Improvement Model of OEE in the Production Process of Cardboard Boxes Through SMED, TPM, Automation, and IoT
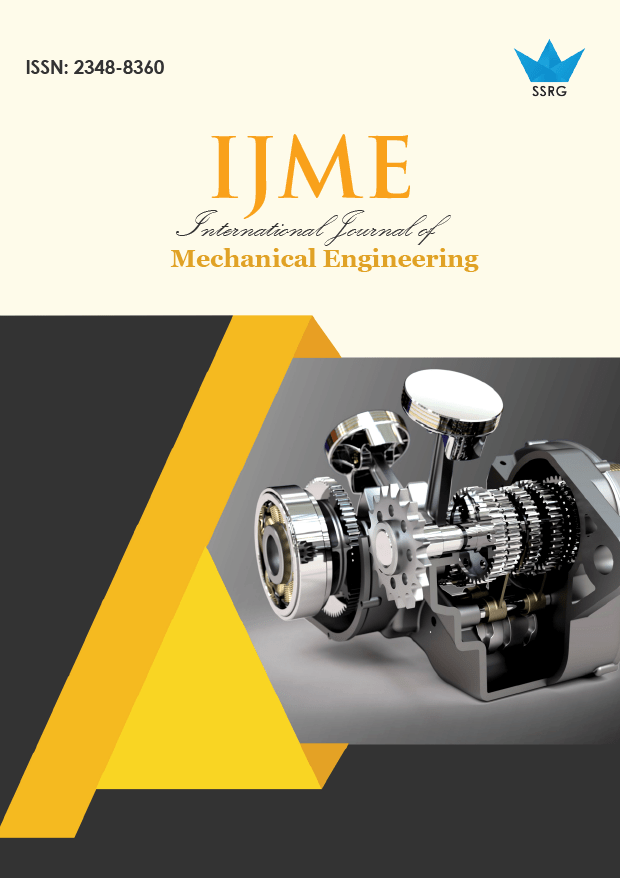
International Journal of Mechanical Engineering |
© 2025 by SSRG - IJME Journal |
Volume 12 Issue 6 |
Year of Publication : 2025 |
Authors : Rolando Gonzales-Vera, Karol Rodriguez-Barrientos, Percy Castro-Rangel, José C. Alvarez, Robert Lepore |
How to Cite?
Rolando Gonzales-Vera, Karol Rodriguez-Barrientos, Percy Castro-Rangel, José C. Alvarez, Robert Lepore, "Improvement Model of OEE in the Production Process of Cardboard Boxes Through SMED, TPM, Automation, and IoT," SSRG International Journal of Mechanical Engineering, vol. 12, no. 6, pp. 34-51, 2025. Crossref, https://doi.org/10.14445/23488360/IJME-V12I6P104
Abstract:
As processes become more complex, measuring them using key KPI indicators, such as Overall Equipment Effectiveness (OEE), is essential. This study analyses the OEE of the cardboard box production process-the product with the highest annual revenue in a Peruvian printing company. The current OEE is 64.27%, which falls short of the graphic industry standard (72.5%). Increasing the OEE would provide several benefits, such as higher availability, improved product quality, reduced setup times, and lower machine wear. Therefore, an innovative solution model is proposed that will use SMED and TPM tools, as well as Automation and IoT technologies. These Lean tools will be enhanced through the mentioned technologies. The solution model will follow the PMBOK approach due to its significant contributions to project management and will consist of three phases: initial, implementation, and closure. Improvements will be projected for key SMART indicators that are identified. Subsequently, these improvements will be validated through simulation in Arena software across three scenarios: moderate, optimistic, and pessimistic. All three scenarios will show improvements over the current OEE, approaching the industry standard. Setup time in die-cutting was reduced to 836.69 minutes, die-cutter wear decreased to 24.58%, and lubricant usage in guillotines and offset machines increased to 255.04 ml and 569.21 ml, respectively.
Keywords:
OEE, TPM, SMED, Automation, IoT, Graphic Sector.
References:
[1] Roberto Giani Pattaro Junior et al., “A Novel Framework for Single-Minute Exchange of Die (SMED) Assisted by Lean Tools,” The International Journal of Advanced Manufacturing Technology, vol. 119, pp. 6469-6487, 2022.
[CrossRef] [Google Scholar] [Publisher Link]
[2] Guillermo Garcia-Garcia, Yadvinder Singh, and Sandeep Jagtap, “Optimising Changeover through Lean-Manufacturing Principles: A Case Study in a Food Factory,” Sustainability, vol. 14, no. 14, pp. 1-20, 2022.
[CrossRef] [Google Scholar] [Publisher Link]
[3] Vitor Santos et al., “Applying the SMED Methodology to Tire Calibration Procedures,” Systems, vol. 10, no. 6, pp. 1-12, 2022.
[CrossRef] [Google Scholar] [Publisher Link]
[4] Viren Parwani, and Guiping Hu, “Improving Manufacturing Supply Chain by Integrating SMED and Production Scheduling,” Logistics, vol. 5, no. 1, pp. 1-14, 2021.
[CrossRef] [Google Scholar] [Publisher Link]
[5] Diego Augusto de Jesus Pacheco, and Giovana Di Giorgio Heidrich, “Revitalising the Setup Reduction Activities in Operations Management,” Production Planning and Control, vol. 34, no. 9, pp. 791-811, 2021.
[CrossRef] [Google Scholar] [Publisher Link]
[6] Marcela Malindzakova, Dusan Malindzak, and Patrick Garaj, “Implementation of the Single Minute Exchange of Dies Method for Reducing Changeover Time in a Hygiene Production Company,” International Journal of Industrial Engineering and Management, vol. 12, no. 4, pp. 243–252, 2021.
[CrossRef] [Google Scholar] [Publisher Link]
[7] Pavel Ondra, “The Impact of Single Minute Exchange of Die and Total Productive Maintenance on Overall Equipment Effectiveness,” Journal of Competitiveness, vol. 14, no. 2, pp. 113–132, 2022.
[CrossRef] [Google Scholar] [Publisher Link]
[8] Jovana Nikolić, Marica Dašić, and Marko Đapan, “Smed as an Indispensable Part of Lean Manufacturing in the Small and Medium Enterprises,” International Journal for Quality Research, vol. 17, no. 1, pp. 255–270, 2023.
[CrossRef] [Google Scholar] [Publisher Link]
[9] Jagdeep Singh, and Harwinder Singh, “Justification of TPM Pillars for Enhancing the Performance of Manufacturing Industry of Northern India,” International Journal of Productivity and Performance Management, vol. 69, no. 1, pp. 109–133, 2020.
[CrossRef] [Google Scholar] [Publisher Link]
[10] Filip Hardt et al., “Innovative Approach to Preventive Maintenance of Production Equipment Based on a Modified TPM Methodology for Industry 4.0,” Applied Sciences, vol. 11, no. 15, pp. 1-17, 2021.
[CrossRef] [Google Scholar] [Publisher Link]
[11] David Mendes et al., “Integrating TPM and Industry 4.0 to Increase the Availability of Industrial Assets: A Case Study on a Conveyor Belt,” Processes, vol. 11, no. 7, pp. 1-21, 2023.
[CrossRef] [Google Scholar] [Publisher Link]
[12] Edward Michlowicz, “Assessment of the Modernized Production System through Selected TPM Method Indicators,” Eksploatacja i Niezawodnosc, vol. 24, no. 4, pp. 677–686, 2022.
[CrossRef] [Google Scholar] [Publisher Link]
[13] Omar Bataineh et al., “A Sequential TPM-based Scheme for Improving Production Effectiveness Presented with a Case Study,” Journal of Quality in Maintenance Engineering, vol. 25, no. 1, pp. 144–161, 2019.
[CrossRef] [Google Scholar] [Publisher Link]
[14] P. Marinho et al., “Selecting the Best Tools and Framework to Evaluate Equipment Malfunctions and Improve the OEE in the Cork Industry,” International Journal of Industrial Engineering and Management, vol. 12, no. 4, pp. 286–298, 2021.
[CrossRef] [Google Scholar] [Publisher Link]
[15] Muhammad Zubair et al., “Manufacturing Productivity Analysis by Applying Overall Equipment Effectiveness Metric in a Pharmaceutical Industry,” Cogent Engineering, vol. 8, no. 1, 2021.
[CrossRef] [Google Scholar] [Publisher Link]
[16] Chew Keat Cheah, Joshua Prakash, and Kok Seng Ong, “An Integrated OEE Framework for Structured Productivity Improvement in a Semiconductor Manufacturing Facility,” International Journal of Productivity and Performance Management, vol. 69, no. 5, pp. 1081–1105, 2020.
[CrossRef] [Google Scholar] [Publisher Link]
[17] Myriam Ertz, and Florian Gasteau, “Role of Smart Technologies for Implementing Industry 4.0 Environment in Product Lifetime Extension Towards Circular Economy: A Qualitative Research,” Heliyon, vol. 9, no. 6, pp. 1-17, 2023.
[CrossRef] [Google Scholar] [Publisher Link]
[18] Juan Sebastian Bravo-Paliz, and Sonia Valeria Avilés-Sacoto, “Characterizing the Integration of BRC Food Safety Certification and Lean Tools: The Case of an Ecuadorian Packaging Company,” The TQM Journal, vol. 35, no. 4, pp. 872-892, 2023.
[CrossRef] [Google Scholar] [Publisher Link]
[19] Raja Chandra Sekar Mariappan et al., “Intelligent VSM Model: A Way to Adopt Industry 4.0 Technologies in Manufacturing Industry,” International Journal of Advanced Manufacturing Technology, vol. 129, pp. 2195–2214, 2023.
[CrossRef] [Google Scholar] [Publisher Link]
[20] Gerardo Luisi et al., “A Hybrid Architectural Model for Monitoring Production Performance in the Plastic Injection Molding Process,” Applied Sciences, vol. 13, no. 22, pp. 1-16, 2023.
[CrossRef] [Google Scholar] [Publisher Link]
[21] Husam Kaid et al., “A Novel Method for Converting Colored Petri Nets to Ladder Diagram in the Automation of Automated Manufacturing Systems,” IEEE Access, vol. 11, pp. 29275–29295, 2023.
[CrossRef] [Google Scholar] [Publisher Link]
[22] Philipp Gönnheimer et al., “Interoperable System for Automated Extraction and Identification of Machine Control Data in Brownfield Production,” Manufacturing Letters, vol. 35, pp. 915–925, 2023.
[CrossRef] [Google Scholar] [Publisher Link]
[23] Rita Martinho et al., “IoT Based Automatic Diagnosis for Continuous Improvement,” Sustainability, vol. 14, no. 15, pp. 1-28, 2022.
[CrossRef] [Google Scholar] [Publisher Link]
[24] David Mendes et al., “Enhanced Real-Time Maintenance Management Model—A Step toward Industry 4.0 through Lean: Conveyor Belt Operation Case Study,” Electronics, vol. 12, no. 18, pp. 1-14, 2023.
[CrossRef] [Google Scholar] [Publisher Link]
[25] Sehnaz Ahmetoglu, Zaihisma Che Cob, and Nor Ashikin Ali, “Internet of Things Adoption in the Manufacturing Sector: A Conceptual Model from a Multi-Theoretical Perspective,” Applied Sciences, vol. 13, no. 6, pp. 1-21, 2023.
[CrossRef] [Google Scholar] [Publisher Link]
[26] Mohammad Ahsan Habib, Ratul Rizvan, and Shamsuddin Ahmed, “Implementing Lean Manufacturing for Improvement of Operational Performance in a Labeling and Packaging Plant: A Case Study in Bangladesh,” Results in Engineering, vol. 17, 2023.
[CrossRef] [Google Scholar] [Publisher Link]
[27] Chen-Yang Cheng et al., “Smart Monitoring of Manufacturing Systems for Automated Decision‐making: A Multi‐Method Framework,” Sensors, vol. 21, no. 20, pp. 1-14, 2021.
[CrossRef] [Google Scholar] [Publisher Link]
[28] Noel Shannon et al., “A Total Productive Maintenance & Reliability Framework for an Active Pharmaceutical Ingredient Plant Utilising Design for Lean Six Sigma,” Heliyon, vol. 9, no. 10, 2023.
[CrossRef] [Google Scholar] [Publisher Link]
[29] C. Jaqin, A. Rozak, and H. Hardi Purba, “Case Study in Increasing Overall Equipment Effectiveness on Progressive Press Machine Using Plan-do-Check-Act Cycle,” International Journal of Engineering, vol. 33, no. 11, pp. 2245–2251, 2020.
[CrossRef] [Google Scholar] [Publisher Link]
[30] Patrick Ruane, Patrick Walsh, and John Cosgrove, “Development of a Digital Model and Metamodel to Improve the Performance of an Automated Manufacturing Line,” Journal of Manufacturing Systems, vol. 65, pp. 538–549, 2022.
[CrossRef] [Google Scholar] [Publisher Link]"
[31] Tamer Haddad, Basheer W. Shaheen, and Istvan Németh, “Improving Overall Equipment Effectiveness (OEE) of Extrusion Machine Using Lean Manufacturing Approach,” Manufacturing Technology, vol. 21, no. 1, pp. 56–64, 2021.
[CrossRef] [Google Scholar] [Publisher Link]
[32] Jalal Possik et al., “Lean Techniques Impact Evaluation Methodology Based on a Co-simulation Framework for Manufacturing Systems,” International Journal of Computer Integrated Manufacturing, vol. 35, no. 1, pp. 91-111, 2022.
[CrossRef] [Google Scholar] [Publisher Link]
[33] Lisbeth Del Carmen Ng Corrales et al., “Overall Equipment Effectiveness: Systematic Literature Review and Overview of Different Approaches,” Applied Sciences, vol. 10, no. 18, pp. 1-20, 2020.
[CrossRef] [Google Scholar] [Publisher Link]
[34] Julien Polge, Jeremy Robert, and Yves Le Traon, “A Case Driven Study of the Use of Time Series Classification for Flexibility in Industry 4.0,” Sensors, vol. 20, no. 24, pp. 1-22, 2020.
[CrossRef] [Google Scholar] [Publisher Link]