An Approach for Narrowing the Method of Selection of Profile Shift Coefficient for A Given Helical Gear Pair
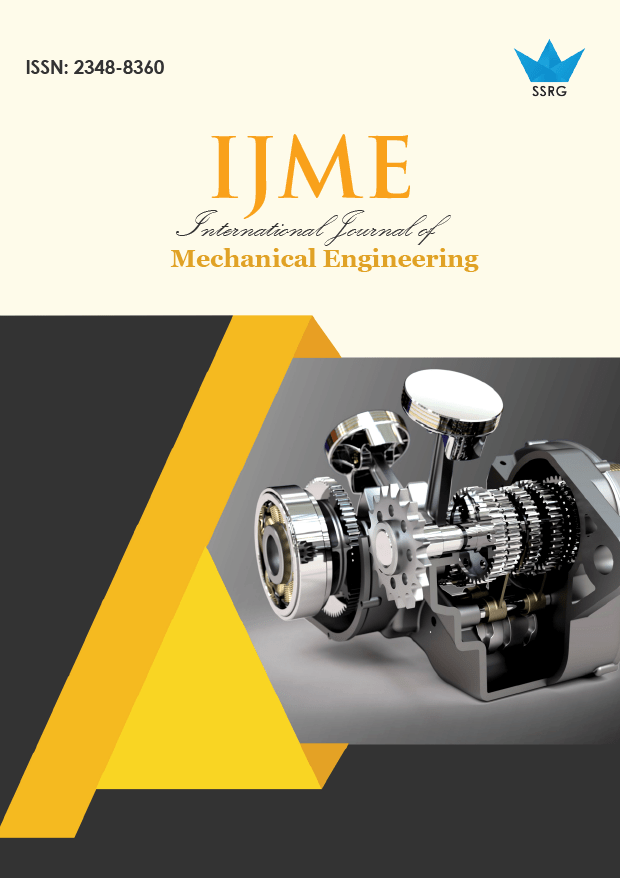
International Journal of Mechanical Engineering |
© 2024 by SSRG - IJME Journal |
Volume 11 Issue 5 |
Year of Publication : 2024 |
Authors : Kiran More, Ashutosh Kumar |
How to Cite?
Kiran More, Ashutosh Kumar, "An Approach for Narrowing the Method of Selection of Profile Shift Coefficient for A Given Helical Gear Pair," SSRG International Journal of Mechanical Engineering, vol. 11, no. 5, pp. 37-47, 2024. Crossref, https://doi.org/10.14445/23488360/IJME-V11I5P105
Abstract:
Profile shift or Addendum modification is provided in gear teeth to avoid undercut, improve strength and running properties or adjust the centre distance. Along with this, it is generally recommended for gears with a critical number of teeth, non-standard entre distance, obtain balances specific sliding or obtain reduction in sizes. However, there is no specific ready data that advises how to use it and what value can be opted. This research work is performed to investigate the effect of addendum modification on various parameters like contact ratio, tooth root strength, specific sliding, and undercutting. A pair of helical gears with 24 teeth and 97 teeth with 20-degree pressure angle and 13.4022-degree helix angle is considered for study purposes. The results are compared with the kissSoft data, and charts are prepared to establish the selection of addendum modification parameters for both gear and pinion. As an output of this research work, a graph is produced to help in narrowing the selection of profile shift coefficient with an excel tool for performing various functions. This work was specific to the sample case, whereas the same methodology can be implemented for other pairs of gears.
Keywords:
Addendum modification, KissSoft, Specific sliding, Undercut.
References:
[1] Shanmugasundaram Sankar, Maasanamuthu Sundar Raj, and Muthusamy Nataraj, “Profile Modification for Increasing the Tooth Strength in Spur Gear using CAD,” Scientific Research, vol. 2, no. 9, pp. 740-749, 2010.
[CrossRef] [Google Scholar] [Publisher Link]
[2] Philips D. Rockwell, “Profile Shift in External Parallel Axis Cylindrical Involute Gears,” Gear Technology, pp. 18-25, 2001.
[Google Scholar] [Publisher Link]
[3] Durmu Günay, Halil Özer, and Alpay Aydemir, “The Effects of Addendum Modification Coefficient on Tooth Stress of Spur Gears,” Mechanical and Computational Applications, vol. 1, no. 1, pp. 36-43, 1996.
[CrossRef] [Google Scholar] [Publisher Link]
[4] Gultekin Karadere, and Ilhan Yilmaz, “Investigation of the Effects of Profile Shift in Helical Gear Mechanisms with Analytical and Numerical Methods,” World Journal of Mechanics, vol. 8, no. 5, pp. 200-209, 2018.
[CrossRef] [Google Scholar] [Publisher Link]
[5] S. Baglioni, F. Cianetti, and L. Landi, “Influence of the Addendum Modification on Spur Gear Efficiency,” Mechanism and Machine Theory, vol. 49, no. 3, pp. 216-233, 2012.
[CrossRef] [Google Scholar] [Publisher Link]
[6] Zoltan Tomori, “An Optimal Choice of Profile Shift Coefficient for Spur Gears,” Machines, vol. 9, no. 6, pp. 1-13, 2021.
[CrossRef] [Google Scholar] [Publisher Link]
[7] Belarhzal Samya et al., “Analysis of Profile Shift Factor's Effect on Bending Stress of Spur Gears Using the Finite Element Method,” IEEE 6th International Conference on Optimization and Applications, Beni Mellal, Morocco, pp. 1-6, 2020.
[CrossRef] [Google Scholar] [Publisher Link]
[8] Michael Gebremariam et al., “Effect of Change of Contact Ratio on Contact Fatigue Stress of Involute Spur Gears,” International Journal of current Engineering and Technology, vol. 8, no. 3, pp. 719-731, 2018.
[CrossRef] [Google Scholar] [Publisher Link]
[9] Jinhai Wang et al., “Analytical Investigation of Profile Shifts on the Mesh Stiffness and Dynamic Characteristics of Spur Gears,” Mechanism and Machine Theory, vol. 167, pp. 1-18, 2022.
[CrossRef] [Google Scholar] [Publisher Link]
[10] A.R. Rajesh, Gonsalvis Joseph, and K.A. Venugopal, “Optimization of Profile Shift Co-Efficient for Highest Contact Ratio in Nonstandard Gearing,” IOP Conference Series: Materials Science and Engineering, Karnataka, India, vol. 1189, 2021.
[CrossRef] [Google Scholar] [Publisher Link]
[11] Ali Raad Hassan, “Pressure Angle and Profile Shift Factor Effects on the Natural Frequency of Spur Gear Tooth Design,” International Journal of Mechanical and Mechatronics Engineering, vol. 12, no. 1, pp. 58-64, 2018.
[Google Scholar] [Publisher Link]
[12] J.I. Pedrero, and M. Artés, “Approximate Equation for the Addendum Modification Factors for Tooth Gears with Balanced Specific Sliding,” Mechanism and Machine Theory, vol. 31, no. 7, pp. 925-935, 1996.
[CrossRef] [Google Scholar] [Publisher Link]
[13] J.I. Pedrero, M. Artés, and J.C. García-Prada, “Determination of the Addendum Modification Factors for Gears with Pre-Established Contact Ratio,” Mechanism and Machine Theory, vol. 31, no. 7, pp. 937-945, 1996.
[CrossRef] [Google Scholar] [Publisher Link]
[14] H.K. Sachidananda, K. Raghunandana, and Joseph Gonsalvis, “Sliding Velocity in Profile Corrected Gears,” Journal of Lubrication Science, vol. 29, no. 1, pp. 43-58, 2017.
[CrossRef] [Google Scholar] [Publisher Link]
[15] Hammoudi Abderazek et al., “A Differential Evolution Algorithm for Tooth Profile Optimization with Respect to Balancing Specific Sliding Coefficients of Involute Cylindrical Spur and Helical Gears,” Advances in Mechanical Engineering, vol. 7, no. 9, pp. 1-11, 2015.
[CrossRef] [Google Scholar] [Publisher Link]
[16] Damir T. Jelaska, Gears and Gear Drive, Wiley, 2012.
[Google Scholar] [Publisher Link]
[17] ISO 6336-1:1996(MAIN), Calculation of load capacity of spur and helical gears-Part 1: Basic Principles, Introduction and General Influence Factors. [Online]. Available : https://standards.iteh.ai/catalog/standards/iso/c8ec37d7-be92-48c2-857b-6b1bf4c66a2a/iso-6336-11996
[18] KISSOFT Reference Guide, 2020. [Online]. Available: https://www.scribd.com/document/518643688/Kisssoft-Release-2020-UserManual
[19] Q. Jane Wang, and Yip-Wah Chung, Encyclopaedia of Tribology, Springer, 2013.
[Publisher Link]
[20] ISO:6336-3, Calculation of Load Capacity of Spur and Helical Gears, 2019. [Online]. Available https://www.iso.org/standard/63822.html#:~:text=This%20document%20specifies%20the%20fundamental,mn%20for%20internal%20g ears