Experimental Analysis for the Surface Roughness Improvement of Bearing Steel SAE 52100 Using Magnetic Abrasive Finishing Process
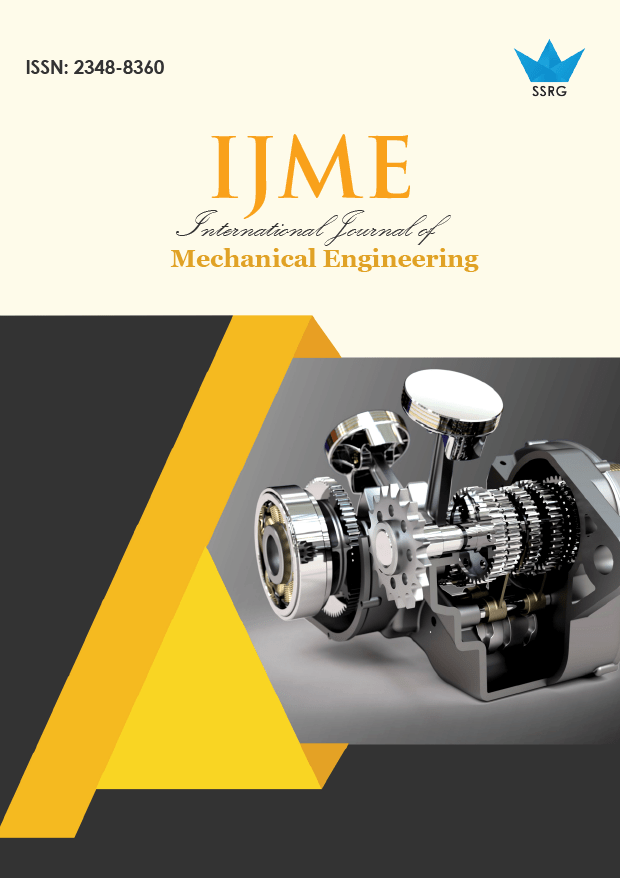
International Journal of Mechanical Engineering |
© 2025 by SSRG - IJME Journal |
Volume 12 Issue 1 |
Year of Publication : 2025 |
Authors : Rajendra E. Kalhapure, Gaurav Kumar Gugliani, Ravindra R. Navthar, Prashant N. Nagare |
How to Cite?
Rajendra E. Kalhapure, Gaurav Kumar Gugliani, Ravindra R. Navthar, Prashant N. Nagare, "Experimental Analysis for the Surface Roughness Improvement of Bearing Steel SAE 52100 Using Magnetic Abrasive Finishing Process," SSRG International Journal of Mechanical Engineering, vol. 12, no. 1, pp. 43-48, 2025. Crossref, https://doi.org/10.14445/23488360/IJME-V12I1P105
Abstract:
52100 bearing steel is mainly used in various applications, including seal rings, sleeves, bearings, balls, bearing races, rollers, guide bars, and knives, among others. Traditional finishing processes might be difficult to perform when making diverse components in varied forms and sizes. This aims to employ advanced fine machining and finishing procedures. Magnetic abrasive finishing is one of the precision fine-finishing approaches that yield exceptionally high-quality components. This process employs a flexible magnetic abrasive brush that is guided by a DC magnetized field to achieve desired results. The magnetized abrasives utilized in this fine-finishing process generally consist of two components: ferromagnetic material and abrasive particles, which must be interconnected. In this study, 52100 steel bars are fine-finished on a Magnetic abrasive finishing setup using multiple process variables. For this investigation, an Aluminum oxide (Al2O3) is used as an abrasive for this micro-finishing process. Variables such as magnetic density, workpiece rotating speed, and abrasive mixer can be easily varied to research greater surface finishes. The success of the process is determined by elements such as abrasive particle contents in mixing ratio, workpiece speed, and the input DC power source for magnetic flux density. The testing results reveal that the surface roughness of 52100 bearing steel rods improved with a high voltage of 36V and a rotational speed of 1026 rpm. Experiments demonstrate that raising the voltage and rotating speed improves surface roughness by a greater percentage.
Keywords:
Flexible magnetic, Abrasive brush, Magnetic Abrasive Fine-finishing, DC electromagnet, Surface roughness.
References:
[1] Ik-Tae Im, Sang Don Mun, and Seong Mo Oh, “Micro Machining of an STS 304 Bar by Magnetic Abrasive Finishing,” Journal of Mechanical Science and Technology, vol. 23, no. 7, pp. 1982-1988, 2009.
[CrossRef] [Google Scholar] [Publisher Link]
[2] Yuri M .Baron, Sung Lim Ko, and Elena Repnikova, “Experimental Verification of Deburring by Magnetic Abrasive Finishing Method. St,” Petersburg State Polytechnical University, Dr. Sc, Prof, Polytechnichskaya Str 29, 2001.
[Google Scholar]
[3] Yuri Mikhailovich Baron, S.L. Ko, and Jung Il Park, “Characterization of the Magnetic Abrasive Finishing Method and its Application to Deburring,” Key Engineering Materials, vol. 291-292, pp. 291-296, 2005.
[CrossRef] [Google Scholar] [Publisher Link]
[4] Zhen-Bing Hou, and R. Komanduri, “Magnetic Field Assisted Finishing of Ceramics—Part III: On the Thermal Aspects of Magnetic Abrasive Finishing (MAF) of Ceramic Rollers,” Journal of Tribology, vol. 120, no. 4, pp. 660-667, 1998.
[CrossRef] [Google Scholar] [Publisher Link]
[5] T. Deaconescu, and A. Deaconescu, “Equipment for Magneto-Abrasive Finishing of Roller Bearing Balls,” 6th International DAAAM Baltic Conference INDUSTRIAL ENGINEERING, Tallinn, Estonia, pp. 1-6, 2008.
[Google Scholar] [Publisher Link]
[6] Jae-Seob Kwak, “Enhanced Magnetic Abrasive Polishing of Non-Ferrous Metals Utilizing a Permanent Magnet,” International Journal of Machine Tools and Manufacture, vol. 49, no. 7-8, pp. 613-618, 2009.
[CrossRef] [Google Scholar] [Publisher Link]
[7] Kanish T.C. et al., “Experimental Investigations on Magnetic Field Assisted Abrasive Finishing of SS 316l,” Procedia Manufacturing, vol. 30, pp. 276-283, 2019.
[CrossRef] [Google Scholar] [Publisher Link]
[8] Yuewu Gao et al., “Modeling of Material Removal in Magnetic Abrasive Finishing Process with Spherical Magnetic Abrasive Powder,” International Journal of Mechanical Sciences, vol. 177, 2020.
[CrossRef] [Google Scholar] [Publisher Link]
[9] R.S. Mulik, and P.M. Pandey, “Experimental Investigations Into the Finishing Force and Torque in Magnetic Abrasive Finishing Process,” ASME 2013 International Mechanical Engineering Congress and Exposition, San Diego, California, USA, 2013.
[CrossRef] [Google Scholar] [Publisher Link]
[10] Er. Rohit Rampala, and Dr. Tarun Goyal, “Fabricating the Magnetic Abrasive Finishing Setup on Lathe,” International Journal For Applied Research in Science and Engineering, vol. 6, no. 12, pp. 1361-1366, 2017.
[Publisher Link]