Weight Optimization of Lathe Bed by Design Modification and Epoxy Granite
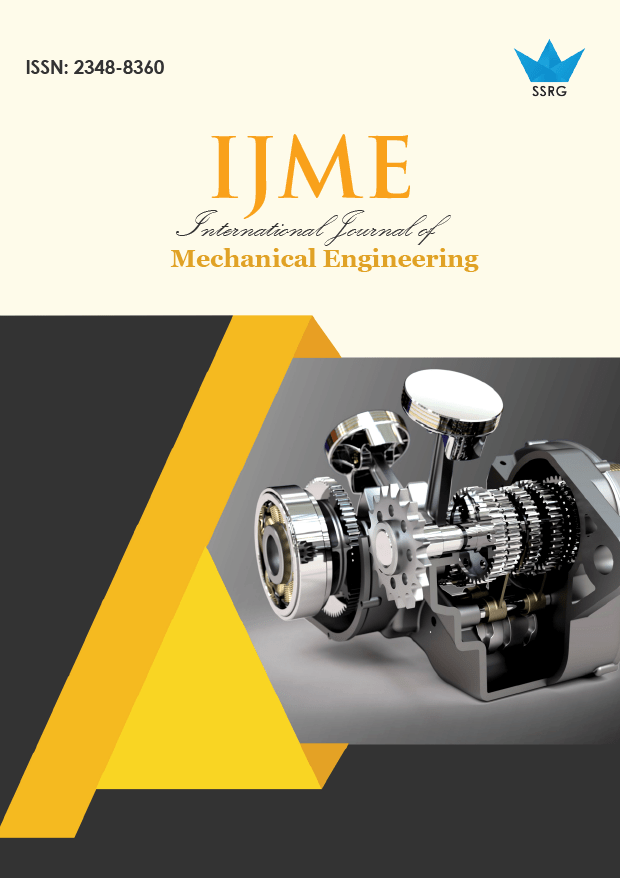
International Journal of Mechanical Engineering |
© 2017 by SSRG - IJME Journal |
Volume 4 Issue 7 |
Year of Publication : 2017 |
Authors : Juturi Saidaiah, Bhukya Biksham, Kanaparthi Veeranjaneyulu |
How to Cite?
Juturi Saidaiah, Bhukya Biksham, Kanaparthi Veeranjaneyulu, "Weight Optimization of Lathe Bed by Design Modification and Epoxy Granite," SSRG International Journal of Mechanical Engineering, vol. 4, no. 7, pp. 23-32, 2017. Crossref, https://doi.org/10.14445/23488360/IJME-V4I7P107
Abstract:
Lathe bed acts as the base on which the different fixed and movable parts of the Lathe are mounted. Lathe beds are usually manufactured with Cast iron or Mild steel. In case of extremely large machines, the bed may be in two or more pieces, bolted together to from the desired length. Lathe Bed is heavy rigid structure which is having high damping capacity for the vibrations generated by machines during machining. In this project, static structural and modal analyses are carried out on lathe bed at maximum load conditions. These simulation results are used to reduce the weight of the lathe bed without deteriorating its structural strength and damping capacity by adding ribs and removing mass where less deformation and stresses are induced. FEA analysis of modified lathe bed is carried out with Gray cast iron and Epoxy-granite which is a mixture of granite and epoxy resin-hardener as an alternative material. Effectiveness of both materials are compared in terms of induced stresses, deformation and weight reduction. Lathe bed CAD models have been generated with Creo modeling software. The FE model has been generated by ANSYS APDL. The analyses are carried out using ANSYS APDL. The results are shown in the form of contour plots and also tabulated, to analyse the effect of weight reduction on the structural integrity of the machine bed before and after the weight reduction and conclusions are drawn about the optimized design.
Keywords:
Weight optimization, Lathe bed, FE Analysis, Epoxy-granite
References:
1. S. Kalpakjan, Manufacturing Engineering and Technology, 3rd Edition, Addison-Wesley, Reading, MA, 1995.
2. Structural Bionic Design and Experimental Verification of a Machine Tool Column, Ling Zhao, Wu-yi Chen, Jian feng Ma, Yong-bin Yang, Journal of Bionic Engineering Suppl. (2008) 46–52.
3. Damping characteristics of composite hybrid spindle covers for high speed machine tools Jung Do Suha, Seung Hwan Changa, Dai Gil Leea, Jin Kyung Choib and Bo Seon Parkc , Journal of Materials Processing Technology, Volume 113, Issues 1-3, 15 June (2001), Pages 178-183.
4. Myo Min Zaw “Strength Analysis of Bed ways for CNC Lathe Machine” GMSARN International Conference on Sustainable Development: Issue and Prospects for the GMS 12-14 Nov.(2008).
5. Bernard Budiansky, “On the minimum weights of compression structures”, in International Journal of Solids and Structures, volume 36, (1999), pp. 3677- 3708.
6. Chang S H, Kim P J, Lee D G, Chol J K. Steel composite hybrid headstock for high-precision grinding machine. Composite Structures, (2001), 53, 1-8.
7. Lee D G, Chang S H, Kim H S. Damping improvement of machine tool columns with polymer matrix fiber composite material. Composite Structures, (1998), 43,155 63.
8. The Machine Tool Industry Research Association, A Dynamic Performance Test for Lathes, July, 1-86, (1971). 9. Welbourn, D.B. and Smith, J.D., “Machine Tool Dynamics, Cambridge University Press,Chap.1, Chap.5, Chap.8, (1970).
10. Koenigs berger, F. and Tlusty, J., “Machine Tool Structures”, Pergamon Press, Vol.1,Sect .2, (1970).
11. Cook, N.H., “Manufacturing Analysis, Addison- Wesley Publishing Company, Chap.3, Chap.7., (1986).
12. Kim D I., Jung S C, Lee J E. Parametric study on design of composite-foam-resin concrete sandwich structures for precision machine tool structures. Composite Structures, (2006), 75, 408-414.
13. TAPAN A PANDYA, M. Tech, "Evaluation of alternative material for lathe bed" May 2016.