Enhancement of Productivity and Efficiency through a Service Model with Lean Service Tools - Case Study
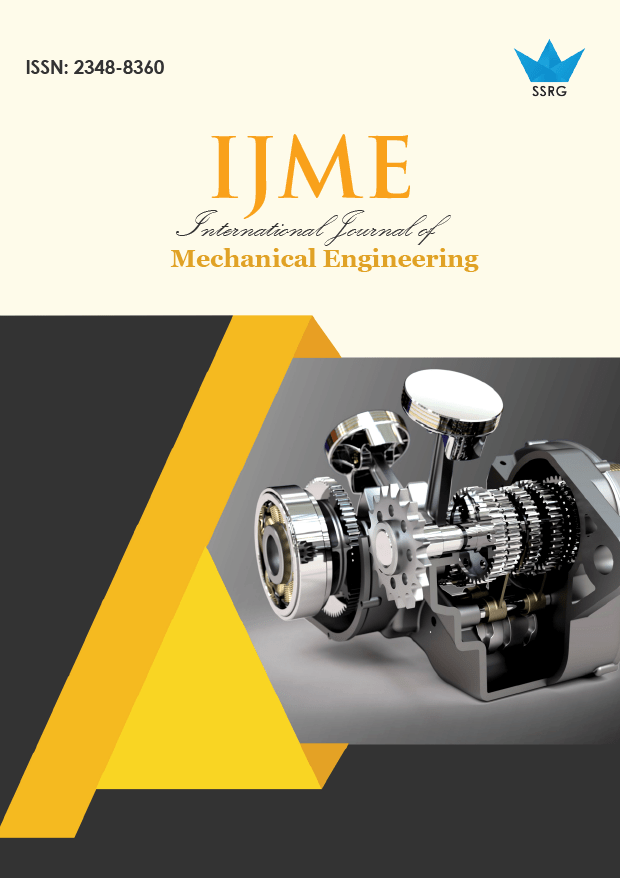
International Journal of Mechanical Engineering |
© 2023 by SSRG - IJME Journal |
Volume 10 Issue 9 |
Year of Publication : 2023 |
Authors : Carmen Alondra-Torres Millones, Juan Carlos Quiroz-Flores, S. Nallusamy |
How to Cite?
Carmen Alondra-Torres Millones, Juan Carlos Quiroz-Flores, S. Nallusamy, "Enhancement of Productivity and Efficiency through a Service Model with Lean Service Tools - Case Study," SSRG International Journal of Mechanical Engineering, vol. 10, no. 9, pp. 18-30, 2023. Crossref, https://doi.org/10.14445/23488360/IJME-V10I9P102
Abstract:
This research aims to enhance productivity in the preparation and presentation of hamburgers at an artisanal category restaurant. The goal is to increase productivity and efficiency while reducing reprocessing rates during practice. This article introduces an innovative operational model that integrates Facility Layout Design (FLD), Standardized Work (STW), and autonomous maintenance under the Plan-Do-Check-Act (PDCA) cycle framework to address the suboptimal utilization of workstations and the current layout, as well as the high error rates in the preparation process and the lack of preventive maintenance for the machines involved in the operation. The model is divided into four phases. The first phase consists of diagnosing the initial situation of the company. The second phase encompasses the implementation of Lean Service and FLD tools. Subsequently, a 12-week implementation phase took place. Finally, the implemented improvements were assessed, and pre-and post-implementation indicators were compared. Statistical validation of the improved indicators was performed using Minitab Statistics V21 software. The results confirmed an 18% increase in productivity and a 27% increase in efficiency. Additionally, reprocessing was reduced by 50%. This article serves as a reference for better decision-making for managers and entrepreneurs within the artisanal food cluster seeking to enhance productivity and efficiency and reduce reprocessing rates in similar small and Medium-Sized Enterprises (MSE).
Keywords:
PDCA, Facility Layout Design, Standardized Work, Autonomous maintenance, Productivity, Rework.
References:
[1] National Institute of Statistics and Information Technology, 2022. [Online]. Available: https://www.inei.gob.pe/estadisticas/indicetematico/economia/
[2] Alex Onaga-Nishimura et al., “Service Management Model Based on Lean Service and Systematic Layout Planning for the Improvement of Customer Satisfaction in an SME in the Restaurant Sector in Peru,” 8 th International Conference on Industrial and Business Engineering, pp. 242-249, 2022.
[CrossRef] [Google Scholar] [Publisher Link]
[3] Enrique Ruiz Zúñiga et al., “A Simulation-Based Optimization Methodology for Facility Layout Design in Manufacturing,” IEEE Access, vol. 8, pp. 163818-163828, 2020.
[CrossRef] [Google Scholar] [Publisher Link]
[4] Reza Zanjirani Farahani, Maryam SteadieSeifi, and Nasrin Asgari, “Multiple Criteria Facility Location Problems: A survey,” Applied Mathematical Modelling, vol. 34, no. 7, pp. 1689-1709, 2010.
[CrossRef] [Google Scholar] [Publisher Link]
[5] Parveen Sharma, and Sandeep Singhal, “Implementation of Fuzzy TOPSIS Methodology in Selection of Procedural Approach for Facility Layout Planning,” The International Journal of Advanced Manufacturing Technology, vol. 88, pp. 1485-1493, 2017.
[CrossRef] [Google Scholar] [Publisher Link]
[6] Mateusz Kikolski, and Chien-Ho Ko, “Facility Layout Design-Review of Current Research Directions,” Engineering Management in Production and Services, vol. 10, no. 3, pp. 70-79, 2018.
[CrossRef] [Google Scholar] [Publisher Link]
[7] Mehmet Savsar, and Aminah Aldehaim, “Analysis and Improvement of Facility Layout in a Furniture Factory: A Case Application,” International Conference on Industrial Engineering and Operations Management, pp. 436-447, 2020.
[Google Scholar] [Publisher Link]
[8] Arturo Realyvásquez-Vargas et al., “Work Standardization and Anthropometric Workstation Design as an Integrated Approach to Sustainable Workplaces in the Manufacturing Industry,” Sustainability, vol. 12, no. 9, pp. 1-22, 2020.
[CrossRef] [Google Scholar] [Publisher Link]
[9] Sudhir Chaurey et al., “A Review on the Identification of Total Productive Maintenance Critical Success Factors for Effective Implementation in The Manufacturing Sector,” Journal of Quality in Maintenance Engineering, vol. 29, no. 1, pp. 114-135, 2023.
[CrossRef] [Google Scholar] [Publisher Link]
[10] Lalit K. Toke, and Shyamkumar D. Kalpande, “Total Quality Management in Small and Medium Enterprises: An Overview in Indian Context,” Quality Management Journal, vol. 27, no. 3, pp. 159-175, 2020.
[CrossRef] [Google Scholar] [Publisher Link]
[11] Aseem Acharya et al., “Plant Effectiveness Improvement of Overall Equipment Effectiveness using Autonomous Maintenance Training: A Case Study,” International Journal of Mechanical and Production Engineering Research and Development, vol. 9, no. 1, pp. 103-112, 2019.
[Google Scholar] [Publisher Link]
[12] Qing Hu et al., “Knowledge Management in Consultancy-Involved Process Improvement Projects: Cases from Chinese SMEs,” Production Planning & Control, vol. 30, no. 10-12, pp. 866-880, 2019.
[CrossRef] [Google Scholar] [Publisher Link]
[13] Marcello Braglia, Roberto Gabbrielli, and Leonardo Marrazzini, “Rolling Kanban, A New Visual Tool to Schedule Family Batch Manufacturing Processes with Kanban,” International Journal of Production Research, vol. 58, no.13, pp. 3998-4014, 2020.
[CrossRef] [Google Scholar] [Publisher Link]
[14] Anchal Patil, and P.V.M. Rao, “Sonographer Ergonomics: Assessment and Workplace Redesign,” International Conference on Industrial Engineering and Operations Management, Malaysia, pp. 3403-3411, 2016.
[Google Scholar] [Publisher Link]
[15] Puvanasvaran A.P., Ab. Hamid M.N.H., and Yoong S.S., “Cycle Time Reduction for Coil Setup Process through Standard Work: Case Study in Ceramic Industry,” ARPN Journal of Engineering and Applied Sciences, vol. 13, no. 1, pp. 210-220, 2018.
[Google Scholar] [Publisher Link]
[16] M.L. Emiliani, “Standardized Work for Executive Leadership,” Leadership & Organization Development Journal, vol. 29, no. 1, pp. 24- 46, 2008.
[CrossRef] [Google Scholar] [Publisher Link]
[17] Raed EL-Khalil, and Hussein Zeaiter, “Improving Automotive Efficiency through Lean Management Tools: A Case Study,” International Journal of Industrial and Manufacturing Engineering, vol. 9, no. 1, pp. 314-321, 2015.
[CrossRef] [Google Scholar] [Publisher Link]
[18] Ruslana Hubková, and Felipe Martinez, “Work Standardization and Waste Reduction in Automobile Exhausts Manufacturing,” 12th International Days of Statistics and Economics, pp. 580-589, 2018.
[Google Scholar] [Publisher Link]
[19] Gun Jea Yu Minjae Park, and Ki Hoon Hong, “A Strategy Perspective on Total Quality Management,” Total Quality Management & Business Excellence, vol. 31, no. 1-2, pp. 68-81, 2020.
[CrossRef] [Google Scholar] [Publisher Link]
[20] Muhammad Danish Mohamad Rosni et al., “Solving Production Bottleneck through Developed Define-Measure-Delegate-ImplementControl in Solving Production Bottleneck,” International Journal of Six Sigma and Competitive Advantage, vol. 14, no.2, pp. 209-226, 2022.
[CrossRef] [Google Scholar] [Publisher Link]
[21] Albari Antunes, and Evandro Eduardo, “Adopting PDCA to Loss Reduction: A Case Study in a Food Industry in Southern Brazil,” International Journal for Quality Research, vol. 13, no. 2, pp. 335-348, 2019.
[Google Scholar]
[22] Silvio Aguiar, Integration of Quality Tools into PDCA and the Six Sigma Program, 2002.
[Google Scholar]
[23] Luís Fernando Peixoto da Cunha, “The PDCA Method as a Tool for Continuous Improvement of Processes and Support for the Elaboration of Strategic Planning of Companies,” Revista Uniabeu, vol. 6, no. 14, pp. 366-384, 2013.
[Google Scholar]
[24] Cristina Werkema, Creating Lean Six Sigma Culture, 2nd ed., Elsevier, 2013.
[Google Scholar]
[25] Mohammad Shahin et al., “Integration of Lean Practices and Industry 4.0 Technologies: Smart Manufacturing for Next-Generation Enterprises,” International Journal of Advanced Manufacturing Technology, vol. 107, pp. 2927-2936, 2020.
[CrossRef] [Google Scholar] [Publisher Link]