Investigating FDM Electrodes for EDM Machining of Mild Steel: Performance Evaluation
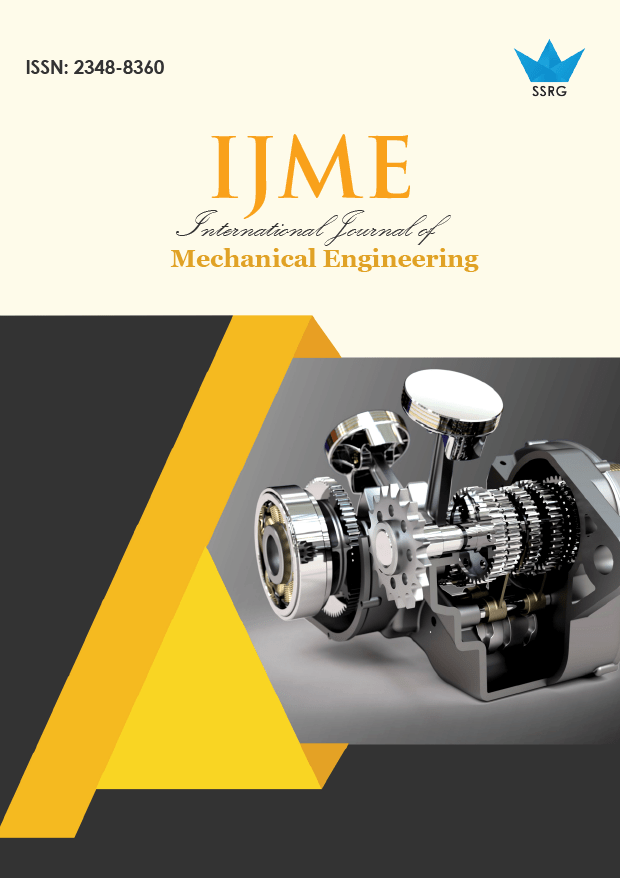
International Journal of Mechanical Engineering |
© 2024 by SSRG - IJME Journal |
Volume 11 Issue 6 |
Year of Publication : 2024 |
Authors : N.J. Shirbhate, S.M. Vinchurkar, A.B. Borade |
How to Cite?
N.J. Shirbhate, S.M. Vinchurkar, A.B. Borade, "Investigating FDM Electrodes for EDM Machining of Mild Steel: Performance Evaluation," SSRG International Journal of Mechanical Engineering, vol. 11, no. 6, pp. 123-130, 2024. Crossref, https://doi.org/10.14445/23488360/IJME-V11I6P114
Abstract:
The purpose of this study is to analyze the performance of the tool electrode used in mild steel Electrical Discharge Machining (EDM) that is produced using the Fused Deposition Modeling (FDM) technique. The study evaluates the suitability of FDM-generated electrodes compared to traditional manufacturing methods and explores the effect of various process parameters on machining performance. Data from the experiments were analyzed using statistical techniques, including ANOVA, to determine significant correlations between process variables and key performance metrics such as Surface Roughness (SR) and Material Removal Rate (MRR). The results indicate that FDM-produced electrodes exhibit comparable performance to traditionally manufactured electrodes, with significant correlations observed between pulse-on-time, current, and voltage parameters and machining efficiency. The study highlights the potential of FDM technology as a cost-effective and efficient method for EDM electrode fabrication while also identifying areas for further research to optimize process parameters and explore advanced materials for enhanced performance.
Keywords:
FDM, EDM, Tool electrode, Performance analysis, Additive manufacturing.
References:
[1] Ricky J. Blom, “Production and Evaluation of Rapid Tooling for Electric Discharge Machining using Electroforming and Spray Metal Deposition Techniques,” Master Thesis, Queensland University of Technology, pp. 1-169, 2005.
[Google Scholar] [Publisher Link]
[2] A. Arthur, and P.M. Dickens, “The Measurement of Heat Distribution in Stereolithography Electrodes During Electro-Discharge Machining,” International Journal of Production Research, vol. 36, no. 9, pp. 2451-2461, 1998.
[CrossRef] [Google Scholar] [Publisher Link]
[3] Fred L. Amorim et al., “Performance of Sinking EDM Electrodes Made by Selective Laser Sintering Technique,” The International Journal of Advanced Manufacturing Technology, vol. 65, pp. 1423-1428, 2013.
[CrossRef] [Google Scholar] [Publisher Link]
[4] John Kechagias et al., “EDM Electrode Manufacture using Rapid Tooling: A Review,” Journal of Materials Science, vol. 43, pp. 2522-2535, 2008.
[CrossRef] [Google Scholar] [Publisher Link]
[5] Dorota Oniszczuk-Ćwiercz et al., “Finishing Additively Manufactured Ti6Al4V Alloy with Low-Energy Electrical Discharges,” Materials, vol. 16, no. 17, pp. 1-175, 2023.
[CrossRef] [Google Scholar] [Publisher Link]
[6] Shitanshu Arya, and Pulak Mohan Pandey, “Statistical Modellingand Process Optimization of EDM Electrode Fabricated using Pressureless Microwave Sintering and Rapid Tooling Route,” Proceedings of the Institution of Mechanical Engineers, Part E: Journal of Process Mechanical Engineering, 2024.
[CrossRef] [Google Scholar] [Publisher Link]
[7] KashifIshfaq, Muhammad Umar Farooq, and Catalin I. Pruncu, “Reducing the Geometrical Machining Errors Incurred During Die Repair and Maintenance through Electric Discharge Machining (EDM),” The International Journal of Advanced Manufacturing Technology, vol. 117, pp. 3153-3168, 2021.
[CrossRef] [Google Scholar] [Publisher Link]
[8] Azhar Equbal et al., “A Critical Insight into the Use of FDM for Production of EDM Electrode,” Alexandria Engineering Journal, vol. 61, no. 5, pp. 4057-4066, 2022.
[CrossRef] [Google Scholar] [Publisher Link]
[9] Saroj Kumar Padhi et al., “Performance Analysis of a Thick Copper-Electroplated FDM ABS Plastic Rapid Tool EDM Electrode,” Advances in Manufacturing, vol. 6, pp. 442-456, 2018.
[CrossRef] [Google Scholar] [Publisher Link]
[10] L. Mahipal Reddy et al., “Estimation of Electrical Conductivity of ABS and PLA based EDM Electrode Fabricated by using FDM 3DPrinting Process,” International Journal of Modern Engineering and Research Technology, vol. 5, pp. 332-338, 2018.
[Google Scholar] [Publisher Link]
[11] Anshuman Kumar Sahu, and Siba Sankar Mahapatra, “Performance Analysis of Tool Electrode Prepared through Laser Sintering Process During Electrical Discharge Machining of Titanium,” The International Journal of Advanced Manufacturing Technology, vol. 106, pp. 1017-1041, 2020.
[CrossRef] [Google Scholar] [Publisher Link]
[12] Azhar Equbal, Md. Israr Equbal, and Anoop Kumar Sood, “An Investigation on the Feasibility of Fused Deposition Modelling Process in EDM Electrode Manufacturing,” CIRP Journal of Manufacturing Science and Technology, vol. 26, pp. 10-25, 2019.
[CrossRef] [Google Scholar] [Publisher Link]
[13] Ujwal A. Danade, Shrikant D. Londhe, and Rajesh M. Metkar, “Machining Performance of 3D-Printed ABS Electrode Coated with Copper in EDM,” Rapid Prototyping Journal, vol. 25, no. 7, pp. 1224-1231, 2019.
[CrossRef] [Google Scholar] [Publisher Link]
[14] G.K. Awari et al., Additive Manufacturing and 3D Printing Technology: Principles and Applications, CRC Press, pp. 1-309, 2021.
[Google Scholar] [Publisher Link]
[15] Laukik P. Raut, and Ravindra V. Taiwade, “Microstructure and Mechanical Properties of Wire Arc Additively Manufactured Bimetallic Structure of Austenitic Stainless Steel and Low Carbon Steel,” Journal of Materials Engineering and Performance, vol. 31, pp. 8531-8541, 2022.
[CrossRef] [Google Scholar] [Publisher Link]
[16] Anoop Kumar Sood, and AzharEqubal, “Feasibility of FDM-Electroplating Process for EDM Electrode Fabrication,” Materials Today: Proceedings, vol. 28, no. 2, pp. 1154-1157, 2020.
[CrossRef] [Google Scholar] [Publisher Link]
[17] Laukik P. Raut, R.V. Taiwade, and Ankit Agarwal, “Investigation of Microstructural and Corrosion Behavior of 316LSi Structure Developed by Wire Arc Additive Manufacturing,” Materials Today Communications, vol. 35, 2023.
[CrossRef] [Google Scholar] [Publisher Link]
[18] T. Sathies, P. Senthil, and M.S. Anoop, “A Review on Advancements in Applications of Fused Deposition Modelling Process,” Rapid Prototyping Journal, vol. 26, no. 4, pp. 669-687, 2020.
[CrossRef] [Google Scholar] [Publisher Link]
[19] Laukik P. Raut, and Ravindra V. Taiwade, “Wire Arc Additive Manufacturing: A Comprehensive Review and Research Directions,” Journal of Materials Engineering and Performance, vol. 30, pp. 4768-4791, 2021.
[CrossRef] [Google Scholar] [Publisher Link]
[20] Raymond Magabe et al., “Modeling and Optimization of Wire-EDM Parameters for Machining of Ni55.8Ti Shape Memory Alloy using Hybrid Approach of Taguchi and NSGA-II,” The International Journal of Advanced Manufacturing Technology, vol. 102, pp. 1703-1717, 2019.
[CrossRef] [Google Scholar] [Publisher Link]
[21] Tanmay Tiwari, Akash Nag, and Amit Rai Dixit, “Investigations on Bending of Micro-Thin Sheets using Spark Discharges,” Materials and Manufacturing Processes, vol. 35, no. 12, pp. 1362-1371, 2020.
[CrossRef] [Google Scholar] [Publisher Link]
[22] Pankaj Kumar Gupta, Akshay Dvivedi, and Pradeep Kumar, “Effect of Pulse Duration on Quality Characteristics of Blind Hole Drilled in Glass by ECDM,” Materials and Manufacturing Processes, vol. 31, no. 13, pp. 1740-1748, 2016.
[CrossRef] [Google Scholar] [Publisher Link]
[23] Yan-Cherng Lin et al., “Electrical Discharge Machining (EDM) Characteristics Associated with Electrical Discharge Energy on Machining of Cemented Tungsten Carbide,” Materials and Manufacturing Processes, vol. 23, no. 4, pp. 391-399, 2008.
[CrossRef] [Google Scholar] [Publisher Link]