An Experimental Analysis of 3D Printed Poly-Lactic Acid (PLA) Specimens as Per ASTM Standard Using Taguchi and Analysis of Variance (ANOVA) Approach
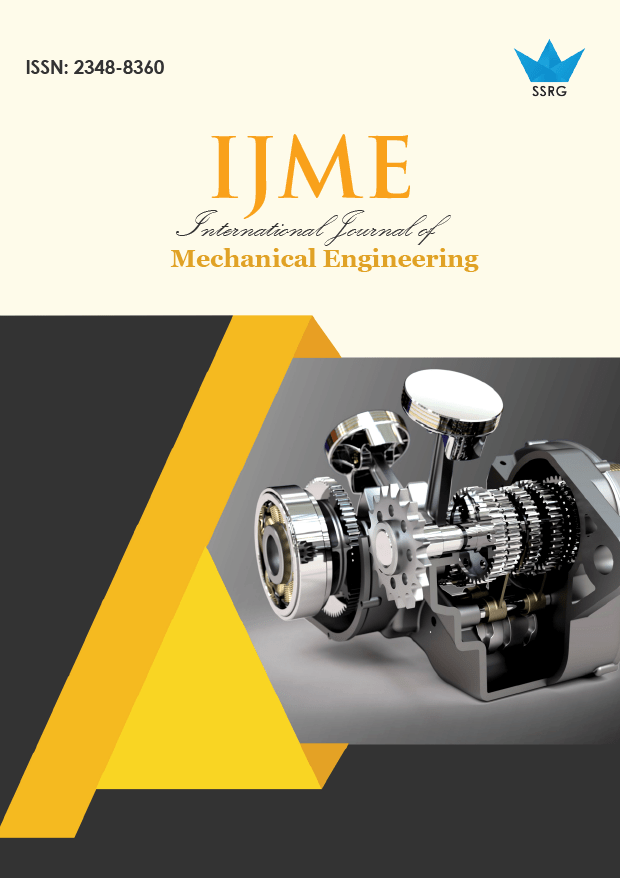
International Journal of Mechanical Engineering |
© 2024 by SSRG - IJME Journal |
Volume 11 Issue 3 |
Year of Publication : 2024 |
Authors : Manoj Kumar Poddar, Saroj Kumar Sarangi |
How to Cite?
Manoj Kumar Poddar, Saroj Kumar Sarangi, "An Experimental Analysis of 3D Printed Poly-Lactic Acid (PLA) Specimens as Per ASTM Standard Using Taguchi and Analysis of Variance (ANOVA) Approach," SSRG International Journal of Mechanical Engineering, vol. 11, no. 3, pp. 27-39, 2024. Crossref, https://doi.org/10.14445/23488360/IJME-V11I3P104
Abstract:
Fused Deposition Modeling (FDM) is a fast-growing 3D printing technique because of its capacity to produce functional components with complicated shapes. The mechanical characteristics of 3D printed components are influenced by many process factors of FDM 3D printers. The present research examined the optimum settings for FDM 3D printers to use with Polylactic Acid (PLA) materials. The printed PLA specimens were subjected to tensile and flexural testing in accordance with ASTM standards to assess their mechanical qualities. The experiments were carefully planned using the Taguchi method of an L9 orthogonal array with four factors at three levels each. Infill pattern, printing speed, printing temperature, and layer thickness were selected as four factors to optimize. Regression modeling, Analysis of Variance (ANOVA), and the Taguchi S/N ratio are used to analyze the data from tensile and flexural testing. The findings suggest that the mechanical strength is significantly influenced by the interactions among Infill patterns, printing speed, layer thickness, and printing temperature.
Keywords:
FDM, Polylactic Acid (PLA), 3D printing, Taguchi method, DOE, ANOVA.
References:
[1] Marzio Grasso et al., “Effect of Temperature on the Mechanical Properties of 3D-printed PLA Tensile Specimens,” Rapid Prototyping Journal, vol. 24, no. 8, pp. 1337-1346, 2018.
[CrossRef] [Google Scholar] [Publisher Link]
[2] Dafydd O. Visscher et al., “Cartilage Tissue Engineering: Preventing Tissue Scaffold Contraction Using a 3D-Printed Polymeric Cage,” Tissue Engineering Part C: Methods, vol. 22, no. 6, pp. 573-584, 2016.
[CrossRef] [Google Scholar] [Publisher Link]
[3] Pshtiwan Shakor et al., “Modified 3D printed Powder to Cement-Based Material and Mechanical Properties of Cement Scaffold Used in 3D Printing,” Construction and Building Materials, vol. 138, pp. 398-409, 2017.
[CrossRef] [Google Scholar] [Publisher Link]
[4] Özgür Keleş, Caleb Wayne Blevins, and Keith J. Bowman, “Effect of Build Orientation on the Mechanical Reliability of 3D Printed ABS,” Rapid Prototyping Journal, vol. 23, no. 2, pp. 320-328, 2017.
[CrossRef] [Google Scholar] [Publisher Link]
[5] Wenzheng Wu et al., “Influence of Layer Thickness and Raster Angle on the Mechanical Properties of 3D-Printed PEEK and a Comparative Mechanical Study between PEEK and ABS,” Materials, vol. 8, no. 9, pp. 5834-5846, 2015.
[CrossRef] [Google Scholar] [Publisher Link]
[6] Fuda Ning et al., “Additive Manufacturing of Carbon Fiber-Reinforced Plastic Composites Using Fused Deposition Modeling: Effects of Process Parameters on Tensile Properties,” Journal of Composites Materials, vol. 51, no. 4, pp. 369-378, 2016.
[CrossRef] [Google Scholar] [Publisher Link]
[7] Antonio Lanzotti et al., “The Impact of Process Parameters on Mechanical Properties of Parts Fabricated in PLA with an Open-Source 3D Printer,” Rapid Prototyping Journal, vol. 21, no. 5, pp. 604-617, 2015.
[CrossRef] [Google Scholar] [Publisher Link]
[8] Farnoosh Ebrahimi, and Hossein Ramezani Dana, “Poly Lactic Acid (PLA) Polymers: from Properties to Biomedical Applications,” International Journal of Polymeric Materials and Polymeric Biomaterials, vol. 71, no. 15, pp. 1117-1130, 2021.
[CrossRef] [Google Scholar] [Publisher Link]
[9] Betty Tyler et al., “Polylactic Acid (PLA) Controlled Delivery Carriers for Biomedical Applications,” Advanced Drug Delivery Reviews, vol. 107, pp. 163-175, 2016.
[CrossRef] [Google Scholar] [Publisher Link]
[10] Ümit Çevik, and Menderes Kam, “A Review Study on Mechanical Properties of Obtained Products by FDM Method and Metal/Polymer Composite Filament Production,” Journal of Nanomaterials, vol. 2020, pp. 1-9, 2020.
[CrossRef] [Google Scholar] [Publisher Link]
[11] Vincent DeStefano, Salaar Khan, and Alonzo Tabada, “Applications of PLA in Modern Medicine,” Engineered Regeneration, vol. 1, pp. 76–87, 2020.
[CrossRef] [Google Scholar] [Publisher Link]
[12] F.S. Senatov et al., “Mechanical Properties and Shape Memory Effect of 3D-Printed PLA-based Porous Scaffolds,” Journal of the Mechanical Behavior of Biomedical Materials, vol. 57, pp. 139-148, 2016.
[CrossRef] [Google Scholar] [Publisher Link]
[13] Ala’aldin Alafaghani, and Ala Qattawi, “Investigating the Effect of Fused Deposition Modeling Processing Parameters Using Taguchi Design of Experiment Method,” Journal of Manufacturing Processes, vol. 36, pp. 164–174, 2018.
[CrossRef] [Google Scholar] [Publisher Link]
[14] Isksioui Hamza, El Gharad Abdellah, and Oubrek Mohamed, “Experimental Optimization of Fused Deposition Modeling Process Parameters: A Taguchi Process Approach for Dimension and Tolerance Control,” Proceedings of the 2nd International Conference on Industrial Engineering and Operations Management, Paris, France, pp. 2992–2993, 2018.
[CrossRef] [Google Scholar] [Publisher Link]
[15] Jackson Pasini Mairing, “The Effect of Advance Statistics Learning Integrated Minitab and Excel with Teaching Teams,” International Journal of Instruction, vol. 13, no. 2, pp. 139-150, 2020.
[CrossRef] [Google Scholar] [Publisher Link]
[16] Mohd Nazri Ahmad et al., “Application of Taguchi Method to Optimize the Parameter of Fused Deposition Modeling (FDM) Using Oil Palm Fiber Reinforced Thermoplastic Composites,” Polymers, vol. 14, no. 11, pp. 1-15, 2022.
[CrossRef] [Google Scholar] [Publisher Link]
[17] Manu Srivastava, and Sandeep Rathee, “Optimisation of FDM Process Parameters by Taguchi Method for Imparting Customised Properties to Components,” Virtual and Physical Prototyping, vol. 13, no. 3, pp. 203-210, 2018.
[CrossRef] [Google Scholar] [Publisher Link]
[18] J.M. Chacon, “Additive Manufacturing of PLA Structures Using Fused Deposition Modelling: Effect of Process Parameters on Mechanical Properties and Their Optimal Selection,” Materials & Design, vol. 124, pp. 143-157, 2017.
[CrossRef] [Google Scholar] [Publisher Link]
[19] V. Durga Prasada Rao, P. Rajiv, and V. Navya Geethika, “Effect of Fused Deposition Modelling (FDM) Process Parameters on Tensile Strength of Carbon Fibre PLA,” Materials Today: Proceedings, vol. 18, pp. 2012-2018, 2019.
[CrossRef] [Google Scholar] [Publisher Link]
[20] Marzio Grasso et al., “Effect of Temperature on the Mechanical Properties of 3D-printed PLA Tensile Specimens,” Rapid Prototyping Journal, vol. 24, no. 8, pp. 1337-1346, 2018.
[CrossRef] [Google Scholar] [Publisher Link]
[21] Roberto Spina, “Performance Analysis of Colored PLA Products with a Fused Filament Fabrication Process,” Polymers, vol. 11, no. 12, pp. 1-16, 2019.
[CrossRef] [Google Scholar] [Publisher Link]
[22] Yu Zhao, Yuansong Chen, and Yongjun Zhou, “Novel Mechanical Models of Tensile Strength And Elastic Property of FDM AM PLA Materials: Experimental and Theoretical Analyses,” Materials and Design, vol. 181, 2019.
[CrossRef] [Google Scholar] [Publisher Link]
[23] S.K. Dhinesh et al., “Study on Flexural and Tensile Behavior of PLA, ABS and PLA-ABS Materials,” Materials Today: Proceedings, vol. 45, pp. 1175-1180, 2021.
[CrossRef] [Google Scholar] [Publisher Link]
[24] J.A. Travieso-Rodriguez et al., “Comparative Study of the Flexural Properties of ABS, PLA and a PLA–Wood Composite Manufactured through Fused Filament Fabrication,” Rapid Prototyping Journal, vol. 27, no. 1, pp. 81-92, 2020.
[CrossRef] [Google Scholar] [Publisher Link]
[25] M. Damous Zandi et al., “Experimental Analysis of Manufacturing Parameters’ Effect on the Flexural Properties of Wood-PLA Composite Parts Built Through FFF,” The International Journal of Advanced Manufacturing Technology, vol. 106, pp. 3985-3998, 2020.
[CrossRef] [Google Scholar] [Publisher Link]
[26] K.N. Gunasekaran et al., “Investigation of Mechanical Properties of PLA Printed Materials Under Varying Infill Density,” Materials Today: Proceedings, vol. 45, pp. 1849-1856, 2021.
[CrossRef] [Google Scholar] [Publisher Link]
[27] Salvatore Brischetto, and Roberto Torre, “Tensile and Compressive Behavior in the Experimental Tests for PLA Specimens Produced via Fused Deposition Modelling Technique,” Journal of Composites Science, vol. 4, no. 140, pp. 1-25, 2020.
[CrossRef] [Google Scholar] [Publisher Link]
[28] Tianyun Yao et al., “Tensile Failure Strength and Separation Angle of FDM 3D Printing PLA Material: Experimental and Theoretical Analyses,” Composites Part B: Engineering, vol. 188, 2020.
[CrossRef] [Google Scholar] [Publisher Link]
[29] Meena Pant et al., “Wear Assessment of 3–D Printed Parts of PLA (polylactic acid) Using Taguchi design and Artificial Neural Network (ANN) Technique,” Materials Research Express, vol. 7, no. 11, 2020.
[CrossRef] [Google Scholar] [Publisher Link]
[30] M. Samykano, “Mechanical Property and Prediction Model for FDM-3D Printed Polylactic Acid (PLA),” Arabian Journal for Science and Engineering, vol. 46, pp. 7875-7892, 2021.
[CrossRef] [Google Scholar] [Publisher Link]
[31] Lionel Aufray, Pierre-André Gouge, and Lamine Hattali, “Design of Experiment Analysis on Tensile Properties of PLA Samples Produced by Fused Flament Fabrication,” The International Journal of Advanced Manufacturing Technology, vol. 118, pp. 4123–4137, 2022.
[CrossRef] [Google Scholar] [Publisher Link]
[32] Adnan Rasheed et al., “Experimental Investigation and Taguchi Optimization of FDM Process Parameters for the Enhancement of Tensile Properties of Bi-Layered Printed PLA-ABS,” Materials Research Express, vol. 10, no. 9, 2023.
[CrossRef] [Google Scholar] [Publisher Link]
[33] S. Anand Kumar, and Yeole Shivraj Narayan, “Tensile Testing and Evaluation of 3D-Printed PLA Specimens as per ASTM D638 Type IV Standard,” Innovative Design, Analysis and Development Practices in Aerospace and Automotive Engineering (I-DAD 2018), Conference Paper, pp. 79–95, 2018.
[CrossRef] [Google Scholar] [Publisher Link]