An Experimental Analysis of the Effects of Graphite Powder Mixed Dielectric Medium in the Electrical Discharge Machining of Cu-Al Alloy
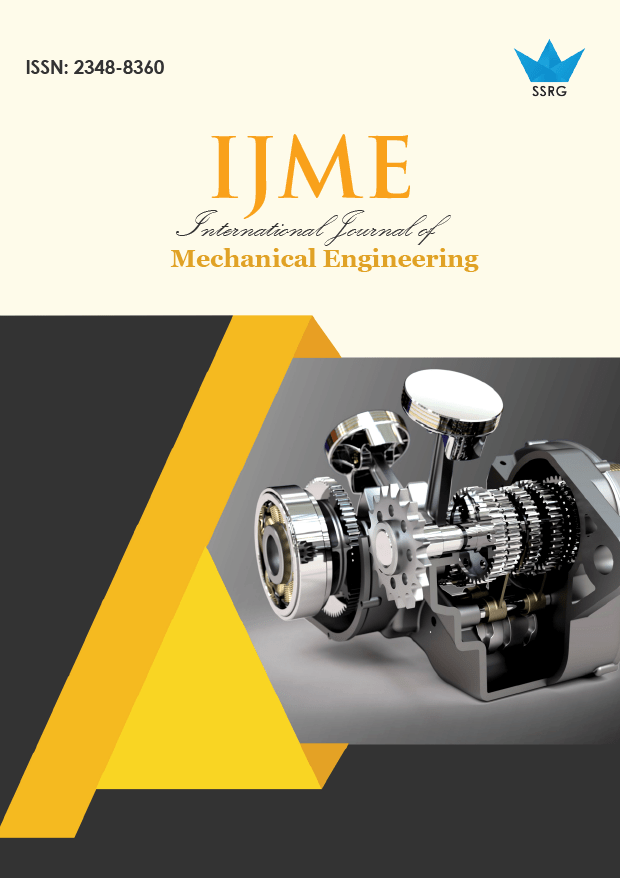
International Journal of Mechanical Engineering |
© 2024 by SSRG - IJME Journal |
Volume 11 Issue 8 |
Year of Publication : 2024 |
Authors : Mohit Kumar, Manoj Kumar Poddar, Dharmvir Kumar, Chandra Bhushan Kumar Yadav |
How to Cite?
Mohit Kumar, Manoj Kumar Poddar, Dharmvir Kumar, Chandra Bhushan Kumar Yadav, "An Experimental Analysis of the Effects of Graphite Powder Mixed Dielectric Medium in the Electrical Discharge Machining of Cu-Al Alloy," SSRG International Journal of Mechanical Engineering, vol. 11, no. 8, pp. 74-83, 2024. Crossref, https://doi.org/10.14445/23488360/IJME-V11I8P109
Abstract:
Electric Discharge Machining (EDM) is a non-traditional manufacturing method used in a variety of sectors, including automotive, military, aerospace, and microsystems, to produce low-cost products with consistent quality. PowderMixed Electric Discharge Machining (PMEDM) is a novel technique that reduces the insulating strength of the fluid and increases the spark gap between the tool and workpiece by combining the electrically conductive powder with the dielectric. This leads to a more consistent process, which enhances the rate of material removal and the quality of the surface. The present study examined the effects of dielectric mixed with micro-sized graphite powder on the material removal rate and surface roughness of the Cu-Al alloy workpiece material. The purpose of using Cu-Al alloy as a work material is to study the process behavior of this material, which has specific applications in nuclear reactors, spacecraft, rocket motors, and gas turbines. We use the Taguchi technique to design the experiments and the ANOVA technique to analyze the results. Using powder-mixed dielectric improves the MRR and SR, with peak current and powder concentration being the most significant factors during the process.
Keywords:
PMEDM, Cu-Al alloy, Taguchi method, ANOVA, Regression.
References:
[1] Hassan Abdel-Gawad El-Hofy, Advanced Machining Processes: Nontraditional and Hybrid Machining Processes, McGraw Hill LLC, pp. 1-288, 2005.
[Google Scholar] [Publisher Link]
[2] H.K. Kansal, Sehijpal Singh, and Pradeep Kumar, “Technology and Research Developments in Powder Mixed Electric Discharge Machining (PMEDM),” Journal of Materials Processing Technology, vol. 184, no. 1-3, pp. 32-41, 2007.
[CrossRef] [Google Scholar] [Publisher Link]
[3] Kun Ling Wu et al., “Improvement of Surface Finish on SKD Steel Using Electro-Discharge Machining with Aluminum and Surfactant Added Dielectric,” International Journal of Machine Tools & Manufacture, vol. 45, no. 10, pp. 1195-1201, 2005.
[CrossRef] [Google Scholar] [Publisher Link]
[4] Y. Uno, A. Okada, and S. Cetin, “Surface Modification of EDMed Surface with Powder Mixed Fluid,” 2 nd International Conference on Design and Production of Dies and Molds, pp. 86-92, 2001.
[Google Scholar] [Publisher Link]
[5] Paulo Peças, and Elsa Henriques, “Effect of the Powder Concentration and Dielectric Flow in the Surface Morphology in Electrical Discharge Machining with Powder-Mixed Dielectric (PMD-EDM),” The International Journal of Advanced Manufacturing Technology, vol. 37, pp. 1120-1132, 2008.
[CrossRef] [Google Scholar] [Publisher Link]
[6] H.K. Kansal, Sehijpal Singh, and Pradeep Kumar, “Effect of Silicon Powder Mixed EDM on Machining Rate of AISI D2 Die Steel,” Journal of Manufacturing Processes, vol. 9, no. 1, pp. 13-22, 2007.
[CrossRef] [Google Scholar] [Publisher Link]
[7] Han-Ming Chow et al., “The Use of SiC Powder in Water as Dielectric for Micro-Slit EDM Machining,” Journal of Materials Processing Technology, vol. 195, no. 1-3, pp. 160-170, 2008.
[CrossRef] [Google Scholar] [Publisher Link]
[8] Biing Hwa Yan, Hsien Chung Tsai, and Fuang Yuan Huang, “The Effect in EDM of a Dielectric of a Urea Solution in Water on Modifying the Surface of Titanium,” International Journal of Machine Tools and Manufacture, vol. 45, no. 2, pp. 194-200, 2005.
[CrossRef] [Google Scholar] [Publisher Link]
[9] G. Bharath Reddy, G. Naveen Kumar, and K. Chandrashekar, “Experimental Investigation on Process Performance of Powder Mixed Electric Discharge Machining of AISI D3 Steel and EN-31 Steel,” International Journal of Current Engineering and Technology, vol. 4, no. 3, pp. 1218-1222, 2014.
[Google Scholar] [Publisher Link]
[10] Gangadharudu Talla, S. Gangopadhayay, and C.K. Biswas, “State of the Art in Powder-Mixed Electric Discharge Machining: A Review,” Proceedings of the Institution of Mechanical Engineers, Part B: Journal of Engineering Manufacture, vol. 231, no. 14, pp. 2511-2526, 2017.
[CrossRef] [Google Scholar] [Publisher Link]
[11] A. Sugunakar, A. Kumar, and R. Markandeya, “Effect of Powder Mixed Dielectric Fluid on MRR and SR during Electrical Discharge Machining of RENE 80,” International Journal of Engineering Research and Development, vol. 13, no. 5, pp. 37-43, 2017.
[Google Scholar] [Publisher Link]
[12] Gourab Mohanty et al., “Experimental Investigations on Graphite Mixed Electric Discharge Machining of En-19 Alloy Steel,” Materials Today: Proceedings, vol. 5, no. 9, pp. 19418-19423, 2018.
[CrossRef] [Google Scholar] [Publisher Link]
[13] Ayanesh Y. Joshi, and Anand Y. Joshi, “A Systematic Review on Powder Mixed Electrical Discharge Machining,” Heliyon, vol. 5, no. 12, pp. 1-12, 2019.
[CrossRef] [Google Scholar] [Publisher Link]
[14] Niwat Mookam et al., “Effects of Graphite and Boron Carbide Powders Mixed into Dielectric Fluid on Electrical Discharge Machining of SKD 11 Tool Steel,” Arabian Journal for Science and Engineering, vol. 46, pp. 2553-2563, 2021.
[CrossRef] [Google Scholar] [Publisher Link]
[15] Jay Vora et al., “Machining Parameter Optimization and Experimental Investigations of Nano-Graphene Mixed Electrical Discharge Machining of Nitinol Shape Memory Alloy,” Journal of Materials Research and Technology, vol. 19, pp. 653-668, 2022.
[CrossRef] [Google Scholar] [Publisher Link]
[16] Jay Vora et al., “Multi-Response Optimization and Influence of Expanded Graphite on Performance of WEDM Process of Ti6Al4V,” Journal of Manufacturing and Materials Processing, vol. 7, no. 3, pp. 1-17, 2023.
[CrossRef] [Google Scholar] [Publisher Link]
[17] Chander Prakash et al., “Experimental Investigations in Powder Mixed Electric Discharge Machining of Ti–35Nb–7Ta–5ZrβTitanium Alloy,” Materials and Manufacturing Processes, vol. 32, no. 3, pp. 274-285, 2017.
[CrossRef] [Google Scholar] [Publisher Link]
[18] Nesredin Chekole Deresse, Vivek Deshpande, and Ismail W.R. Taifa, “Experimental Investigation of the Effects of Process Parameters on Material Removal Rate Using Taguchi Method in External Cylindrical Grinding Operation,” Engineering Science and Technology, an International Journal, vol. 23, no. 2, pp. 405-420, 2020.
[CrossRef] [Google Scholar] [Publisher Link]
[19] M. Fakkir Mohamed, and K. Lenin, “Optimization of Wire EDM Process Parameters Using Taguchi Technique,” Materials Today: Proceedings, vol. 21, no. 1, pp. 527-530, 2020.
[CrossRef] [Google Scholar] [Publisher Link]
[20] Ali Yeganefar, Seyed Ali Niknam, and Reza Asadi, “The Use of Support Vector Machine, Neural Network, and Regression Analysis to Predict and Optimize Surface Roughness and Cutting Forces in Milling,” The International Journal of Advanced Manufacturing Technology, vol. 105, pp. 951-965, 2019.
[CrossRef] [Google Scholar] [Publisher Link]
[21] Jackson Pasini Mairing, “The Effect of Advance Statistics Learning Integrated Minitab and Excel with Teaching Teams,” International Journal of Instruction, vol. 13, no. 2, pp. 139-150, 2020.
[CrossRef] [Google Scholar] [Publisher Link]