Experimental Investigation of Nitrided Helical Gear With Different Helix Angles for Oil Drag Power Loss
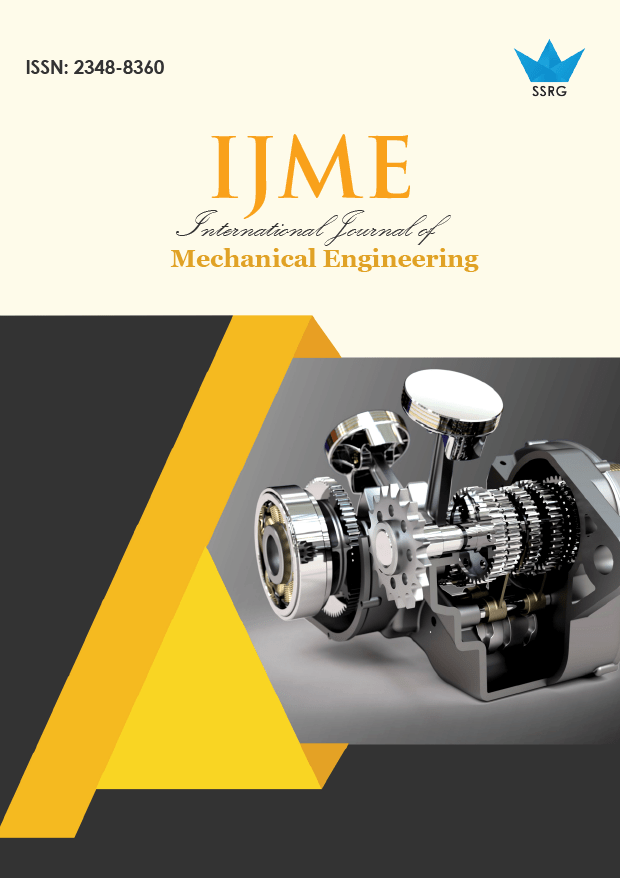
International Journal of Mechanical Engineering |
© 2024 by SSRG - IJME Journal |
Volume 11 Issue 6 |
Year of Publication : 2024 |
Authors : Devendrakumar J. Marsonia, Nishadevi N. Jadeja, Sanjay H. Zala, Nirav D. Mehta, Hardik G. Chothani, Hirendra G. Vyas |
How to Cite?
Devendrakumar J. Marsonia, Nishadevi N. Jadeja, Sanjay H. Zala, Nirav D. Mehta, Hardik G. Chothani, Hirendra G. Vyas, "Experimental Investigation of Nitrided Helical Gear With Different Helix Angles for Oil Drag Power Loss," SSRG International Journal of Mechanical Engineering, vol. 11, no. 6, pp. 105-114, 2024. Crossref, https://doi.org/10.14445/23488360/IJME-V11I6P112
Abstract:
Gears are broadly utilized for raised RPM and prevalent torque capabilities in vehicles and engineering equipment. The majority of these drives are lubricated by splashing oil. This way a colossal measure of energy is squandered in overcoming the thick drag of oil experienced by gear. This adversity is known as drag loss. The drag loss happens because of the interaction between oil and gear surfaces. The test rig is planned and grown so testing of single helical gear for drag power loss can be measured precisely. Helical gear with a sing SAE 9310 gear material is tried for drag power loss without Nitriding treatment. Then, the same Nitrided gear was tried for drag power loss. Nitriding of gear will, in general, solidify the outer layer of gear up to specific profundity by the testimony of nitrogen. The Central Composite Design (CCD) based Response Surface Methodology (RSM) was utilized to assess and streamline the drag power loss impact for nitrided and non-nitrided helical gears. The controlling factors gear rotating speed (RPM), volume of oil and oil temperature were thought of. A model was created, and in view of that, preliminary attempts were proposed to couple the controlling boundaries for limiting the drag power loss for the single helical gear at the ideal state of the cycle. It is seen that oil volume was the best affecting parameter for the drag power loss of gear in assessment with different other parameters like oil temperature, gear RPM etc. It very well might be because of most noteworthy F-insights an incentive for drag power loss. Furthermore, it is found that the nitrided helical gear encounters less drag from encompassing oil when contrasted with non nitrided gear. That might be because of the covering of the nitrogen layer over gear material, which furnishes a better surface with higher hardness subsequently, less oil drag is acting.
Keywords:
Helical gear, Drag power loss, Nitriding, RSM, CCD.
References:
[1] S. Seetharaman et al., “Oil Churning Power Losses of a Gear Pair: Experiments and Model Validation,” Journal of Tribology, vol. 131, no. 2, pp. 1-10, 2009.
[CrossRef] [Google Scholar] [Publisher Link]
[2] Anant S. Kolekar et al., “Windage and Churning Effects in Dipped Lubrication,” Journal of Tribology, vol. 136, no. 2, pp. 1-10, 2014.
[CrossRef] [Google Scholar] [Publisher Link]
[3] A.S. Terekhov, “Hydraulic Losses in Gearboxes with Oil Immersion,” Russian Engineering Journal, vol. 55, no. 5, pp. 7-11, 1975.
[Google Scholar]
[4] R.J. Boness, “Churning Losses of Discs and Gears Running Partially Submerged in Oil,” Proceeding of the ASME International Power Transmission and Gearing Conference, Chicago, vol. 1, pp. 355-359, 1989.
[Google Scholar] [Publisher Link]
[5] P. Luke, and A.V. Olver, “A Study of Churning Losses in Dip-Lubricated Spur Gear,” Proceedings of the Institution of Mechanical Engineers, Part G: Journal of Aerospace Engineering, vol. 213, no. 5, pp. 337-346, 1999.
[CrossRef] [Google Scholar] [Publisher Link]
[6] Soo Il Jeon, Improving Efficiency in Drive Lines: An Experimental Study on Churning Losses in Hypoid Axle, Department of Mechanical Engineering, Imperial College London, 2010.
[Google Scholar] [Publisher Link]
[7] S. Seetharaman, and A. Kahraman, “Load-Independent Spin Power Losses of a Spur Gear Pair: Model Formulation,”Journal of Tribology, vol. 131, no. 2, pp. 1-11, 2009.
[CrossRef] [Google Scholar] [Publisher Link]
[8] C. Changenet, and P. Velex, “A Model for the Prediction of Churning Losses in Geared Transmissions—Preliminary Results,”Journal of Mechanical Design, vol. 129, no. 1, pp. 128-133, 2007.
[CrossRef] [Google Scholar] [Publisher Link]
[9] Xiaozhou Hu et al., “Churning Power Losses of a Gearbox with Spiral Bevel Geared Transmission,” Tribology International, vol. 129, pp. 398-406, 2018.
[CrossRef] [Google Scholar] [Publisher Link]
[10] Robert W. Mann, and Charles H. Marston, “Friction Drag on Bladed Disks in Housings as a Function of Reynolds Number, Axial and Radial Clearance, and Blade Aspect Ratio and Solidity,” Journal of Fluids Engineering, vol. 83, no. 4, pp. 719-723, 2017.
[CrossRef] [Google Scholar] [Publisher Link]
[11] J.W. Daily, and R.E. Nece, “Chamber Dimension Effects on Induced Flow and Frictional Resistance of Enclosed Rotating Disks,” Journal of Basic Engineering, vol. 82, no. 1, pp. 217-230, 1960.
[CrossRef] [Google Scholar] [Publisher Link]
[12] S. Laruelle et al., “Experimental Investigations and Analysis on Churning Losses of Splash Lubricated Spiral Bevel Gears,” Mechanics & Industry, vol. 18, no. 4, 2017.
[CrossRef] [Google Scholar] [Publisher Link]
[13] Qianlei Peng, Liangjin Gui, and Zijie Fan, “Numerical and Experimental Investigation of Splashing Oil Flow in a Hypoid Gearbox,” Engineering Applications of Computational Fluid Mechanics, vol. 12, no. 1, pp. 324-333, 2018.
[CrossRef] [Google Scholar] [Publisher Link]
[14] D.I. Lalwani, N.K. Mehta, and P.K. Jain, “Experimental Investigations of Cutting Parameters Influence on Cutting Torques and Surface Roughness in Finish Hard Turning of MDN250 Steel,” Journal of Materials Processing Technology, vol. 206, no. 1-3, pp. 167-179, 2008.
[CrossRef] [Google Scholar] [Publisher Link]
[15] Sushanta Kumar Behera et al., “Application of Response Surface Methodology (RSM) for Optimization of Leaching Parameters for Ash Reduction from Low-Grade Coal,” International Journal of Mining Science and Technology, vol. 28, no. 4, pp. 621-629, 2018.
[CrossRef] [Google Scholar] [Publisher Link]
[16] Abd Elaziz Sarrai et al., “Using Central Composite Experimental Design to Optimize the Degradation of Tylosin from Aqueous Solution by Photo-Fenton Reaction,” Materials, vol. 9, no. 6, pp. 1-11, 2016.
[CrossRef] [Google Scholar] [Publisher Link]