Numerical Investigation of Deep Drawing Process by Response Surface Methodology
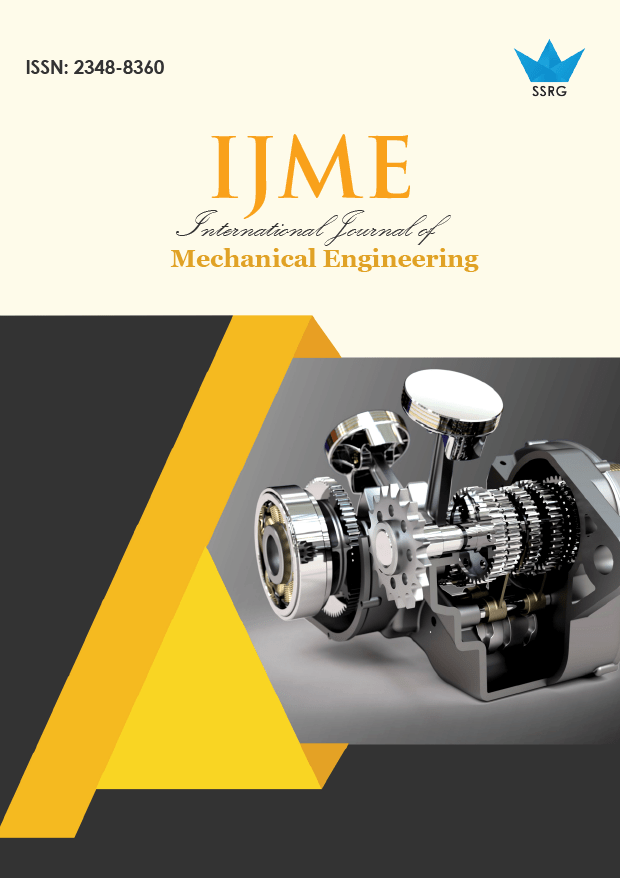
International Journal of Mechanical Engineering |
© 2024 by SSRG - IJME Journal |
Volume 11 Issue 11 |
Year of Publication : 2024 |
Authors : Mehul V Ardeshana, Jaydeep K Dadhaniya |
How to Cite?
Mehul V Ardeshana, Jaydeep K Dadhaniya, "Numerical Investigation of Deep Drawing Process by Response Surface Methodology," SSRG International Journal of Mechanical Engineering, vol. 11, no. 11, pp. 61-66, 2024. Crossref, https://doi.org/10.14445/23488360/IJME-V11I11P106
Abstract:
Deep drawing is used widely to manufacture objects out of sheet metal. Several geometric parameters can generate deep drawing products that are free of defects. The radius of the Punch corner, Clearance and radius of the die corner are the three parameters that have the biggest effects on deep drawing. The stress distribution of an SS 316 cylindrical cup was examined in this study while considering these parameters. The finite element simulation of this process is performed in ABAQUS software. FEM simulation using the isotropic hardening law was carried out. Response surface methodology is used to design experiments. When the outcomes of the FEA and the experiments were compared, they agreed well. The most influential parameters were identified by ANOVA analysis. The finding showed that the optimum parameter of the punch corner radius (PCR) should be 5.3 mm, the Die Corner Radius (DCR) should be 6.6 mm, and clearance should be 1.07 mm to minimize stress distribution.
Keywords:
Deep drawing, Punch corner radius, Die corner radius, Response surface methodology, Stress distribution.
References:
[1] Bora Şener, and Hasan Kurtaran, “Modeling the Deep Drawing of an AISI 304 Stainless-Steel Rectangular Cup Using the Finite-Element Method and an Experimental Validation,” Materiali in Tehnologije, vol. 50, no. 6, pp. 961-965, 2016.
[CrossRef] [Google Scholar] [Publisher Link]
[2] M. T. Browne, and M. T. Hillery, “Optimising the Variables When Deep-Drawing C.R.1 Cups,” Journal of Materials Processing Technology, vol. 136, no. 1-3, pp. 64-71, 2003.
[CrossRef] [Google Scholar] [Publisher Link]
[3] H. Zein et al., “Effect of Die Design Parameters on Thinning of Sheet Metal in the Deep Drawing Process,” American Journal of Mechanical Engineering, vol. 1, no. 2, pp. 20-29, 2013.
[CrossRef] [Google Scholar] [Publisher Link]
[4] Waleed Khalid Jawad, “Investigation of Contact Interface between the Punch and Blank in Deep Drawing Process,” Engineering and Technology Journal, vol. 25, no. 3, pp. 370-382, 2007.
[Google Scholar] [Publisher Link]
[5] Masoud Mahmoodi et al., “Using the Artificial Neural Network to Investigate the Effect of Parameters in Square Cup Deep Drawing of Aluminum-Steel Laminated Sheets,” International Journal of ISSI, vol. 17, no. 2, pp. 1-13, 2020.
[CrossRef] [Google Scholar] [Publisher Link]
[6] Yanmin Xie et al., “Multi-Objective Optimization of Process Parameters in Stamping Based on an Improved RBM–BPNN Network and MOPSO Algorithm,” Structural and Multidisciplinary Optimization, vol. 64, no. 6, pp. 4209-4235, 2021.
[CrossRef] [Google Scholar] [Publisher Link]
[7] Takalkar Atul S, and Lenin Babu Mailan Chinnapandi, “Formability Prediction of the Al1050/SS304 Sandwich Composite Sheet by Using a Numerical and Experimental Approach,” Advances in Materials and Processing Technologies, vol. 7, no. 4, pp. 567-590, 2020.
[CrossRef] [Google Scholar] [Publisher Link]
[8] Philippa M. Horton et al., “An Experimental Analysis of the Relationship between the Corner, Die and Punch Radii in Forming Isolated Flanged Shrink Corners from Al 5251,” Journal of Materials Processing Technology, vol. 278, 2020.
[CrossRef] [Google Scholar] [Publisher Link]
[9] Ihsan Irthiea, and Zaid Mahmood, “Effect of process parameters on micro flexible deep drawing of stainless steel 304 cups utilizing floating ring: Simulation and experiments,” Proceedings of the Institution of Mechanical Engineers, Part B: Journal of Engineering Manufacture, vol. 235, no. 1-2, pp. 134-143, 2021.
[CrossRef] [Google Scholar] [Publisher Link]
[10] Liang Luo et al., “Influence of Blank Holder-Die Gap on Micro-Deep Drawing of SUS304 Cups,” International Journal of Mechanical Sciences, vol. 191, 2021.
[CrossRef] [Google Scholar] [Publisher Link]
[11] N. M. Yusop and A. B. Abdullah, “Evaluation of square deep drawn AA6061-T6 Blank Based on Thinning Pattern,” IOP Conference Series: Materials Science and Engineering, vol. 670, no. 1, 2019.
[CrossRef] [Google Scholar] [Publisher Link]
[12] M. Gavas and M. Izciler, “Design and Application of Blank Holder System with Spiral Spring in Deep Drawing of Square Cups,” Journal of Materials Processing Technology, vol. 171, no. 2, pp. 274-282, 2006.
[CrossRef] [Google Scholar] [Publisher Link]
[13] Wang Wu-rong, Chen Guan-long, and Lin Zhong-qin, “The Effect of Binder Layouts on the Sheet Metal Formability in the Stamping with Variable Blank Holder Force,” Journal of Materials Processing Technology, vol. 210, no. 10, pp. 1378-1385, 2010.
[CrossRef] [Google Scholar] [Publisher Link]
[14] Søren Tommerup, and Benny Endelt, “Experimental Verification of a Deep Drawing Tool System for Adaptive Blank Holder Pressure Distribution,” Journal of Materials Processing Technology, vol. 212, no. 11, pp. 2529-2540, 2012.
[CrossRef] [Google Scholar] [Publisher Link]
[15] Lucian Lazarescu, Ioan Nicodim, and Dorel Banabic, “Evaluation of Drawing Force and Thickness Distribution in the Deep-Drawing Process with Variable Blank-Holding,” Key Engineering Materials, vol. 639, pp. 33-40, 2015.
[CrossRef] [Google Scholar] [Publisher Link]
[16] L. Chen et al., “Finite Element Simulation and Model Optimization of Blankholder Gap and Shell Element Type in the Stamping of a Washing-Trough,” Journal of Materials Processing Technology, vol. 182, no. 1-3, pp. 637-643, 2007.
[CrossRef] [Google Scholar] [Publisher Link]
[17] Masoud Kardan, Ali Parvizi, and Ali Askari, “Influence of Process Parameters on Residual Stresses in Deep-Drawing Process with FEM and Experimental Evaluations,” Journal of the Brazilian Society of Mechanical Sciences and Engineering, vol. 40, no. 3, 2018.
[CrossRef] [Google Scholar] [Publisher Link]
[18] Minh Tien Tran et al., “Earing Reduction by Varying Blank Holding Force in Deep Drawing with Deep Neural Network,” Metals, vol. 11, no. 3, 2021.
[CrossRef] [Google Scholar] [Publisher Link]