Parametric Optimization and Microhardness Analysis in DED Single-layer Stellite-6
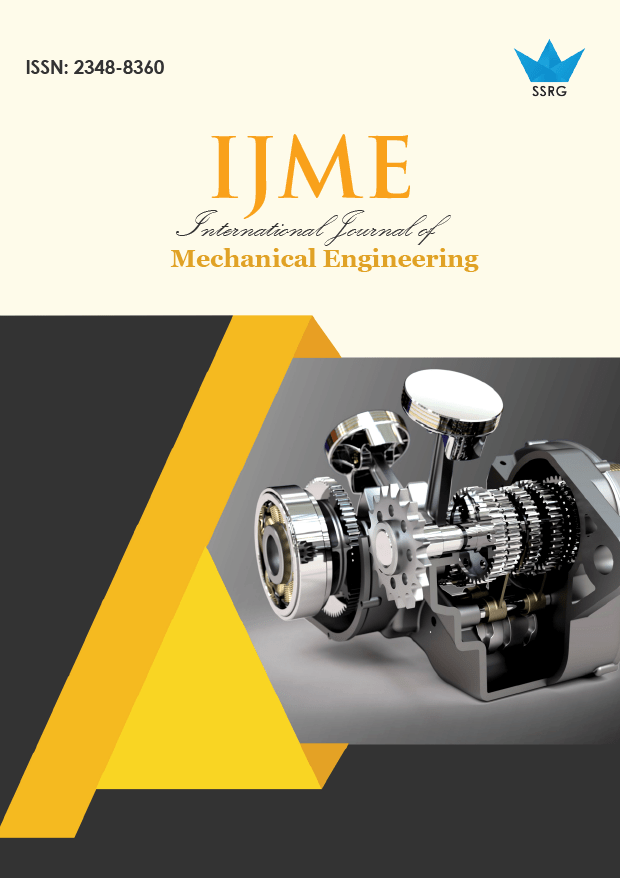
International Journal of Mechanical Engineering |
© 2024 by SSRG - IJME Journal |
Volume 11 Issue 9 |
Year of Publication : 2024 |
Authors : Sunil V. Patel, Chirag P. Patel |
How to Cite?
Sunil V. Patel, Chirag P. Patel, "Parametric Optimization and Microhardness Analysis in DED Single-layer Stellite-6," SSRG International Journal of Mechanical Engineering, vol. 11, no. 9, pp. 53-64, 2024. Crossref, https://doi.org/10.14445/23488360/IJME-V11I9P104
Abstract:
The utilization of Direct Energy Deposition (DED) through the laser cladding process presents a significant opportunity for enhancing the production of high-performance steel. This research delves into the parametric performance and micro-hardness assessment of a Stellite-6 layer deposited onto SS316 substrates via laser coating. Stellite-6 is renowned for its exceptional wear and corrosion resistance, rendering it a favorable option for enhancing the surface of the widely utilized SS316. Studies define the impact of various parameters (such as laser power, laser scan speed, powder quantity, etc.) on the microstructure and micro-hardness characteristics of SS316 and Stellite-6. Micro-hardness evaluations were conducted to ascertain the coating's hardness distribution and area. The interface between the substrate and the coating was also examined. Furthermore, the influence of permeability on coating height and depth was investigated. These findings offer insights into the process quality necessary to attain the desired strength and enhance comprehension of the micro-structural attributes of lasercoated Stellite-6 on SS316 substrate systems.
Keywords:
Direct energy deposition, Micro-hardness analysis, Laser cladding, Stellite-6, SS316.
References:
[1] T.H. Maiman, “Stimulated Optical Radiation in Ruby,” Nature, vol. 187, no. 4736, pp. 493-494, 1960.
[CrossRef] [Google Scholar] [Publisher Link]
[2] T.H. Maiman et al., “Stimulated Optical Emission in Fluorescent Solids. II. Spectroscopy and Stimulated Emission in Ruby,” Physical Review, vol. 123, no. 4, pp. 1151-1157, 1961.
[CrossRef] [Google Scholar] [Publisher Link]
[3] W.M. Steen, “Laser Material Processing-An Overview,” Journal of Optics A: Pure and Applied Optics, vol. 5, no. 4, 2003.
[CrossRef] [Google Scholar] [Publisher Link]
[4] Theodore H. Maiman, “Laser Applications,” Physics Today, vol. 20, no. 7, pp. 24-28, 1967.
[CrossRef] [Google Scholar] [Publisher Link]
[5] W.M. Steen, Laser Material Processing, Germany: Springer, pp. 1-408, 2003.
[Google Scholar] [Publisher Link]
[6] Ehsan Toyserkani, Amir Khajepour, and Stephen F. Corbin, Laser Cladding, 1st ed., CRC Press, pp. 1-280, 2004.
[CrossRef] [Google Scholar] [Publisher Link]
[7] K. Komvopoulos, and K. Nagarathnam, “Processing and Characterization of Laser-Cladded Coating Materials,” Journal of Engineering Materials and Technology, vol. 112, no. 2, pp. 131-143, 1990.
[CrossRef] [Google Scholar] [Publisher Link]
[8] L. Han, K.M. Phatak, and F.W. Liou, “Modeling of Laser Cladding with Powder Injection,” Metallurgical and Materials Transactions B, vol. 35, pp. 1139-1150, 2004.
[CrossRef] [Google Scholar] [Publisher Link]
[9] Liaoyuan Chen et al., “Repair of Spline Shaft by Laser-Cladding Coarse TiC Reinforced Ni-Based Coating: Process, Microstructure and Properties,” Ceramics International, vol. 47, no. 21, pp. 30113-30128, 2021.
[CrossRef] [Google Scholar] [Publisher Link]
[10] Minjie Song et al., “Effects of Laser Cladding on Crack Resistance Improvement for Aluminum Alloy Used in Aircraft Skin,” Optics & Laser Technology, vol. 133, 2021.
[CrossRef] [Google Scholar] [Publisher Link]
[11] Corbin M. Grohol, Yung C. Shin, and Alex Frank, “Laser Cladding of Aluminum Alloy 6061 via Off-Axis Powder Injection,” Surface and Coatings Technology, vol. 145, 2021.
[CrossRef] [Google Scholar] [Publisher Link]
[12] Ehsan Toyserkani, Amir Khajepour, and Stephen Corbin, “3-D Finite Element Modeling of Laser Cladding by Powder Injection: Effects of Laser Pulse Shaping on the Process,” Optics and Lasers in Engineering, vol. 41, no. 6, pp. 849-867, 2004.
[CrossRef] [Google Scholar] [Publisher Link]
[13] Kaiming Wang et al., “Microstructure and Properties of WC Reinforced Ni-Based Composite Coatings with Y2O3 Addition on Titanium Alloy by Laser Cladding,” Science and Technology of Welding and Joining, vol. 24, no. 5, pp. 517-524, 2019.
[CrossRef] [Google Scholar] [Publisher Link]
[14] Jin Ke et al., “Microstructure and Fretting Wear of Laser Cladding Self-Lubricating Anti-Wear Composite Coatings on TA2 Alloy after Aging Treatment,” Optics & Laser Technology, vol. 119, 2019.
[CrossRef] [Google Scholar] [Publisher Link]
[15] Shitanshu Shekhar Chakraborty, and Samik Dutta, “Estimation of Dilution in Laser Cladding Based on Energy Balance Approach Using Regression Analysis,” Sādhanā, vol. 44, 2019.
[CrossRef] [Google Scholar] [Publisher Link]
[16] Ondřej Nenadl et al., “The Prediction of Coating Geometry from Main Processing Parameters in Laser Cladding,” Physics Procedia, vol. 56, pp. 220-227, 2014.
[CrossRef] [Google Scholar] [Publisher Link]
[17] Kaiming Wang et al., “Microstructure and Property of Laser Clad Fe-Based Composite Layer Containing Nb and B4C Powders,” Journal of Alloys and Compounds, vol. 802, pp. 373-384, 2019.
[CrossRef] [Google Scholar] [Publisher Link]
[18] Fuquan Li et al., “Microstructural Study of MMC Layers Produced by Combining Wire and Coaxial WC Powder Feeding in Laser Direct Metal Deposition,” Optics & Laser Technology, vol. 77, pp. 134-143, 2016.
[CrossRef] [Google Scholar] [Publisher Link]
[19] Kaiming Wang et al., “A Study on the Additive Manufacturing of a High Chromium Nickel-Based Superalloy by Extreme High-Speed Laser Metal Deposition,” Optics & Laser Technology, vol. 133, 2021.
[CrossRef] [Google Scholar] [Publisher Link]
[20] Shrey Bhatnagar, Suvradip Mullick, and Muvvala Gopinath, “A Lumped Parametric Analytical Model for Predicting Molten Pool Temperature and Clad Geometry in Pre-Placed Powder Laser Cladding,” Optik, vol. 247, 2021.
[CrossRef] [Google Scholar] [Publisher Link]
[21] Waheed Ul Haq Syed, Andrew J. Pinkerton, and Lin Li, “A Comparative Study of Wire Feeding and Powder Feeding in Direct Diode Laser Deposition for Rapid Prototyping,” Applied Surface Science, vol. 247, no. 1-4, pp. 268-276, 2005.
[CrossRef] [Google Scholar] [Publisher Link]
[22] Adrita Dass, and Atieh Moridi, “State of the Art in Directed Energy Deposition: From Additive Manufacturing to Materials Design,” Coatings, vol. 9, no. 7, pp. 1-26, 2019.
[CrossRef] [Google Scholar] [Publisher Link]
[23] U. de Oliveira, V. Ocelík, and J.Th.M. De Hosson, “Analysis of Coaxial Laser Cladding Processing Conditions,” Surface and Coatings Technology, vol. 197, no. 2-3, pp. 127-136, 2005.
[CrossRef] [Google Scholar] [Publisher Link]
[24] Mingzhong Hao, and Yuwen Sun, “A FEM Model for Simulating Temperature Field in Coaxial Laser Cladding of TI6AL4V Alloy Using an Inverse Modeling Approach,” International Journal of Heat and Mass Transfer, vol. 64, pp. 352-360, 2013.
[CrossRef] [Google Scholar] [Publisher Link]
[25] Chun-Sheng OuYang et al., “Preparation and High Temperature Tribological Properties of Laser In-Situ Synthesized Self-Lubricating Composite Coating on 304 Stainless Steel,” Journal of Materials Research and Technology, vol. 9, no. 4, pp. 7034-7046, 2020.
[CrossRef] [Google Scholar] [Publisher Link]
[26] Xixi Luo et al., “Effect of Line Energy Density of the Laser Beam on the Microstructure and Wear Resistance Properties of the Obtained Fe3Al Laser Cladding Coatings,” Optik, vol. 261, 2022.
[CrossRef] [Google Scholar] [Publisher Link]
[27] Can Huang et al., “Dry Sliding Wear Behavior of Laser Clad TiVCrAlSi High Entropy Alloy Coatings on Ti–6Al–4V Substrate,” Materials & Design, vol. 41, pp. 338-343, 2012.
[CrossRef] [Google Scholar] [Publisher Link]
[28] T.E. Abioye, D.G. McCartney, and A.T. Clare, “Laser Cladding of Inconel 625 Wire for Corrosion Protection,” Journal of Materials Processing Technology, vol. 217, pp. 232-240, 2015.
[CrossRef] [Google Scholar] [Publisher Link]
[29] Gang Wang et al., “Tribological Study of Ti3SiC2/Cu5Si/TiC Reinforced Co-Based Coatings on SUS304 Steel by Laser Cladding,” Surface and Coatings Technology, vol. 432, 2022.
[CrossRef] [Google Scholar] [Publisher Link]
[30] Hussam El Cheikh et al., “Analysis and Prediction of Single Laser Tracks Geometrical Characteristics in Coaxial Laser Cladding Process,” Optics and Lasers in Engineering, vol. 50, no. 3, pp. 413-422, 2012.
[CrossRef] [Google Scholar] [Publisher Link]
[31] M.J. Hamedi, M.J. Torkamany, and J. Sabbaghzadeh, “Effect of Pulsed Laser Parameters on In-Situ TiC Synthesis in Laser Surface Treatment,” Optics and Lasers in Engineering, vol. 49, no. 4, pp. 557-563, 2011.
[CrossRef] [Google Scholar] [Publisher Link]
[32] André A. Ferreira et al., “Optimization of Direct Laser Deposition of a Martensitic Steel Powder (Metco 42C) on 42CrMo4 Steel,” Metals, vol. 11, no. 4, pp. 1-18, 2021.
[CrossRef] [Google Scholar] [Publisher Link]
[33] Bo Shan et al., “Laser Cladding of Fe-Based Corrosion and Wear-Resistant Alloy: Genetic Design, Microstructure, and Properties,” Surface and Coatings Technology, vol. 433, 2022.
[CrossRef] [Google Scholar] [Publisher Link]
[34] Zhengtao Gan et al., “Numerical Simulation of Thermal Behavior and Multicomponent Mass Transfer in Direct Laser Deposition of Co-Base Alloy on Steel,” International Journal of Heat and Mass Transfer, vol. 104, pp. 28-38, 2017.
[CrossRef] [Google Scholar] [Publisher Link]
[35] Damian Janicki, “Laser Cladding of Inconel 625-Based Composite Coatings Reinforced by Porous Chromium Carbide Particles,” Optics & Laser Technology, vol. 94, pp. 6-14, 2017.
[CrossRef] [Google Scholar] [Publisher Link]
[36] Fuxing Fu et al., “Analysis on the Physical Mechanism of Laser Cladding Crack and its Influence Factors,” Optik, vol. 127, no. 1, pp. 200-202, 2016.
[CrossRef] [Google Scholar] [Publisher Link]
[37] Prabu Balu et al., “Multi-Response Optimization of Laser-Based Powder Deposition of Multi-track Single Layer Hastelloy C-276,” Materials and Manufacturing Processes, vol. 28, no. 2, pp. 173-182, 2013.
[CrossRef] [Google Scholar] [Publisher Link]
[38] B. Cárcel et al., “Laser Cladding of TiAl Intermetallic Alloy on Ti6Al4V -Process Optimization and Properties,” Physics Procedia, vol. 56, pp. 284-293, 2014.
[CrossRef] [Google Scholar] [Publisher Link]
[39] Zhenguo Nie et al., “Experimental Study and Modeling of H13 Steel Deposition Using Laser Hot-Wire Additive Manufacturing,” Journal of Materials Processing Technology, vol. 235, pp. 171-186, 2016.
[CrossRef] [Google Scholar] [Publisher Link]
[40] C.J. Todaro et al., “Grain Structure Control During Metal 3D Printing by High-Intensity Ultrasound,” Nature Communications, vol. 11, no. 1, pp. 1-9, 2020.
[CrossRef] [Google Scholar] [Publisher Link]
[41] Guangyi Ma et al., “Microstructure Evolution and Mechanical Properties of Ultrasonic Assisted Laser Clad Yttria Stabilized Zirconia Coating,” Ceramics International, vol. 43, no. 13, pp. 9622-9629, 2017.
[CrossRef] [Google Scholar] [Publisher Link]
[42] Victor Geanta et al., “Chemical Composition Influence on Microhardness, Microstructure and Phase Morphology of AlxCrFeCoNi High Entropy Alloys,” Revista de Chimie, vol. 69, no. 4, pp. 798-801, 2018.
[CrossRef] [Google Scholar] [Publisher Link]
[43] S. Zhang, C.L. Wu, and C.H. Zhang, “Phase Evolution Characteristics of FeCoCrAlCuVxNi High Entropy Alloy Coatings by Laser High-Entropy Alloying,” Materials Letters, vol. 141, pp. 7-9, 2015.
[CrossRef] [Google Scholar] [Publisher Link]
[44] Prakash Kattire et al., “Experimental Characterization of Laser Cladding of CPM 9V on H13 Tool Steel for Die Repair Applications,” Journal of Manufacturing Processes, vol. 20, no. 3, pp. 492-499, 2015.
[CrossRef] [Google Scholar] [Publisher Link]
[45] H. Zhang et al., “Laser Cladding of Colmonoy 6 Powder on AISI316L Austenitic Stainless Steel,” Nuclear Engineering and Design, vol. 240, no. 10, pp. 2691-2696, 2010.
[CrossRef] [Google Scholar] [Publisher Link]
[46] P. Prokhorenko, N. Migun, and N. Dezhkunov, “Development of Penetrant Test Theory Based on New Physical Effects,” Non-Destructive Testing '92, pp. 538-542, 1992.
[CrossRef] [Google Scholar] [Publisher Link]