Design and Analysis of Milling Cutter using Fem
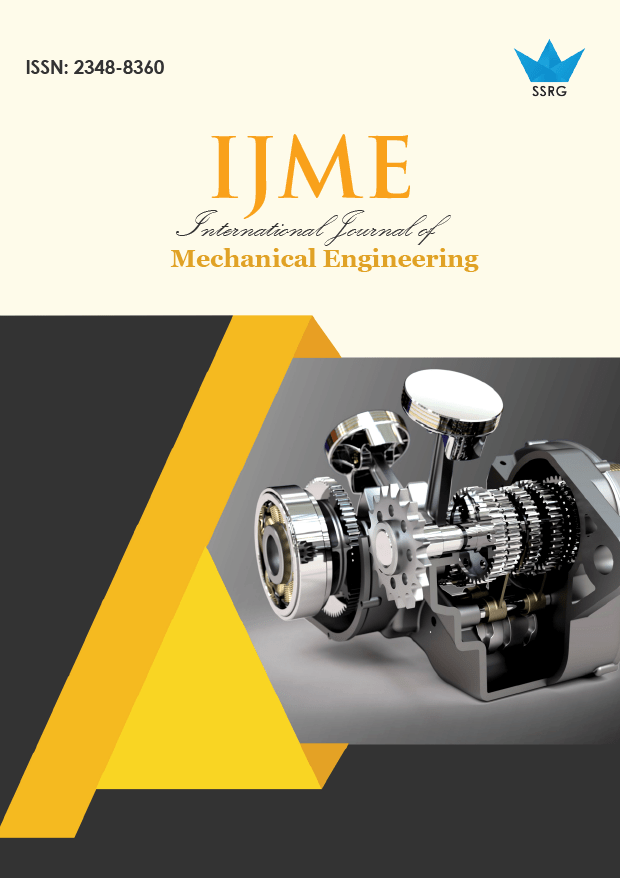
International Journal of Mechanical Engineering |
© 2018 by SSRG - IJME Journal |
Volume 5 Issue 12 |
Year of Publication : 2018 |
Authors : Humayun Syed, V.Suresh, P.Vijayanand |
How to Cite?
Humayun Syed, V.Suresh, P.Vijayanand, "Design and Analysis of Milling Cutter using Fem," SSRG International Journal of Mechanical Engineering, vol. 5, no. 12, pp. 8-14, 2018. Crossref, https://doi.org/10.14445/23488360/IJME-V5I12P103
Abstract:
Processing is An procedure for generating even What's more mind boggling shapes with the utilization of multi-tooth cutting tool, which will be called a processing cutter and the cutting edges are known as teethe. Those pivot of revolution of the cutting apparatus is peroxide blonde of the bearing for feed, whichever parallel or peroxide blonde of the machined surface. Those machine device that customarily performs this operation may be a
processing machine. Processing will be an intruded on cutting operation: those teeth of the processing cutter enter Also retreat those worth of effort
Throughout each transformation. This interfered cutting movement subjects those teethe with a cycle about sway energy and warm stun around each
revolution. The apparatus material Furthermore cutter geometry must be planned with withstand these states. Cutting liquids need aid key for the vast
majority processing operations.
In this project those plan parts for processing cutter will be analysed Also we take two business metal cutting business What's more cowhide industry. Planned an uncommon processing cutters, Similarly as for every mechanical prerequisites. Those objective acknowledged is those plan and displaying for processing cutter What's more should investigate Different stress parts acting on it. Different outlining
methodologies are acknowledged on configuration those powerful processing cutter similar to external diameter, internal diameter, radius, teeth point and so on. Those plan and Investigation is conveyed crazy utilizing the software's such as SOLIDWORKS Furthermore ANSYS.
Keywords:
ANSYS, CATIA, cutting fluids, cutting edges, High Speed Steel, Milling Speed, machined surfaces, surface milling cutter.
References:
[1] Alauddin et al (1995) "formed a surface-roughness model to the wind processing of 190 BHN steel".
[2] Mike et al (1999) "the creator investigated another approach for complete surface prediction done end-milling operations".
[3] Yu Hsuan et al (1999) "produced an in-process built surface distinguishment framework with anticipate those surface unpleasantness at last processing procedure".
[4] Benardos&Vosniakos (2002) "introduced a neural system displaying".
[5] Nithin K Mani, Prof. Cijo Mathew., Prof. Prakash M Kallanickal"Optimization of Cutting Parameters & Nanoparticle Concentration in CNC Turning of EN8 Steel using Al2O3 Nanofluids as Coolant", International Journal of Engineering Trends and Technology (IJETT), V29(6),290-294 November 2015.
[6] Ming & hung (2004) "analysed those impact of machining parameters for example, such that those cutting speed, feed, profundity for cut, concavity Also pivotal easing angles of the forefront of the conclusion Plant ahead surface unpleasantness in the opening end processing of aluminum compound".
[7] Ghani et al (2004) "connected those Taguchi streamlining technique".
[8] Brezocnik et al (2004) "recommended hereditary modifying approach should anticipate the surface unpleasantness done end processing".
[9] Oktem et al (2005) "concentrated on the improvement for an compelling technique".