Comparative Analysis of Turning Parameters in Dry and Wet Machining of Haynes 25 Alloy Using L9 Taguchi Approach
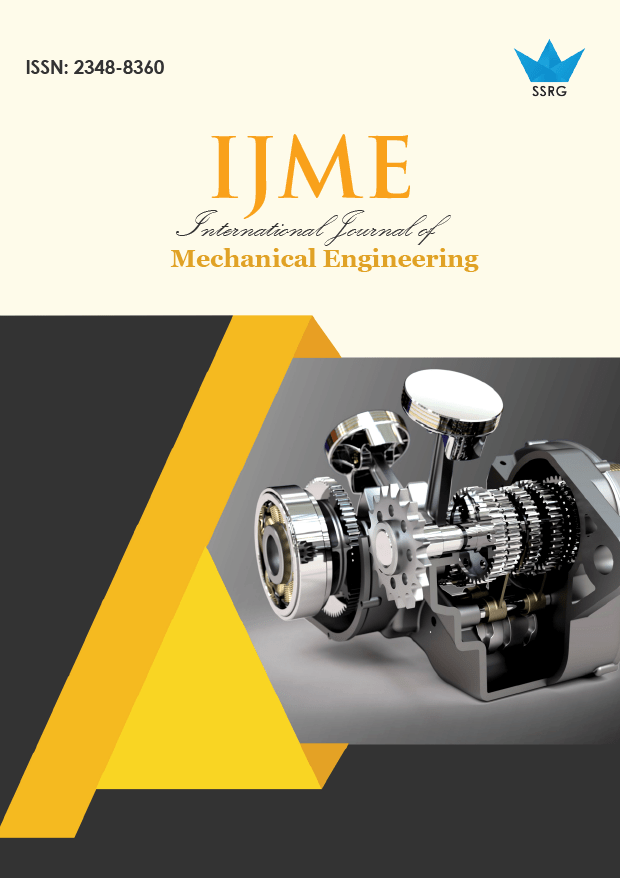
International Journal of Mechanical Engineering |
© 2024 by SSRG - IJME Journal |
Volume 11 Issue 3 |
Year of Publication : 2024 |
Authors : Amit Tajne, Hardik Ramani, Yogesh G. Joshi |
How to Cite?
Amit Tajne, Hardik Ramani, Yogesh G. Joshi, "Comparative Analysis of Turning Parameters in Dry and Wet Machining of Haynes 25 Alloy Using L9 Taguchi Approach," SSRG International Journal of Mechanical Engineering, vol. 11, no. 3, pp. 11-16, 2024. Crossref, https://doi.org/10.14445/23488360/IJME-V11I3P102
Abstract:
This study examines the impact of the machining environment, namely dry turning versus wet turning, on optimizing turning parameters for machining Haynes 25 alloy. The study utilizes the precise L9 Taguchi Methodology to investigate the critical parameters of cutting speed, depth of cut, and feed rate. The objective is to minimize tool wear and improve surface roughness under dry and wet conditions. The turning parameters, including cutting speed, depth of cut, and feed rate, are methodically adjusted. The cutting speeds are set at 500,1000,1500 rpm, the depth of cut at 0.6,1.2,1.8 mm, and the feed rates at 0.05, 0.1 and 0.15 mm/rev. In the dry turning experiments, there is no application of external coolant, but in the wet turning studies, a specific type of coolant is injected into the cutting zone. Both environments are closely scrutinized to ensure precise and verifiable results. Regression analysis is performed separately for dry and wet turning situations, resulting in predictive equations for tool wear and surface roughness in each environment. The ideal parameters for dry turning are determined as (insert optimal conditions for dry turning), whereas wet turning demonstrates superior outcomes under (insert optimal conditions for wet turning). Under the observed ideal parameters, the wet turning environment continually exceeds dry turning by significantly reducing tool wear and improving surface roughness.
Keywords:
Haynes 25, Surface roughness, Tool wear, Dry turning, Wet turning.
References:
[1] Haynes International - Haynes®25 Alloy, 2024. [Online]. Available: https://www.haynesintl.com/en/datasheet/haynes-25-alloy/
[2] David A. Stephenson, and John S. Agapiou, Metal Cutting Theory and Practice, 3rd ed., CRC Press, Boca Raton, Florida, 2016.
[Google Scholar] [Publisher Link]
[3] S.L. Semiatin, J.J. Jonas, and G.R. Halford, ASM Handbook, Volume 14B: Metal Working: Sheet Forming, ASM International, Materials Park, USA, 2006.
[4] W. Brain Rowe et al., Tribology of Abrasive Machining Processes, 1st ed., William Andrew, USA, 2004.
[Google Scholar] [Publisher Link]
[5] Genichi Taguchi, System of Experimental Design: Engineering Methods to Optimize Quality and Minimize Costs, 1st ed., UNIPUB/Kraus International Publications, 1987.
[Publisher Link]
[6] Genichi Taguchi, and S. Konishi, Taguchi Methods: Orthogonal Arrays and Linear Graphs: Tools for Quality Engineering, ASI Press, 1987.
[Google Scholar]
[7] Phillip J. Ross, Taguchi Techniques for Quality Engineering: Loss Function, Orthogonal Experiments, Parameter and Tolerance Design, McGraw-Hill Education, 1988.
[Google Scholar] [Publisher Link]
[8] Atul B. Andhare, K. Kannathasan, and Manoj Funde, “Effect of Machining Parameters on Surface Roughness and Tool Flank Wear in Turning of Haynes 25 Alloy,” Advances in Mechanical Engineering, pp. 679-686, 2020.
[CrossRef] [Google Scholar] [Publisher Link]
[9] Murat Sarıkaya, and Abdulkadir Gullu, “Examining of Tool Wear in Ryogenic Machining of Cobalt-Based Haynes 25 Superalloy,” International Journal of Chemical, Molecular, Nuclear, Materials and Metallurgical Engineering, vol. 9, no. 8, pp. 852-856, 2015.
[CrossRef] [Google Scholar] [Publisher Link]
[10] Murat Sarıkaya, Volkan Yılmaz, and Abdulkadir Gullu, “Analysis of Cutting Parameters and Cooling/Lubrication Methods for Sustainable Machining in the Turning of Haynes 25 Superalloy,” Journal of Cleaner Production, vol. 133, pp. 172-181, 2016.
[CrossRef] [Google Scholar] [Publisher Link]
[11] Senol Sirin, “Investigation of the Performance of Cermet Tools in the Turning of Haynes 25 Superalloy under Gaseous N2 and Hybrid Nanofluid Cutting Environments,” Journal of Manufacturing Processes, vol. 76, pp. 428-443, 2022.
[CrossRef] [Google Scholar] [Publisher Link]
[12] Murat Sarıkaya et al., “Performance Evaluation of Whisker-Reinforced Ceramic Tools under Nano-Sized Solid Lubricants Assisted MQL Turning of Co-Based Haynes 25 Superalloy,” Ceramics International, vol. 47, no. 11, pp. 15542-15560, 2021.
[CrossRef] [Google Scholar] [Publisher Link]
[13] B. Satyanarayana, G. Ranga Janardhana, and D. Hanumantha Rao, “Optimized High-Speed Turning on Inconel 718 Using Taguchi Method Based Grey Relational Analysis,” Indian Journal of Engineering and Materials Sciences (IJEMS), vol. 20, no. 4, pp. 269-275, 2013.
[Google Scholar] [Publisher Link]
[14] Sitki Akincioglu, Hasan Gokkaya, and Ilyas Uygur, “The Effects of Cryogenic-Treated Carbide Tools on Tool Wear and Surface Roughness of Turning of Hastelloy C22 Based on Taguchi Method,” International Journal of Advanced Manufacturing Technology, vol. 82, pp. 303-314, 2016.
[CrossRef] [Google Scholar] [Publisher Link]