The Effect of Design Parameters on the Discharge of a Transparent Cylinder Single-Acting Reciprocating Pump
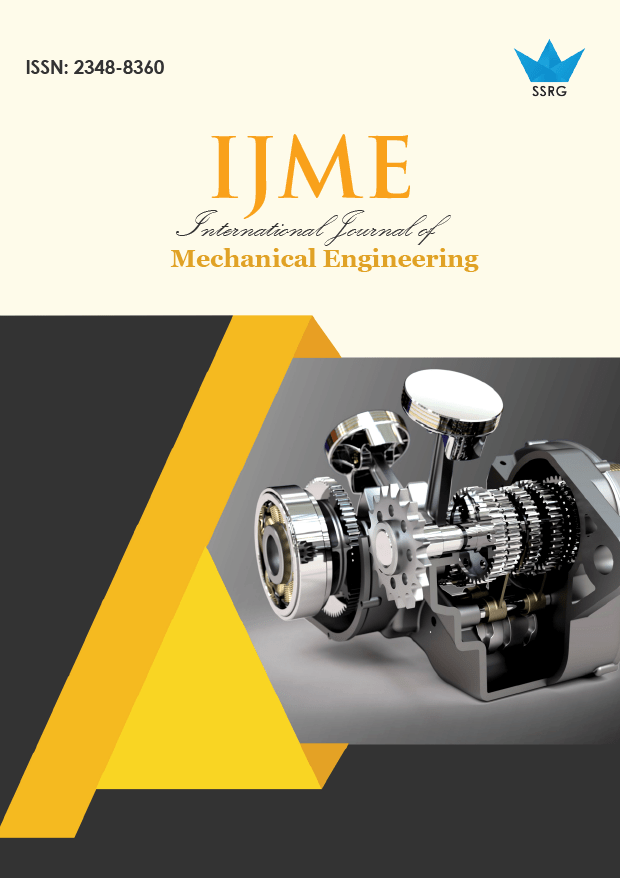
International Journal of Mechanical Engineering |
© 2023 by SSRG - IJME Journal |
Volume 10 Issue 6 |
Year of Publication : 2023 |
Authors : Ekong Godwin I., Essien Promise J., Udom Evans J. |
How to Cite?
Ekong Godwin I., Essien Promise J., Udom Evans J., "The Effect of Design Parameters on the Discharge of a Transparent Cylinder Single-Acting Reciprocating Pump," SSRG International Journal of Mechanical Engineering, vol. 10, no. 6, pp. 20-28, 2023. Crossref, https://doi.org/10.14445/23488360/IJME-V10I6P104
Abstract:
This project presents the Effect of Design Parameters on the Discharge of a Single-acting Reciprocating Pump for use in the Mechanical Engineering laboratory of the Akwa Ibom State University (AKSU). The project provides a portable positive displacement pump for demonstrating the movement of fluids in the laboratory. The component consists of atransparent piston-cylinder assembly, suction pipe, delivery pipe, suction valve, delivery valve, crank, and connecting rod mechanism powered by an electric motor. During the operation of this apparatus, there will be visual movement of the piston during the suction and delivery stroke per each cycle. The pump piston has a diameter of 0.100 m, a stroke length of 0.305 m, and a designed speed of 20 r.p.m. The suction head and delivery are 0.762 m and 1.585 m, respectively. The practical operations were performed, and data was collected. The reciprocating pump principles were applied for the pressure head analysis during the suction and delivery strokes. The parametric analysis carried out includes the acceleration head during the suction stroke at the beginning of the delivery stroke and the pressure head in the middle of the stroke and at the end of the suction stroke. Analyses were performed, and the results indicate a pump discharge of delivery.0008 m3/s with work done by the pump of 18.40 Nm/sec. Further studies were performed for four different piston diameters, stroke lengths, and speeds. The results were used in the computation analysis for the discharge and work done by the pump.
Keywords:
Pressure, Suction, Delivery, Single-acting, Reciprocating, Pump.
References:
[1] I. Ekong Godwin, and J. Ekanem Ubong, “Performance Analysis of a Single-acting Reciprocating Pump,” Quest Journals Journal of Research in Mechanical Engineering, vol. 9, no. 3, pp. 7-18, 2023.
[Google Scholar] [Publisher Link]
[2] R.K. Rajput, A Textbook of Fluid Mechanics and Hydraulic Machines, S. Chand and Company Ltd. 2004.
[Google Scholar]
[3] Z.G. Han, and Qing Jian Liu, “Dynamic Analysis on Crank-Slider Mechanism of Reciprocating Pump,” Materials Science Forum, vol. 697-698, pp. 676–80, 2011.
[CrossRef] [Google Scholar] [Publisher Link]
[4] Yang TieNing, “Performance Study on Linear Motor Reciprocating Pump,” Master’s Thesis, China University of Petroleum, 2009.
[Google Scholar] [Publisher Link]
[5] S. H. D. Joffe, “The Effect of Operating Parameters on the Wear Behaviour of Disc Poppet Valves in Reciprocating Slurry Pumps,” Master Thesis, University of Cape Town, 1988.
[Google Scholar] [Publisher Link]
[6] Donald D. Dudenhoeffer, “Failure Analysis of a Repairable System: The Case Study of a Cam-Driven Reciprocating Pump,” Thesis, Naval Postgraduate School Monterey, 1994.
[Google Scholar] [Publisher Link]
[7] Parag Akarte et al., “Solar Based Reciprocating Pump,” International Journal for Research in Applied Science and Engineering Technology, vol. 10, no. 5, pp. 4492–4497, 2022.
[CrossRef] [Publisher Link]
[8] Trinath Sahoo, “Cavitation in Reciprocating Pumps,” World Pumps, vol. 2006, no. 472, pp. 24–27, 2006.
[CrossRef] [Google Scholar] [Publisher Link]
[9] Meng Li Wu, and Jia Bin Yuan, “Analysis of the Pulsation in Aircraft Deicing System,” Applied Mechanics and Materials, vol. 251, pp. 104–108, 2012.
[CrossRef] [Google Scholar] [Publisher Link]
[10] J. D. Burton, and T. D. Short, “Induced Flow Reciprocating Pumps Part 1,” Institution of Mechanical Engineers, Part A: Journal of Power and Energy, vol. 213, no. 5, pp. 363–373, 1999.
[CrossRef] [Google Scholar] [Publisher Link]
[11] Gerhard Vetter, and Schweinfurther Friedrich, “Pressure Pulsations in the Piping of Reciprocating Pumps,” Chemical Engineering & Technology, vol. 10, no. 1, pp. 262–271, 1987.
[CrossRef] [Google Scholar] [Publisher Link]
[12] D.N. Johnston, “Numerical Modelling of Reciprocating Pumps with Self-Acting Valves,” Institution of Mechanical Engineers, Part I: Journal of Systems and Control Engineering, vol. 205, no. 2, pp. 87–96, 1991.
[CrossRef] [Google Scholar] [Publisher Link]
[13] Godwin Ita Ekong, Christopher A. Long, and Peter R. N. Childs, “Clearance Control Concept in Gas Turbine H.P. Compressors,” ASME, International Mechanical Engineering Congress and Exposition, pp. 433-441, 2013.
[CrossRef] [Google Scholar] [Publisher Link]
[14] Godwin Ita Ekong, Christopher A. Long, and Peter R. N. Childs, “The Effect of Heat Transfer Coefficient Increase on Tip Clearance Control in H.P. Compressors in Gas Turbine Engine,” ASME, International Mechanical Engineering Congress and Exposition, 2014.
[CrossRef] [Google Scholar] [Publisher Link]
[15] Jeffrey J. Rudolf et al., “Optimum Design Parameters for Reciprocating Pumps used in Natural Gas Wells,” Journal of Energy Resources Technology, vol. 127, no. 4, pp. 285–292, 2005.
[CrossRef] [Google Scholar] [Publisher Link]
[16] Adam Menkara et al., “Applications of a Novel Reciprocating Positive Displacement Pump in the Simulation of Pulsatile Arterial Blood Flow,” PLOS ONE, vol. 17, no. 12, 2022.
[CrossRef] [Google Scholar] [Publisher Link]
[17] Hashimoto, Hiroyuki, Hirokuni Hiyama, and Rokuro Sato, “Development of Prototype Pump Using a Vibrating Pipe with a Valve,” ASME, Journal of Fluids Engineering, vol. 116, no. 4, pp. 741–745, 1994.
[CrossRef] [Google Scholar] [Publisher Link]
[18] Ekong I. Godwin, Ibibom N. Emmanue, and Bassey U. Isaiah, “Performance Analysis of a Single-acting Reciprocating Compressor Using Thermodynamic Concepts,” International Journal of Engineering Science Invention, vol. 9, no. 5, pp. 20-31, 2020.
[Google Scholar] [Publisher Link]
[19] Godwin I. Ekong, “The Effect of the Design Parameters on Mass Flow Measurement and Control in an Orifice Plate Flow RIG,” Quest Journals, Journal of Research in Mechanical Engineering, vol. 6, no. 1, pp. 1-12, 2020.
[Google Scholar] [Publisher Link]
[20] Godwin I. Ekong, “Parametric Effect on the Discharge of Venturimeter Flow RIG,” Quest Journal, Journal of Research in Mechanical Engineering, vol. 8, no. 7, pp. 34-44, 2022.
[Google Scholar] [Publisher Link]
[21] Godwin I. Ekong, Christopher A. Long, and Peter R. N. Childs, “Application of Creativity Tools to Gas Turbine Engine Compressor Clearance Control,” ASME, International Mechanical Engineering Congress and Exposition, 2014.
[CrossRef] [Google Scholar] [Publisher Link]
[22] Godwin I. Ekong, “Application of Creative Techniques in Effective Management of a Power Generation Plant,” Journal of the European TRIZ Association, vol. 1, pp. 43–50, 2014.
[Google Scholar] [Publisher Link]