Parametric Optimization of Cutting Parameters for Machining of AISI 403 by PVD Coated Tungsten Carbide Inserts Using Taguchi Method
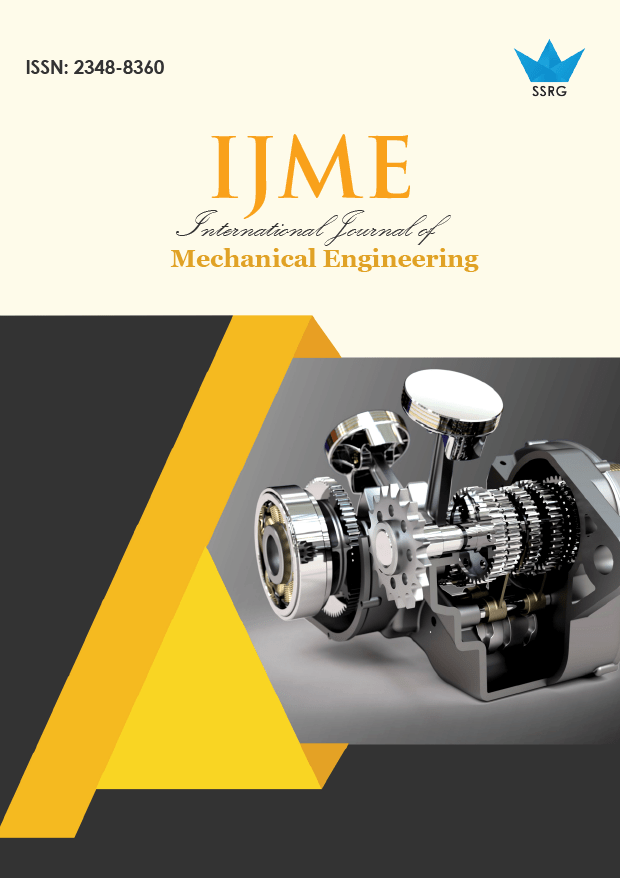
International Journal of Mechanical Engineering |
© 2024 by SSRG - IJME Journal |
Volume 11 Issue 6 |
Year of Publication : 2024 |
Authors : N.N. Jadeja, S.H. Zala, H.G. Vyas, N.D. Mehta |
How to Cite?
N.N. Jadeja, S.H. Zala, H.G. Vyas, N.D. Mehta, "Parametric Optimization of Cutting Parameters for Machining of AISI 403 by PVD Coated Tungsten Carbide Inserts Using Taguchi Method," SSRG International Journal of Mechanical Engineering, vol. 11, no. 6, pp. 62-72, 2024. Crossref, https://doi.org/10.14445/23488360/IJME-V11I6P108
Abstract:
AISI 403 stainless steel was used for the turning process in our research project. We conducted experiments with various process parameters, including cutting speed, depth of cut and feed to optimize the ideal values for cutting forces FX, FY, and RA. Using an L9 orthogonal array and optimizing output parameters, we studied the performance characteristics of turning with a CNMA120404 carbide insert with a 0.8mm nose radius. We employed the technique of Taguchi during CNC turning to optimize the effects of surface irregularity and cutting forces FX, FY. The use of AISI 403 stainless steel in manufacturing helps to minimize product costs. Our experimental analysis revealed that as speed increases, the total S/N ratio decreases while it increases with feed and cut depth. The optimized values of process factors, such as feed and cut depth, have the greatest influence on surface roughness after cutting speed.
Keywords:
Cutting forces, Stainless steel, Surface roughness, Taguchi, S/N ratio, Tungsten carbide inserts.
References:
[1] Lohithaksha M. Maiyar et al., “Optimization of Machining Parameters for end Milling of Inconel 718 Super Alloy Using Taguchi Based Grey Relational Analysis,” Procedia Engineering, vol. 64, pp. 1276-1282, 2013.
[CrossRef] [Google Scholar] [Publisher Link]
[2] Hilmi Pekşen, and Ali Kalyon, “Optimization and Measurement of Flank Wear and Surface Roughness via Taguchi Based Grey Relational Analysis,” Materials and Manufacturing Processes, vol. 36, no. 16, pp. 1865-1874, 2021.
[CrossRef] [Google Scholar] [Publisher Link]
[3] Ravi Patel, Ankit Kumar, and Jitendra Kumar Verma, “Analysis and Optimization of Surface Roughness in Turning Operation of
Mild Steel Using Taguchi Method,” International Journal of Engineering Trends and Technology, vol. 34, no. 7, pp. 337-341, 2016.
[CrossRef] [Google Scholar] [Publisher Link]
[4] Arshad Noor Siddiquee et al., “Optimization of Deep Drilling Process Parameters of AISI 321 Steel Using Taguchi Method,” Procedia Materials Science, vol. 6, pp. 1217-1225, 2014.
[CrossRef] [Google Scholar] [Publisher Link]
[5] Awadhesh Pal, S.K. Choudhury, and Satish Chinchanikar, “Machinability Assessment through Experimental Investigation during Hard and Soft Turning of Hardened Steel,” Procedia Materials Science, vol. 6, pp. 80-91, 2014.
[CrossRef] [Google Scholar] [Publisher Link]
[6] M. Aramesh et al., “Survival Life Analysis of the Cutting Tools During Turning Titanium Metal Matrix Composites (Ti-MMCs),” Procedia CIRP, vol. 14, pp. 605-609, 2014.
[CrossRef] [Google Scholar] [Publisher Link]
[7] J.A. Ghani, I.A. Choudhury, and H.H. Masjuki, “Wear Mechanism of TiN Coated Carbide and Uncoated Cermets Tools at High Cutting Speed Applications,” Journal of Materials Processing Technology, vol. 153-154, pp. 1067-1073, 2004.
[CrossRef] [Google Scholar] [Publisher Link]
[8] H. Hong et al., “Machinability of Steels and Titanium Alloys Under Lubrication,” Wear, vol. 162-164, pp. 34-39, 1993.
[CrossRef] [Google Scholar] [Publisher Link]
[9] G.K. Dosbaeva et al., “Cutting Temperature Effect on PCBN and CVD Coated Carbide Tools in Hard Turning of D2 Tool Steel,” International Journal of Refractory Metals and Hard Materials, vol. 50, pp. 1-8, 2015.
[CrossRef] [Google Scholar] [Publisher Link]
[10] D. Philip Selvaraj, P. Chandramohan, and M. Mohanraj, “Optimization of Surface Roughness, Cutting Force and Tool Wear of Nitrogen Alloyed Duplex Stainless Steel in a Dry Turning Process Using Taguchi Method,” Measurement, vol. 49, pp. 205-215, 2014.
[CrossRef] [Google Scholar] [Publisher Link]
[11] Håkan Thoors, H. Chandrasekaran, and Patrik Ölund, “Study of Some Active Wear Mechanisms in a Titanium-Based Cermet When Machining Steels,” Wear, vol. 162-164, Part. A, pp. 1-11, 1993.
[CrossRef] [Google Scholar] [Publisher Link]
[12] G.E. D'Errico, R. Calzavarini, and B. Vicenzi, “Influences of PVD Coatings on Cermet Tool Life in Continuous and Interrupted Turning,” Journal of Materials Processing Technology, vol. 78, no. 1-3, pp. 53-58, 1998.
[CrossRef] [Google Scholar] [Publisher Link]
[13] Atul Kulkarni et al., “Analysis of Cutting Temperature during Turning of SS 304 Using Uncoated and PVD Coated Carbide Inserts,” Materials Today: Proceedings, vol. 68, no. 6, pp. 2569-2573, 2022.
[CrossRef] [Google Scholar] [Publisher Link]
[14] Uttkarsh Patel et al., “Performance Evaluations of Ti-Based PVD Coatings Deposited on Cermet Tools for High-Speed Dry Finish Turning of AISI 304 Stainless Steel, Wear, vol. 492-493, 2022.
[CrossRef] [Google Scholar] [Publisher Link]
[15] SatyanarayanaKosaraju, M. Vijay Kumar, and N. Sateesh, “Optimization of Machining Parameter in Turning Inconel 625,” Materials Today: Proceedings, vol. 5, no. 2, pp. 5343-5348, 2018.
[CrossRef] [Google Scholar] [Publisher Link]
[16] Miroslav Radovanović et al., “Taguchi Approach for the Optimization of Cutting Parameters in Finish Turning of Medical Stainless Steel,” Applied Mechanics and Materials, vol. 809-810, pp. 153-158, 2015.
[CrossRef] [Google Scholar] [Publisher Link]
[17] M. Nalbant, H. Gökkaya, and G. Sur, “Application of Taguchi Method in the Optimization of Cutting Parameters for Surface Roughness in Turning,” Materials & Design, vol. 28, no. 4, pp. 1379-1385, 2007.
[CrossRef] [Google Scholar] [Publisher Link]
[18] Yuhui Yang et al., “The Grey-Taguchi Method Analysis for Processing Parameters Optimization and Experimental Assessment of 42CrMo Steel Treated by Ultrasonic Surface Rolling,” Journal of Materials Research and Technology, vol. 23, pp. 6244-6261, 2023.
[CrossRef] [Google Scholar] [Publisher Link]