of Surface Finish and Tool Flank Wear in Turning of AISI D2 Steel with Ceramic Wiper Inserts,” Journal of Materials Processing Technology, vol. 189, no. 1-3, pp. 192–198, 2007.
[CrossRef] [Google Scholar] [Publisher Link]
[7] Muhammad Aftab Ahmad et al., “Influence of Wiper and Conventional Inserts at Profile Geometry During Turning of D2 Tool Steel, Engineering Technology Open Access Journal, vol. 1, no. 5, 2018.
[CrossRef] [Google Scholar] [Publisher Link]
[8] Yogesh Raut, and Amit Bahekar "Optimization of Parameters to Reduce the Surface Roughness in Face Milling Operation on Cast Iron Work piece Applying Taguchi Method,” International Journal of Engineering Trends and Technology, vol. 68, no. 1, pp. 9-13, 2020.
[CrossRef] [Google Scholar] [Publisher Link]
[9] Ramón Quiza, Luis Figueira, and J. Paulo Davim, “Comparing Statistical Models and Artificial Neural Networks on Predicting the Tool Wear in Hard Machining D2 AISI Steel,” The International Journal of Advanced Manufacturing Technology, vol. 37, pp. 641–648, 2008.
[CrossRef] [Google Scholar] [Publisher Link]
[10] V. N. Gaitonde et al., “Analysis of Machinability During Hard Turning of Cold Work Tool Steel (Type: AISI D2), Materials and Manufacturing Processes, vol. 24, no. 12, pp. 1373–1382, 2009.
[CrossRef] [Google Scholar] [Publisher Link]
[11] Sarmad Ali Khan et al., “High Feed Turning of AISI D2 Tool Steel Using Multi Radii Tool Inserts: Tool Life, Material Removed and Workpiece Surface Integrity Evaluation,” Materials and Manufacturing Processes, vol. 32, no. 6, 2017.
[CrossRef] [Google Scholar] [Publisher Link]
[12] Noor Dhani, Ahmad Gasruddin, and Laswar Gombilo Bitu, “Effect of Aggregate Abrasion Value on Marshall Parameters in Mixed LGA (Lawele Granular Asphalt),” International Journal of Engineering Trends and Technology, vol. 71, no. 2, pp. 259-267, 2023.
[CrossRef] [Publisher Link]
[13] Dilbag Singh, and P. Venkateswara Rao, “A Surface Roughness Prediction Model for Hard Turning Process,” The International Journal of Advanced Manufacturing Technology, vol. 32, pp 1115–1124, 2007.
[CrossRef] [Google Scholar] [Publisher Link]
[14] Hamdi Aouici et al., “Analysis of Surface Roughness and Cutting Force Components in Hard Turning with CBN Tool: Prediction Model and Cutting Conditions Optimization,” Measurement, vol. 45, no. 3, pp. 344-353, 2012.
[CrossRef] [Google Scholar] [Publisher Link]
[15] Tuğrul Özel, and Yiğit Karpat, “Predictive Modeling of Surface Roughness and Tool Wear in Hard Turning Using Regression and Neural Networks,” International Journal of Machine Tools and Manufacture, vol. 45, no. 4-5, pp. 467- 479, 2005.
[CrossRef] [Google Scholar] [Publisher Link]
[16] İlhan Asiltürk, and Mehmet Çunkaş, “Modeling and Prediction of Surface Roughness in Turning Operations Using Artificial Neural Network and Multiple Regression Method,” Expert Systems with Applications, vol. 38, no. 5, pp. 5826-5832, 2011.
[CrossRef] [Google Scholar] [Publisher Link]