Optimizing Thermal Management in Electric Battery Packs through Heat Pipe-Based Systems and Aluminum Sleeve Integration
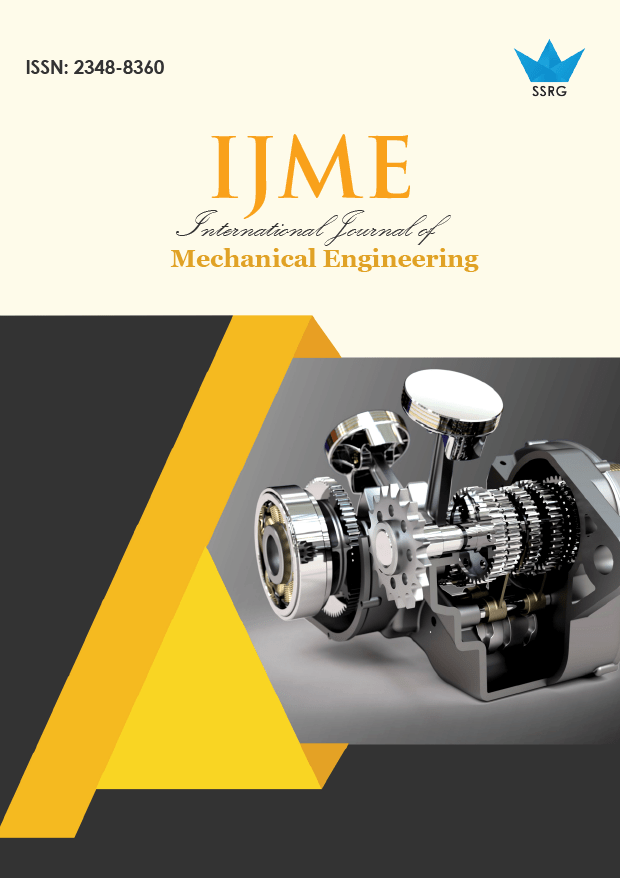
International Journal of Mechanical Engineering |
© 2024 by SSRG - IJME Journal |
Volume 11 Issue 8 |
Year of Publication : 2024 |
Authors : Satish Patil, Prajitsen Damle, Pawan Meshram, Nilesh Salunke |
How to Cite?
Satish Patil, Prajitsen Damle, Pawan Meshram, Nilesh Salunke, "Optimizing Thermal Management in Electric Battery Packs through Heat Pipe-Based Systems and Aluminum Sleeve Integration," SSRG International Journal of Mechanical Engineering, vol. 11, no. 8, pp. 122-133, 2024. Crossref, https://doi.org/10.14445/23488360/IJME-V11I8P114
Abstract:
The study aimed to investigate the performance of the battery thermal management when conducting a performance analysis of the BTMS, and the consequence of heat pipes on the maximum temperature of the battery cells was examined utilizing the ANSYS Fluent 2024R1 commercial CFD Package. Several important findings arose from detailed CFD analysis done in this project: Firstly, it was clear that the ability of cylindrical heat pipes to improve performance increased in line with the quantity of heat produced by the battery cells. This increase was attributed to its other part, heat pipes, through which it justified attaining the requisite temperature for phase change according to the working norm of heat pipes. In particular, the minimum temperature is attained with the use of a 30W battery system using a heat pipe with a star shape. On the other hand, the highest temperature was found during the heat generation of 80W without the heat pipe system, irrespective of the working fluid flow rate. Finally, the study emphasized the greatest need for utilising heat pipe thermal management systems where and when feasible, most significantly in battery systems that generate approximately 80W heat. The absence of such systems could result in an overheating state and all the consequent hazards to the battery shell and the system. Cylindrical heat pipes are adaptive in releasing heat as the production of heat from batteries increases. From the results obtained, it was evident that the high-power LHCP systems where heat pipe integration is not incorporated and the system generated high heat are at higher temperatures; those without heat pipe integration and low heat generation are at lower temperatures, suggesting that heat pipe thermal management is necessary in case of high heat generation for safety and reliability. In addition to the previous finding, these results provide conclusive support that the heat pipe-based TMS is vital for sustaining other critical temperature profiles needed for the electric vehicle battery pack for longest-running functionality as well as to arrest catastrophes.
Keywords:
Battery thermal management, Cylindrical battery, Heat pipe, Thermal performance, CFD.
References:
[1] Guizhou Ren, Guoqing Ma, and Ning Cong, “Review of Electrical Energy Storage System for Vehicular Applications,” Renewable and Sustainable Energy Reviews, vol. 41, pp. 225-236, 2015.
[CrossRef] [Google Scholar] [Publisher Link]
[2] Wangyu Liu et al., “Experimental Investigation on Thermal Management of Cylindrical Li-Ion Battery Pack Based on Vapor Chamber Combined with Fin Structure,” Applied Thermal Engineering, vol. 162, 2019.
[CrossRef] [Google Scholar] [Publisher Link]
[3] Jialin Liang et al., “Thermal–Electrochemical Simulation of Electrochemical Characteristics and Temperature Difference for a Battery Module under Two-Stage Fast Charging,” Journal of Energy Storage, vol. 29, 2020.
[CrossRef] [Google Scholar] [Publisher Link]
[4] Zhonghao Rao, and Shuangfeng Wang, “A Review of Power Battery Thermal Energy Management,” Renewable and Sustainable Energy Reviews, vol. 15, no. 9, pp. 4554-4571, 2011.
[CrossRef] [Google Scholar] [Publisher Link]
[5] Chengchao Yuan et al., “Inhibition Effect of Different Interstitial Materials on Thermal Runaway Propagation in the Cylindrical LithiumIon Battery Module,” Applied Thermal Engineering, vol. 153, pp. 39-50, 2019.
[CrossRef] [Google Scholar] [Publisher Link]
[6] Haobing Zhou et al., “Thermal Performance of Cylindrical Lithium-Ion Battery Thermal Management System Based on Air Distribution Pipe,” International Journal of Heat and Mass Transfer, vol. 131, pp. 984-998, 2019.
[CrossRef] [Google Scholar] [Publisher Link]
[7] E. Jiaqiang et al., “Investigation on Thermal Performance and Pressure Loss of the Fluid Cold-Plate Used in Thermal Management System of the Battery Pack,” Applied Thermal Engineering, vol. 145, pp. 552-568, 2018.
[CrossRef] [Google Scholar] [Publisher Link]
[8] Yunhua Gan et al., “Development of Thermal Equivalent Circuit Model of Heat Pipe-Based Thermal Management System for a Battery Module with Cylindrical Cells,” Applied Thermal Engineering, vol. 164, 2020.
[CrossRef] [Google Scholar] [Publisher Link]
[9] Qiqiu Huang et al., “Experimental Investigation of the Thermal Performance of Heat Pipe Assisted Phase Change Material for Battery Thermal Management System,” Applied Thermal Engineering, vol. 141, pp. 1092-1100, 2018.
[CrossRef] [Google Scholar] [Publisher Link]
[10] Dafen Chen et al., “Comparison of Different Cooling Methods for Lithium Ion Battery Cells,” Applied Thermal Engineering, vol. 94, pp. 846-854, 2016.
[CrossRef] [Google Scholar] [Publisher Link]
[11] Yongxin Lai et al., “A Compact and Lightweight Liquid-Cooled Thermal Management Solution for Cylindrical Lithium-Ion Power Battery Pack,” International Journal of Heat and Mass Transfer, vol. 144, 2019.
[[CrossRef] [Google Scholar] [Publisher Link]
[12] Wenjiong Cao et al., “Thermal Modeling of Full-Size-Scale Cylindrical Battery Pack Cooled by Channeled Liquid Flow,” International Journal of Heat and Mass Transfer, vol. 138, pp. 1178-1187, 2019.
[CrossRef] [Google Scholar] [Publisher Link]
[13] Z.Y. Jiang, and Z.G. Qu, “Lithium–Ion Battery Thermal Management Using Heat Pipe and Phase Change Material during Discharge– Charge Cycle: A Comprehensive Numerical Study,” Applied Energy, vol. 242, pp. 378-392, 2019.
[CrossRef] [Google Scholar] [Publisher Link]
[14] Zhonghao Rao et al., “Experimental Investigation on Thermal Management of Electric Vehicle Battery with Heat Pipe,” Energy Conversion and Management, vol. 65, pp. 92-97, 2013.
[CrossRef] [Google Scholar] [Publisher Link]
[15] Yunhua Gan et al., “A Numerical Study on the Performance of a Thermal Management System for a Battery Pack with Cylindrical Cells Based on Heat Pipes,” Applied Thermal Engineering, vol. 179, 2020.
[CrossRef] [Google Scholar] [Publisher Link]
[16] Jaewan Kim, Jinwoo Oh, and Hoseong Lee, “Review on Battery Thermal Management System for Electric Vehicles,” Applied Thermal Engineering, vol. 149, pp. 192-212, 2019.
[CrossRef] [Google Scholar] [Publisher Link]
[17] Yonghuang Ye et al., “Numerical Analyses on Optimizing a Heat Pipe Thermal Management System for Lithium-Ion Batteries during Fast Charging,” Applied Thermal Engineering, vol. 86, pp. 281-291, 2015.
[CrossRef] [Google Scholar] [Publisher Link]
[18] Rui Zhao, Junjie Gu, and Jie Liu, “An Experimental Study of Heat Pipe Thermal Management System with Wet Cooling Method for Lithium Ion Batteries,” Journal of Power Sources, vol. 273, pp. 1089-1097, 2015.
[CrossRef] [Google Scholar] [Publisher Link]
[19] Jialin Liang, Yunhua Gan, and Yong Li, “Investigation on the Thermal Performance of a Battery Thermal Management System Using Heat Pipe under Different Ambient Temperatures,” Energy Conversion and Management, vol. 155, pp. 1-9, 2018.
[CrossRef] [Google Scholar] [Publisher Link]
[20] Q. Wang et al., “Experimental Investigation on EV Battery Cooling and Heating by Heat Pipes,” Applied Thermal Engineering, vol. 88, pp. 54-60, 2015.
[CrossRef] [Google Scholar] [Publisher Link]
[21] Hyuntae Kim et al., “Development of PCM-Based Shell-and-Tube Thermal Energy Storages for Efficient EV Thermal Management,” International Communications in Heat and Mass Transfer, vol. 154, 2024.
[CrossRef] [Google Scholar] [Publisher Link]
[22] Zhonghao Rao et al., “Thermal Performance of Liquid Cooling Based Thermal Management System for Cylindrical Lithium-Ion Battery Module with Variable Contact Surface,” Applied Thermal Engineering, vol. 123, pp. 1514-1522, 2017.
[CrossRef] [Google Scholar] [Publisher Link]
[23] Jan Bohacek, Miroslav Raudensky, and Ebrahim Karimi-Sibaki, “Polymeric Hollow Fibers: Uniform Temperature of Li-Ion Cells in Battery Modules,” Applied Thermal Engineering, vol. 159, pp. 1-11, 2019.
[CrossRef] [Google Scholar] [Publisher Link]
[24] Jinwang Li et al., “Effect of Fabricating Parameters on Properties of Sintered Porous Wicks for Loop Heat Pipe,” Powder Technology, vol. 204, no. 2-3, pp. 241-248, 2010.
[CrossRef] [Google Scholar] [Publisher Link]
[25] Mao-Sung Wu et al., "Heat Dissipation Design for Lithium-Ion Batteries," Journal of Power Sources, vol. 109, no. 1, pp. 160-166, 2002.
[CrossRef] [Google Scholar] [Publisher Link]
[26] Zhonghao Rao et al., "Experimental Investigation on Thermal Management of Electric Vehicle Battery with Heat Pipe," Energy Conversion and Management, vol. 65, pp. 92-97, 2013.
[CrossRef] [Google Scholar] [Publisher Link]
[27] Remi Bertossi, “Modeling of Heat and Mass Transfers in Heat Pipes. Contribution to the Analysis of Interface Phenomena Occurring in Two-Phase Flows,” Free University of Brussels, Poitiers, France, pp. 1-221, 2009.
[Google Scholar] [Publisher Link]
[28] Peyman Taheri, and Majid Bahrami, "Temperature Rise in Prismatic Polymer Lithium-Ion Batteries: An Analytic Approach," SAE International Journal of Passenger Cars-Electronic and Electrical Systems, vol. 5, no. 1, pp. 164-176, 2012.
[CrossRef] [Google Scholar] [Publisher Link]
[29] Hussein Mbulu, Yossapong Laoonual, and Somchai Wongwises, "Experimental Study on the Thermal Performance of a Battery Thermal Management System Using Heat Pipes," Case Studies in Thermal Engineering, vol. 26, pp. 1-12, 2021.[CrossRef] [Google Scholar] [Publisher Link]